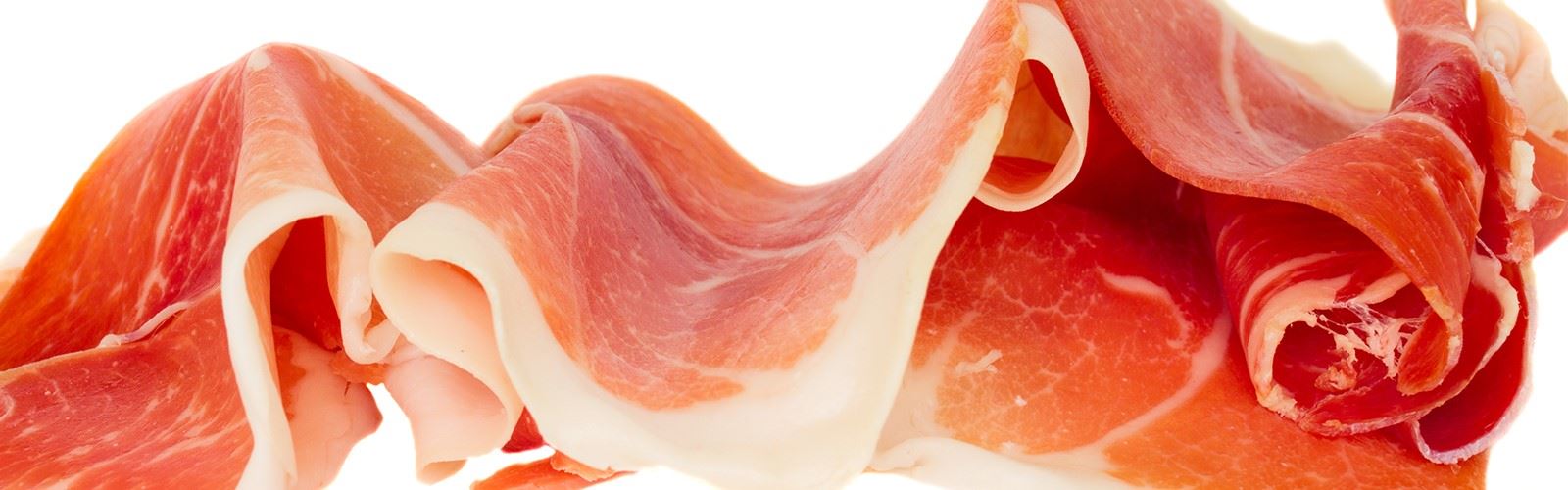
DryMeat
Project overview
The project was a Competence Building Project for Industry, funded by the Norwegian Research Council, Nortura SA, Alfsen og Gunderson AS and BWL Maskin AS. SINTEF Energi was leading the project and the involved research partners were SINTEF Materials and Chemistry, Nofima, Animalia and Instituto de Agroquímica y Tecnología de Alimentos (CSIC), Spain.
Drying and ripening conditions of high end, dry-cured ham require long processing times in order to achieve the superior quality. The weight of the product is reduced simultaneously, which makes the production an expensive process. The climatic conditions must be well controlled during processing and the focus is naturally on the superior product quality, while energy efficiency of the process is still an important but secondary parameter.
The main objective of DryMeat was to establish fundamental knowledge about interactions between drying kinetics and ripening processes for cured meat in order to design cost and energy efficient drying processes resulting in a desired and reproducible product quality. In order to achieve this specific sub-objectives were identified and addressed during the project execution.
The underlying background for DryMeat project was to support the Norwegian industry with new knowledge and understanding of the complex interaction (between process optimisation, product quality and energy efficiency and economics) or "of the above mentioned goals". In addition to the energy efficiency goal of 20 % reduction in energy consumption by 2020 is the authorities' aim of reducing the daily salt intake by 30 % in 2018. The objectives of DryMeat were identified under consideration of this background.
The project has reached its main objective by:
- generating fundamental knowledge on drying kinetics, salting and ripening reactions
- identifying more cost and energy efficient production process
- developing novel analytical methods based on LC-MS, including untargeted metabolite profiling and proteomics
- making suggestions for marker components with respect to product quality
- educating on PhD student
- developing several Spin-Off such as H2020 DryF where international collaboration were established
- 14 articles were published during the execution the project