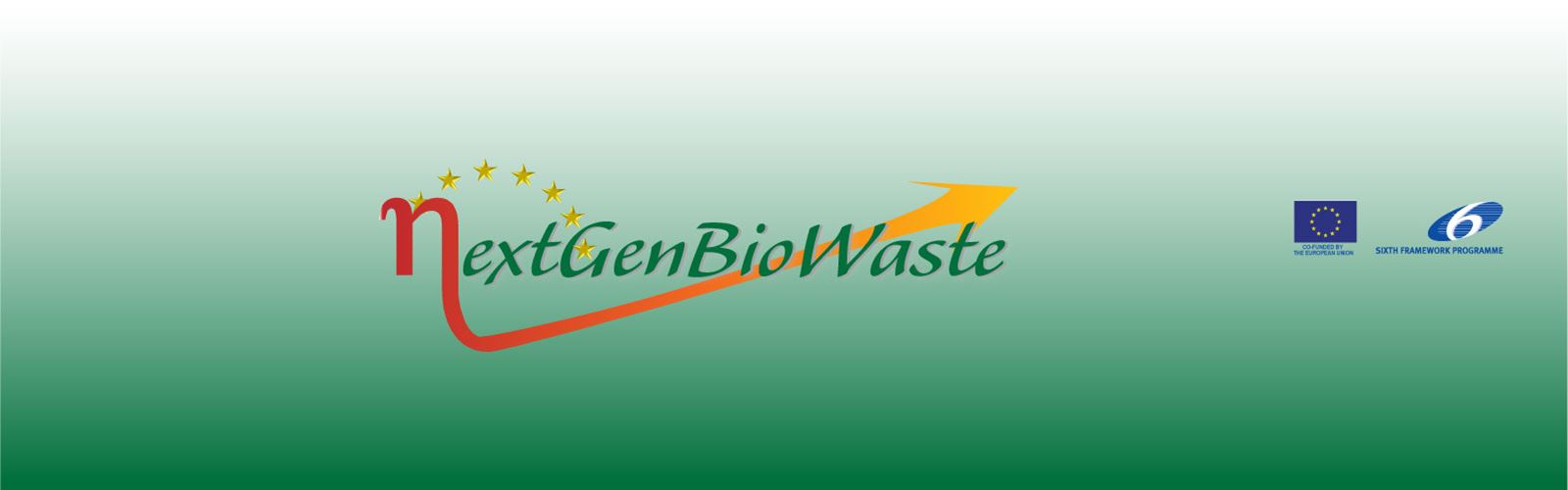
NextGenBioWaste
Conversion technology - SP2
The operational parameters in turn depend on the quality and composition of the input fuel and thus the combustion process. Further the control system used for the process must be reliable. For the case where the plant operator has reliable and real time information on the behaviour of the process, the process parameters can be adjusted and optimized as required during the process. When the effects of the key operational parameters on the plant performance are well understood via direct measurements and modelling, it is possible to further develop new concepts in combustion, boiler design and process control.
Objectives
In this project novel designs of reconstructions of existing boilers will be demonstrated; in addition novel concepts to boiler systems of completely new generation High Efficiency Waste-to-Energy plants. All these demonstrations are aimed at getting a much better energy recovery (efficiency improvement, CO2 emission reduction), increase of throughput, increase of reliability and cost efficiency.
The present task addresses this issue and seeks to develop methods, which will provide information required for this process optimization. The information not only includes real time data on the behaviour of the combustion but also on the degradation behaviour of plant components. Collectively this information can be used to adjust the process parameters, and better plan outages due to a better understanding of the degradation mechanisms.
