Hydrogen peroxide (H2O2) is used as a whitener or disinfection chemical in many industries, such as pulp and paper, textiles, electronics, resins, coatings, disinfection, and water treatment. The chemical is traditionally produced in centralised energy intensive production and subsequently provided and used in these sectors.
With the EU Sustainable Development Goals and Green Deal as a backdrop, a new EU-funded project will make the chemical industry greener and reduce greenhouse gas emissions.
Substantial economic and environmental benefits
The project will develop an electrified technology for the production of H2O2 in textile and pulp and paper production. The expected results will revolutionize the production of H2O2 – from traditional manufacturing with a significant CO2 footprint, to a adaptable, robust on-site production, based on the need for H2O2.
– This will both reduce CO2 emissions directly and indirectly, in addition to contributing to a circular economy by reducing the consumption of critical raw materials and the amount of hazardous waste, says Richard H. Heyn, Project Coordinator and Chief Scientist at SINTEF.
Uses a digital twin to replace fossil fuel-based production with renewable energy sources
The research focus of the project is to develop a unique electrochemical process for the production of H2O2 via persulfate, a compound that has higher oxidation potential and is more stable than H2O2.
The flexible and scalable process will use only water and renewable sources of electricity to replace the current production process that relies solely on fossil fuels. This will provide improved energy and material efficiency and result in savings in greenhouse gas emissions.
To achieve the research goal, the project will develop a digital twin, to simulate the dynamic operation with variations in the availability of renewable power. They will also analyse how the full-sized system would be able to function as a grid balancing service, utilizing renewable electricity when it is both abundant and cheap.
– Data from the digital twin will be part of the identification of routes for improved commercial viability, ensuring efficient integration of renewable sources to drive the conversion process in a reliable manner, explains Richard H. Heyn.
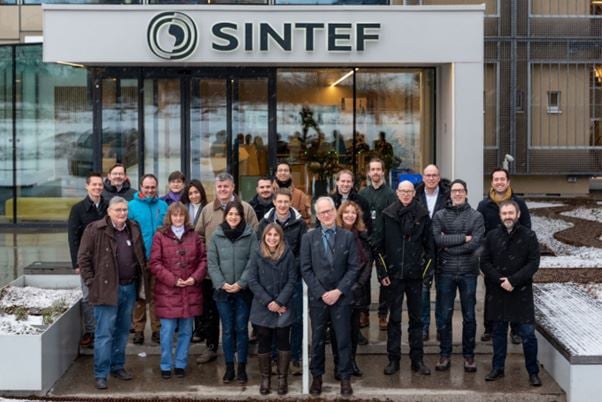