– Vi har vist at membranteknologien fungerer, og håper den blir med i neste testfase i Brevik, sier May-Britt Hägg, professor ved Institutt for kjemisk prosessteknologi, NTNU.
Membranteknologi utviklet ved NTNU er en av de fire aktuelle teknologiene som kan bli tatt i bruk ved fullskala CO2-håndtering.
CO2-fangst fra sementproduksjon
De fire teknologiene som testes i prosjektet er:
- Aminer (Aker Solutions)
- Membraner (NTNU, SINTEF, DNV GL, Air Products)
- Kalsiumsyklus (Alstom)
- Faststoffabsorbent (Research Triangle Institute, USA)
Norcem er vert og tilrettelegger for prosjektet. Det finansieres med 65 prosent fra forskningsprogrammet CLIMIT, resten fra partnerne, som egenfinansiering.
CO2 som fanges i testanleggene slippes foreløpig ut igjen. Dersom Norcem en dag skal fange CO2 i stor skala, må det først etableres en infrastruktur for transport og lagring av CO2.
– Lykkes vi her, har vi en prototype som vil være interessant både for kraftverk og industri, legger hun til.
Norcems sementfabrikk i Brevik og Yaras ammoniakkfabrikk i Porsgrunn er de mest aktuelle kandidatene for et fullskala CO2-håndteringsprosjekt i Norge, konkluderer statsforetaket Gassnova i en idéstudie som ble oversendt Olje- og energidepartementet denne uka.
Sementfabrikken er det fjerde største punktutslippet i Norge, og slipper årlig ut nesten 800.000 tonn CO2. Yara i Porsgrunn er på femteplass, med vel 560.000 tonn. Søppelforbrenningsanlegget på Klemetsrud i Oslo kan også vurderes for CO2-fangst, mener Gassnova.
Verken Mongstad, Kårstø eller LNG-fabrikken i Hammerfest er aktuelle for CO2-fangst i denne omgang, ifølge Olje- og energidepartementets oppsummering av Gassnovas anbefalinger. Selve idéstudien er unndratt offentlighet.
Regjeringen vil gå gjennom anbefalingene og orientere Stortinget i statsbudsjettet for 2016, sier OED i en pressemelding. Departementet konstaterer også at det vil være «svært krevende» å realisere et fullskala demonstrasjonsanlegg innen 2020.
- Les også: Leire kan brukes i karbonfangst
Først i verden?
Dersom regjeringen følger opp anbefalingene fra Gassnova, kan det første fullskala anlegget for CO2-fangst i Norge dermed havne hos Norcem i Brevik. Ikke bare det: Den kan trolig bli verdens første sementfabrikk med CO2-rensing. På internasjonale oversikter over planlagte CCS-prosjekter finnes det ingen andre sementfabrikker.
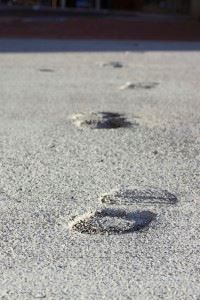
Sementindustriens karbonfotavtrykk er stort. Foto: Thinkstock
Klikk for å åpne
Sementindustrien er en av verdens største kilder til utslipp av CO2, og står for rundt 5 prosent av de globale utslippene. To tredeler er prosessutslipp, det vil si CO2 som frigjøres når kalkstein brennes til sement. Disse utslippene kan bare kuttes med en eller annen form for rensing. Testkjøringene i Brevik følges derfor med stor interesse i internasjonal sementindustri. Storkonsernet HeidelbergCement og bransjeorganisasjonen ECRA (European Cement Research Academy) er partnere i prosjektet.
Aminteknologi mest moden
Aker Solutions’ aminteknologi er den klart mest modne og velprøvde teknologien av de fire som testes. Dersom et fullskala anlegg skal stå ferdig allerede i 2020, er aminteknologien trolig den eneste som er aktuell, opplyste Norcems prosjektleder Liv Bjerge i et nyhetsbrev fra forskningsprogrammet Climit tidligere i år.
– Men i et lengre perspektiv har vi helt sikkert flere teknologier. Vi er veldig spent på membranteknologien, la hun til.
For membranteknologien har sine klare fordeler. Røykgassen kan renses uten bruk av aminer eller andre kjemikalier. Den tar også mindre plass enn absorbsjonstårn, som brukes ved aminteknologi.
