In order to truly exploit the opportunities offered by additive manufacturing, in terms of geometric complexity and taylored mass-production, virtual product development is important. Numerical simulations is a central element in this. We can distinguish between two main types of numerical simulations for AM:
1) Simulation of the physical AM process, typically aiming at reducing process-induced thermal stresses, and resulting part distortion and crack initiation.
2) Geometry optimization of a component to be made by AM (but initially without thinking about the AM process as such), also referred to as "analysis-based design" or "generative design". This could be to minimize the component weight for given mechanical loads and boundary conditions, to take advantage of the geometric freedom of AM. This is often referred to as topology and shape optimization. Such simulations can also address properties other than weight and mechanical performance. One example could be a reactor system, in which multiphysics simulations of flow/mixing, chemical reactions and heat transfer are performed in order to optimize the geometry of the components, especially internal structures.
Ideally, both types of simulations should be coupled or run iteratively, in order to achieve an optimal component. For simulations of "type 1" above, SINTEF uses and evaluates some of the commercial programs that exist, but SINTEF also uses its expertise in welding simulations etc to develop simulation models for selected AM processes and materials. SINTEF is also active with regard to "type 2" simulations, e.g. regarding how anisotropic mechanical properties can be included in a topology optimization.
When it comes to reducing thermal stresses etc, today's simulation programs have their limitations, but material models and material data are constantly improving. As of today, practical experience and design rules may be the best starting point.
To minimize problems with residual stresses etc (for a given material, note that some materials are more problematic than others), one must optimize the geometry of the component to be built, as well as its orientation, anchoring and support in the AM process (if we focus on powder bed fusion processes for metals, which is the most common metal additive process in the industry). Furthermore, process parameters and possible post-processing must be optimized.
With regard to new simulation technologies for AM, SINTEF is also performing research on isogeometric analysis where three-variable mathematical descriptions (splines) replace both traditional two-variable representation used in design software (CAD) and traditional elements used in finite element analysis (FEA).
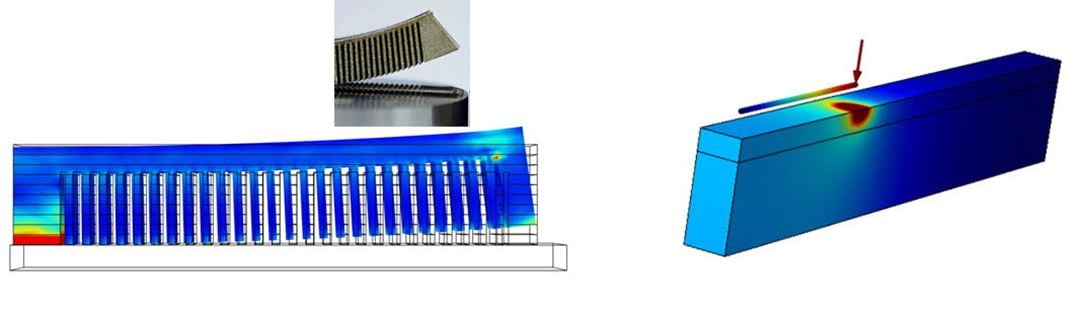
Contact persons:
- Mohammed M'Hamdi (numerical simulation of AM processes, and development of microstructure)
- Amin S. Azar (topology and shape optimization, material data for structural analysis (FEA))
- Vegard Brøtan (lattice structures, topology and shape optimization)
- Erik Andreassen (material models and data for structural analysis with polymer materials)
- Tor Dokken (isogeometric analysis (IgA), geometry representations)