Battery technology is essential to meet Europe and Norway’s zero emission targets by 2050, helping to reduce carbon emissions in the energy and transport sectors across the continent. In Norway, strong battery research communities have flourished for over a decade, attracting growing interest from the industry.
The value chain perspective is important when discussing batteries in Norway. SINTEF is now publishing a report addressing an overview of Norwegian battery research and industry. The report was launched during the project SUMBAT consortium meeting, held on March 12, 2024.
A need for suppliers of all components
The battery technology needs to advance, but equally important is to enhance sustainability in production, utilization, and recycling by establishing value chains wherein everything, from the selection of materials for the batteries to their recycling process, operates with the most efficient logistics at each stage.
Currently, there are several initiatives for battery manufacturing in Norway and a few companies are in the initial stages of establishing factories for commercial production.
FREYR aims to provide industrial scale clean battery solutions and is finalizing a customer qualification plant for lithium-ion batteries (LIBs) produced with their technology in Norway.
– What we see is lacking for establishing a comprehensive value chain in Norway are suppliers of all necessary components in the required volumes, says Kush Upadhyay, R&D Engineer from FREYR.
Market growth for electric vehicles
Thanks to access to affordable renewable energy and government incentives, Norway has been a pioneering country for the electrification of transport. Currently, Norway has more electric vehicles per person than any other country in the world. Most of the electric vehicles are owned by private individuals, but more companies are also joining the shift towards green transportation and benefiting from the growing battery market.
Within application of batteries for transportation, the majority of the research in Norway has been related to the maritime industry. This has given Norway a world leading position in this field.
Corvus Energy is one of the pioneers in energy storage and delivers zero-emission solutions for all segments in the maritime transportation. They can confirm the increased demand.
– We see significant market growth and increasing demand for maritime battery solutions. Further, we see big and growing advantages arising from data driven battery condition assessments, partly developed within the SUMBAT project, says Lars Ole Valøen, EVP & CTO from Corvus.
SUMBAT is a Green Platform project funded by the Research Council of Norway and aims to assemble the world's most sustainable value chain for battery production.
Become more self-sufficient of critical raw materials
Norway plays an important role to secure European independency as the nation holds substantial amounts of key minerals necessary for sustaining local production. Important critical raw materials (CRMs) used in making the active components of LIBs include cobalt, lithium, nickel, graphite, copper, silicon, and manganese.
These materials are limited resources and some of them are not well distributed in the world. The European Commission (EC) estimated that to achieve its goal of climate neutrality, the EU would require up to 60 times more lithium and 15 times more cobalt.
The EC has identified securing and diversifying the supply of critical raw materials as one of the top ten strategic issues to ensure EU’s freedom and operational capacity in the future. The dependency of China in particular, can be exemplified by graphite, one of the main components of lithium-ion batteries. In 2018, China produced about 68 percent of the world’s graphite and more than 90 percent of the graphite for batteries.
The Norwegian company Vianode is developing and producing graphite for LIBs. Their graphite products have 90 percent lower CO2 emissions than current commercially available materials. They aim to produce battery materials for 3 million electric vehicles per year by 2030. The company has been running a pilot plant in Kristiansand since spring 2021 and is now starting industrial production at the Herøya Industrial Park.
– We are ready to get started, however, we strongly advocate for more stringent regulations from the authorities to foster a more sustainable battery value chain, says Gunstein Skomedal, Head of Research at Vianode.
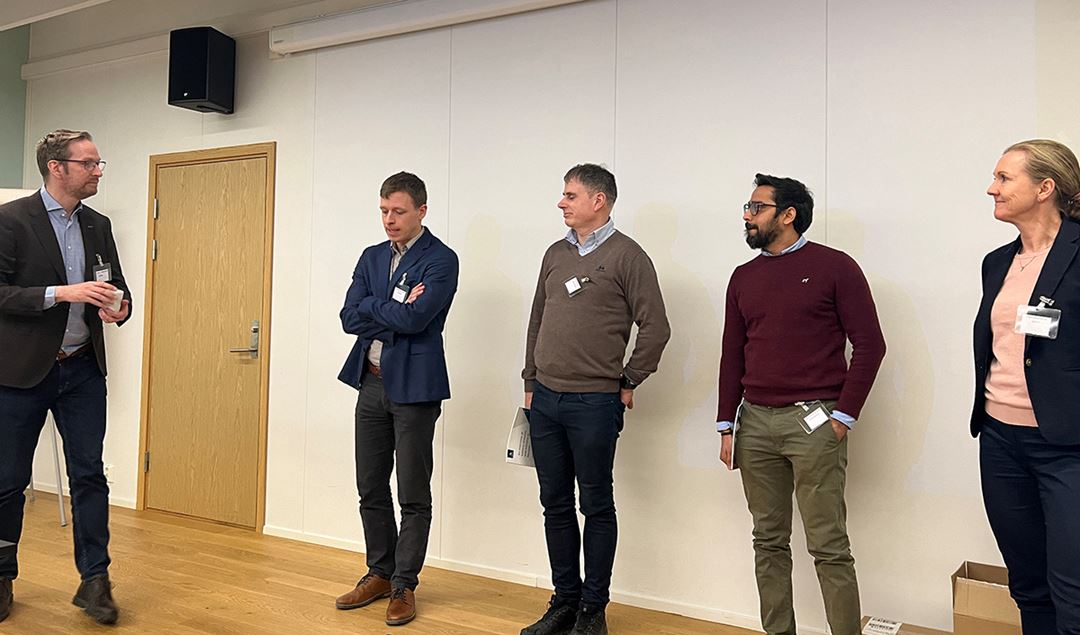
Recycling of materials
In order to ensure sustainable battery production, the value chain has to move from linear to a circular system by improving re-use, recycling, and integration to secondary raw materials. High degree of circularity will have positive effects on the economy, reduce the overall environmental footprint and prevent shortage of CRMs.
