Drilling operations
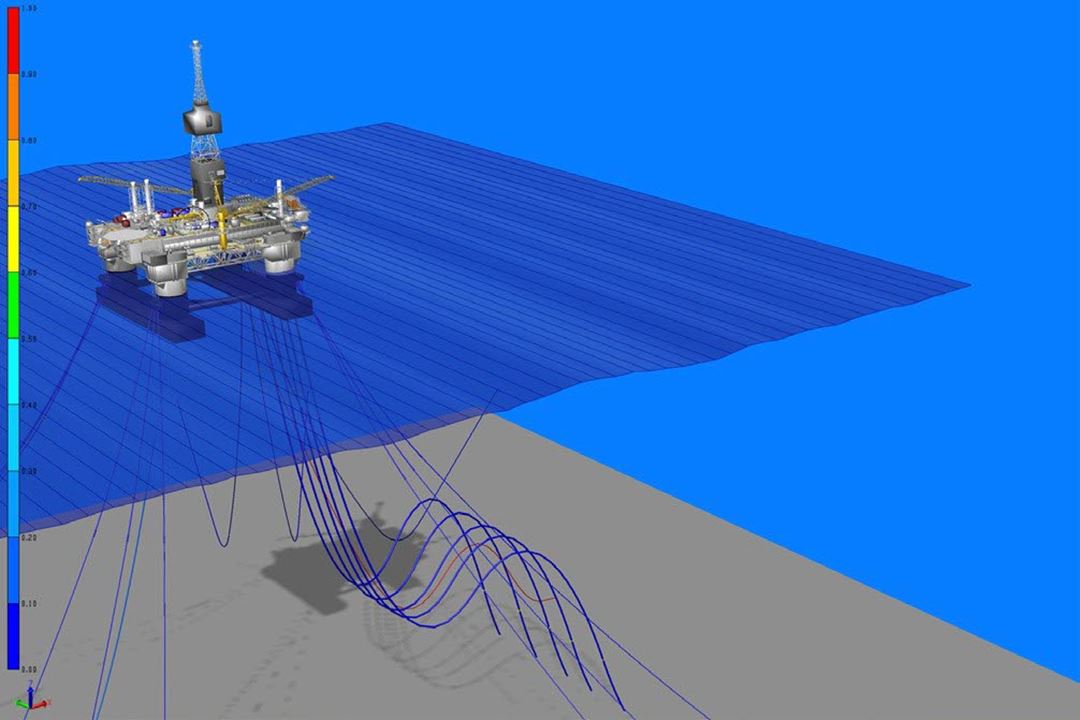
The SIMA workbench includes modelling capabilities that allows building a complete and accurate physical representation of a floater and drillstring, either using an RAO (response amplitude operator), or a coupled force model. SimDrill is a high-level modelling and anlysis tool for drilling operations built on top of the SIMA workbench.
Modelling capabilities
Standard components for offshore drilling operations from floaters are available including:
- Wells and geotechnical models according API RP2GEO or ISO/TR 13624-2
- Vessel model based on RAO or coupled force model
- Riser joints, slick or buoyancy type
- BOP
- Xmas tree
- Tensioner system
- Flex-joints
- 2D and 3D modelling view
Through an intuitive interface the components are assembled into a drilling system (riser tally) by selecting form the components defined by the user.
Analysis modules
SimDrill includes several analysis modules that range from basic model setup to complete analysis workflows:
- Complete workflow for global analysis of Wellhead Fatigue based on DNVGL-RP-0142, including automated reporting.
- Basic analysis setup and reporting for VIV (using VIVANA), operating limits, recoil analysis and riser fatigue.
- Models can be exported and further refined in the SIMA workbench.
Wellhead fatigue analysis in SimDrill
SimDrill performs wellhead fatigue analysis based on the DNV wellhead fatigue method described in DNVGL-RP-0142. The recommended practice is based on a combination of local and global finite element analysis. The local analysis generates transfer functions that give the relation between moment at wellhead and stress in an arbitrary number of hotspots in the wellhead/conductor. The local analysis must be performed in a separate general FE tool. SimDrill is capable of importing transfer functions and use them for global analysis FE results.
The method described by DNV is complex and in some cases open for interpretation. The following assumptions have been made in the current version of SimDrill:
- Uni-directional global analysis is used, spreading may be applied
- Fatigue damage is calculated using interpolated stress time-series, M-N approach is not used.
Hotspot stress transfer curves are imported from a defined xml-format, parameter variation may be done using the following variables if transfer functions are available:
- Operation phase
- Vessel id
- Hotspot id
- Cement level
- Soil stiffness bound
- Template stiffness bound
Historical weather data may be represented by time-series of actual observations or scatter diagrams.
An arbitrary number of historical and planned operations may be applied. Each operation is associated with a phase, assigned type (Historical/Planned), and linked to a Drilling system.
A start and end time must be entered for each operation. For historical operations, the operation must be within the imported hindcast data. Scatter diagrams are generated for each operation.
The result is a fatigue damage for each combination of operation, hotspot and cement-level. The accumulated damage over operations is calculated for each combination of hotspot and cement level. The combination of hotspot and cement-level giving the highest accumulated damage is reported.