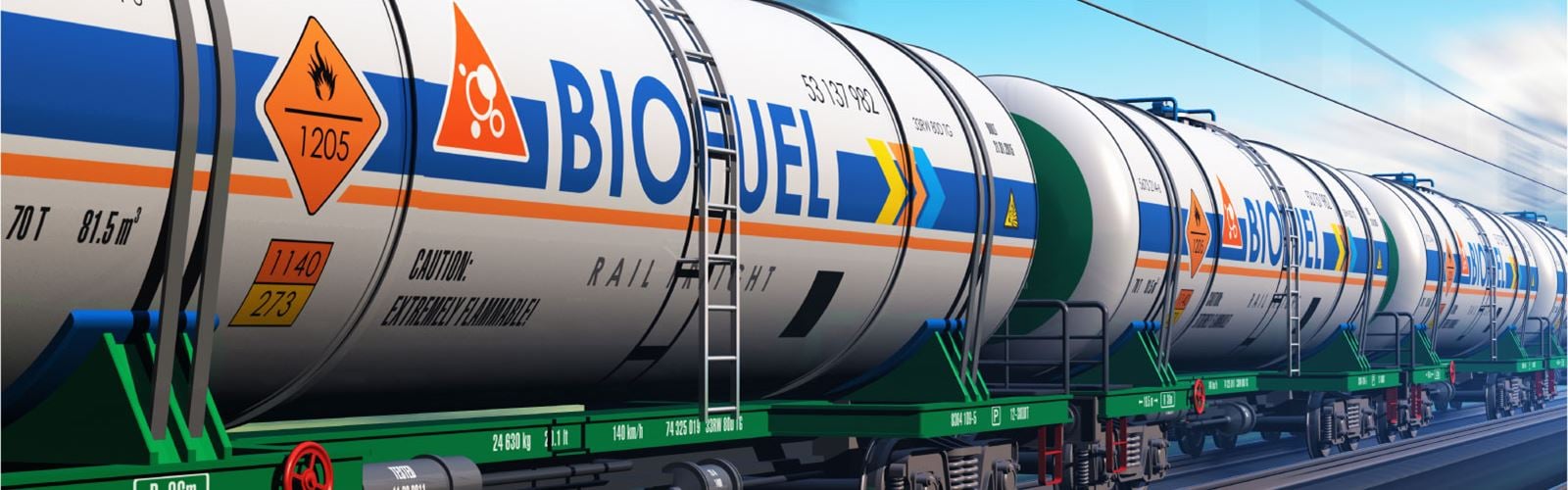
GAFT - Gasification and FT-Synthesis of Lignocellulosic Feedstocks
Gasification
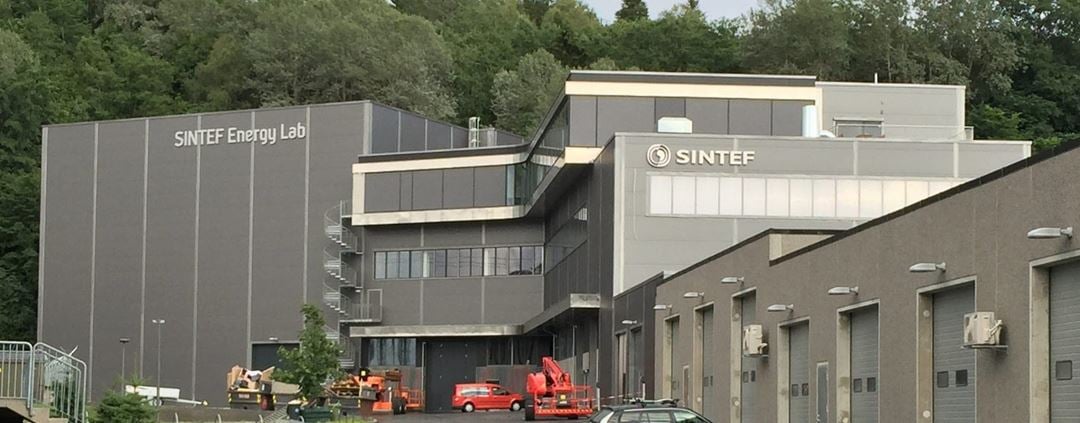
Gasification is a thermochemical process were carbonaceous fuels are converted into combustible gases often referred to as syngas. There are different types of reactors like fixed-bed, fluidised-bed (FB), and entrained flow (EF). Two types of EF gasifiers can be distinguished; slagging and non-slagging. In a non-slagging type the reactor interior walls are kept more or less free from ash; a mode best suited for feedstocks with low ash content. However, in the case of biomass, it is preferred to have a slagging reactor because fouling cannot be totally avoided and more importantly; because a slagging reactor is more fuel flexible. As long as the fuel ash can be kept in a molten state in the reactor, fouling and plugging can be prevented which opens up opportunities to use low grade fuels. In addition, the increased flexibility of a slagging reactor makes the adaptation to future changes in feedstock cost (and availability) easier without changing gasification technology. EF gasifier of the slagging type is currently under commissioning at our newly erected laboratory at Blaklia, SINTEF Energy Lab.
- Development of Computational fluid dynamics
(CFD) and kinetic models for the prediction of the performance of the EF reactor with low-grade biomass and for char reactivity will be investigated through a PhD work that will start in 2016. - Ash behaviour:
The selected gasification technology requires that at least 5-6 wt. % of the biomass feed should be ash, an amount that is necessary for the continuous flow of molten ash and the complete cover/protection of the reactor wall. In order to be able to use these feedstocks in an EF reactor the ash composition needs to be optimised. This can be achieved either by feedstock mixing and/or by using additives. - Particle feeding:
One of the advantages of EF reactors is a high conversion rate compared to other gasification technologies. This is obtained by using high temperature and small particles (typically 100 µm for coal). The energy requirements for grinding biomass to the same particle size as coal have been found to require ca. 20 % of the energy content of the feedstock. Torrefaction can be applied in order to improve grindability and avoid fibrous particles that can cause feeding problems even at small sizes. - Syngas optimisation:
In downstream Fisher Tropsch (FT) processes, the syngas needs to have a H2 to CO ratio of 2 for optimal operation. In addition, the syngas needs to be clean of contaminates such as sulphur components, larger hydrocarbons and sub-micron particles. The gas can be cleaned by processes downstream the gasifier but before the fuel synthesis. However, if the gas composition and concentration of contaminates can be optimized and minimized before gas cleaning and conditioning this may facilitate potential capital and operational cost reductions. Several parameters such as gasification temperature, reactor residence time, fuel particle size and gasification agent influence the gas composition and the amount of contaminates and this will be investigated in the GAFT project and quantified through; cold gas efficiency, carbon conversion efficiency and product gas distribution.