Norway, with its strong expertise in processing industry, has a great opportunity to take a leading role within recycling of batteries and developing new and more efficient processes for recycling of all battery materials.
– Today, graphite is not recycled, and ends up as CO2-emissions. However, we at Vianode have developed a unique technology that is also capable of recycling graphite from battery production scrap and end of life batteries back into graphite that can be used in creation of new lithium-ion batteries. This is a true gamechanger and will make batteries even more sustainable in the future, says Gunstein Skomedal.
Research and Innovation as a cornerstone
Research and innovation are essential to ensure that European battery production and usage are both competitive and sustainable. SINTEF has for the last decade focused on shaping and contributing to the European research and innovation agenda for batteries.
SINTEF has an extensive research infrastructure and many ongoing research projects on batteries. At SINTEF Battery lab we are expanding our research activities on materials for different battery technologies. The lates addition to SINTEF’s battery infrastructure is part of NABLA, aimed at providing a national infrastructure dedicated to the battery research and development for Norwegian research and industrial organizations.
Fride Vullum-Bruer, Senior Research Scientist at SINTEF Energy, conducts research on various aspects of the battery value chain. She also points at recycling and access to CRMs as important parts.
– Although we’ve made good progress compared to many other countries, we need to focus more on research along the entire value chain. Topics where Norway has much of the competence required to excel, are raw materials sourcing and production as well as recycling. And both areas could be vital for successful battery production in Norway and Europe.
To become more competitive in the European energy market, it’s crucial to meet European regulations. The ongoing development of the EU’s battery passport, which will include all information about the battery from cradle to grave, including carbon footprint, will be important.
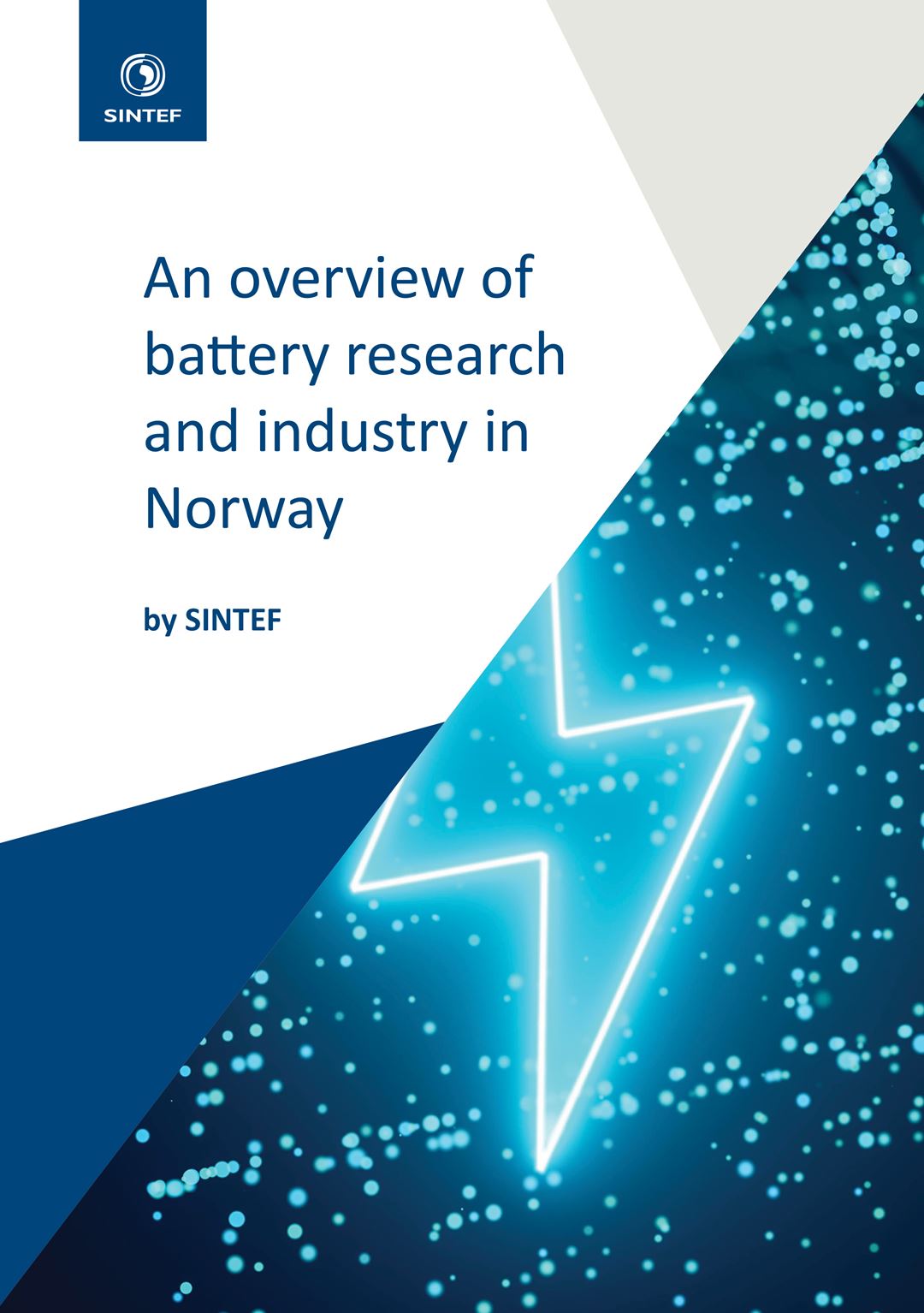
Read the report here:
An overview of battery research and industry in Norway (pdf)