State of the art
Only 3% of the entire European energy demand is currently covered by energy from waste. Knowing the vast amounts of waste available in Europe, it seems obvious that waste to energy may contribute significantly to the overall RES target provided there is a market for heat and cold. In the context of NextGenBioWaste, heat can be converted into cold by the use of an absorption chiller. As can be concluded from the figure below, about 80% of the energy from waste is converted into heat, and about 20% into electricity. Eventually, by introducing schemes for trigeneration of electricity, heat and cold from waste and biomass with a high electric efficiency, the operations would become less dependent on the seasonal demand for heat and cold. This suggests that a substantial shift towards waste-to-energy may take place in a greater area of Europe that would directly respond to the RES-e target aimed at deriving 22.1% of all electricity within the EU from renewable sources by 2010 as compared with 13.9% in 1997. Trigeneration (electricity, heat and cool) is always very advantageous for conversion of feedstocks at maximum energy efficiencies. Trigeneration is strongly dependant on the demand side of the market. Therefore finding the suitable location for trigeneration is vitally important. Cool is a derivative of electricity or heat. Therefore, trigeneration as such is not planned for the demonstration activities within NextGenBioWaste.
![]() |
Figure 1: Energy production by municipal waste incinerators in Europe (1999), source BREF Waste Incineration (March 2004, 2nd draft) * means incomplete data [ISWA,2002] |
The current state-of-the-art characteristics of waste conversion technologies:
- Low electrical efficiency, 18-22%
- Severe fouling and corrosion behaviour due to the nature of the fuel and the complex combustion process
- High maintenance costs because of corrosion
- Practical experienced-based control systems
- Grate fired systems is the dominating technology. Some plants, using fluidised bed technology, have been built but severe operational problems are reported.
- High excess air ratio. Typical oxygen concentration is 8vol% O2 , giving relatively large plants and volumes of flue gas to be treated
- High capital costs
- Poor utilisation of residues
In many waste-to-energy plants the lifetime of the final superheaters is as low as 2 years, because of corrosion problems. A set of superheaters for a 40 MW grate-fired boiler with steam data of 400-420 OC is about 0.5 MEuro. There are also extra costs due to unplanned outages in the year before replacement because of a large number of tube leakages (usually 10-15) leading to unplanned stops. This is estimated to cost 250-500 kEuro per year for 10 outages, calculated on loss of income from not being able to receive waste and not being able to sell electricity and heat. (Plants in Germany are paid 100 Euros for every tonne of waste they burn. An average boiler can burn 500 tonnes per day). Doubling the lifetime of superheaters, either by using additives to reduce corrosion or by use of a more corrosion resistant and cost effective material will therefore lead to savings in both maintenance costs and operation costs, estimated as 0.25 MEuro per boiler and year. Furnace wall corrosion and low temperature corrosion are also problems but these costs have not been estimated.
The cost of a superheater includes material costs and manufacturing and installation costs. Using a material that costs twice as much does not therefore lead to a doubling in costs of the whole superheater, typically it might increase by 50%. Therefore more advanced materials are often cost effective.
In Germany alone there are 50 waste-fired grate boilers producing superheated steam. If superheater lifetimes could be doubled in all of them the savings would be considerable.
The current state of the art characteristics of biomass conversion technologies:
- Electrical efficiency ~33%
- Grate fired or fluidised bed systems are being used
- High fuel costs leads to a drive for cheaper and potentially more problematic fuels
- Control systems are based on practical experience
- A maximum co-combustion share of 50% of waste wood in biomass plants is possible
Activities
- The development of process control methods based on dynamic combustion models will be conducted.
- The study of the mechanisms of solid fuel ignition on a WtE plant grate will be conducted in a lab scale facility.
- The development of the in-situ HCl capture system will be carried out on lab-scale and by modelling.
- The development of corrosion laboratory testing to simulate the combustion environment
- Slagging and fouling Models based upon equilibrium calculations. Using such a method the volatile and condensation behaviour of the combustion gases can be described.
- Dynamic CFD model development
- Process flow sheet modelling is carried
- The development and testing of sensors will be carried out for different types of sensors. Development of
- of a sensor for the measurement of NaCl and KCl.
- an electrochemical based corrosion probe.
- corrosion probes which can be implemented in critical parts of the boiler
- a sensor which will permit measurements of the temperature and gaseous species in the combustion layer.
- of a method of determining the wall thickness of boiler components using ultra sound.
- Demonstration activities in existing plants.