Norsk patent
Teknologien er utviklet og patentert av May-Britt Hägg og hennes kolleger ved NTNU. Den består, grovt sagt, av en supertynn hinne, en polyvinylamin, som legges på en porøs bærestruktur, slik at vi får en komposittmembran. Metoden for separasjon kalles fasilitert transport. Ved hjelp av amingruppene i selve polymerstrukturen i membranen omdannes CO2 til bikarbonat ved hjelp av vanndampen som også finnes i røykgassen, og transporteres raskt gjennom membranen, mens de andre stoffene i røykgassen holdes tilbake.
– Vi bruker altså en «agent», en fiksert bærer i membranen, som hjelper til å med å omdanne den gassen vi vil fjerne. Forenklet sagt er det samme prosess som skjer i lungene våre når vi puster, sier Hägg. Der er det et enzym som omdanner CO2 til bikarbonat ved transport gjennom lungene.
Membranen er tidligere testet blant annet ved et kullkraftverk i Portugal, med gode resultater. Men temperaturen på røykgassen fra sementproduksjonen kan være høyere enn i et kullkraftverk, og mer variabel.
– Under den første testfasen i Brevik slet vi mye med riggen. Mye tid gikk med til ombygging, og vi fikk ikke kjørt kontinuerlig over tid. Men når temperaturkontrollen fungerte som den skulle, fikk vi gode målinger. Membranen tålte røykgassen, og separerte som den skulle, sier Hägg.
- Les også: Uten karbonfangst ryker klimamålet
Kristiansand-bedrift
Teknologien er nå i en søknadsrunde om å delta i testfase 2 i Brevik. Membrankonsortiet for fase 2 vil bestå av NTNU, SINTEF, DNV GL og det internasjonale membranselskapet Air Products, som har en norsk avdeling i Kristiansand. Bedriften der produserer nitrogenutskillere, avanserte hulfibermembraner som separerer ut nitrogen fra luften, som blant annet og brukers den for å beskytte eksplosjonsutsatte installasjoner til sjøs.
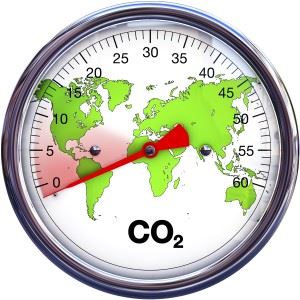
CO2-utslippene fra sementindustrien kan bare kuttes med en eller annen form for rensing. Illustrasjon: Thinkstock
Klikk for å åpne
– Det betyr at vi får med en profesjonell membranprodusent, og et tyngre innslag av norsk industri. Deres hulfibermembran belegges med vår membran, slik at den skiller ut CO2 i stedet for nitrogen, sier Hägg.
Hulfibermembranene gir stor overflate i forhold til volum, og trenger mindre plass enn absorbsjonstårn. De er bygd opp med moduler, og er dermed lettere å tilpasse behovet.
Nå er det to hulfibermoduler som eventuelt skal testes på en sidestrøm i Brevik. Testkjøringen skal vare ut 2016. Så skal det oppsummeres og rapporteres, før Norcem bestemmer seg for hvilken teknologi de eventuelt skal satse på.
– Dersom anlegget skal stå ferdig til 2020, er nok aminteknologien den eneste som er moden nok. Men vi kan også se for oss kombinasjoner og teknologi mer tilpasset enkeltutslipp, sier Hägg.
Testrigg på Tiller
NTNU og SINTEF er også i ferd med å bygge en membranrigg som etter planen skal utplasseres i SINTEFs testanlegg på Tiller i Trondheim til høsten.
– Her har vi den fordelen at vi, i kontrollerte former, kan kjøre forskjellige testserier basert på ulike sammensetninger av gasser og gjennom det simulere forskjellige typer utslippskilder. Dermed har vi muligheten til å få to fine rigger der vi kan få anledning til å demonstrere teknologien på alternative utslippskilder, og kontinuerlig optimalisere membranen. Vi tester videre inntil vi kan si at resultatene er dokumenterte. Og på et tidspunkt håper vi en industriell aktør er interessert i å kjøpe eller lisensiere teknologien, sier Hägg optimistisk.