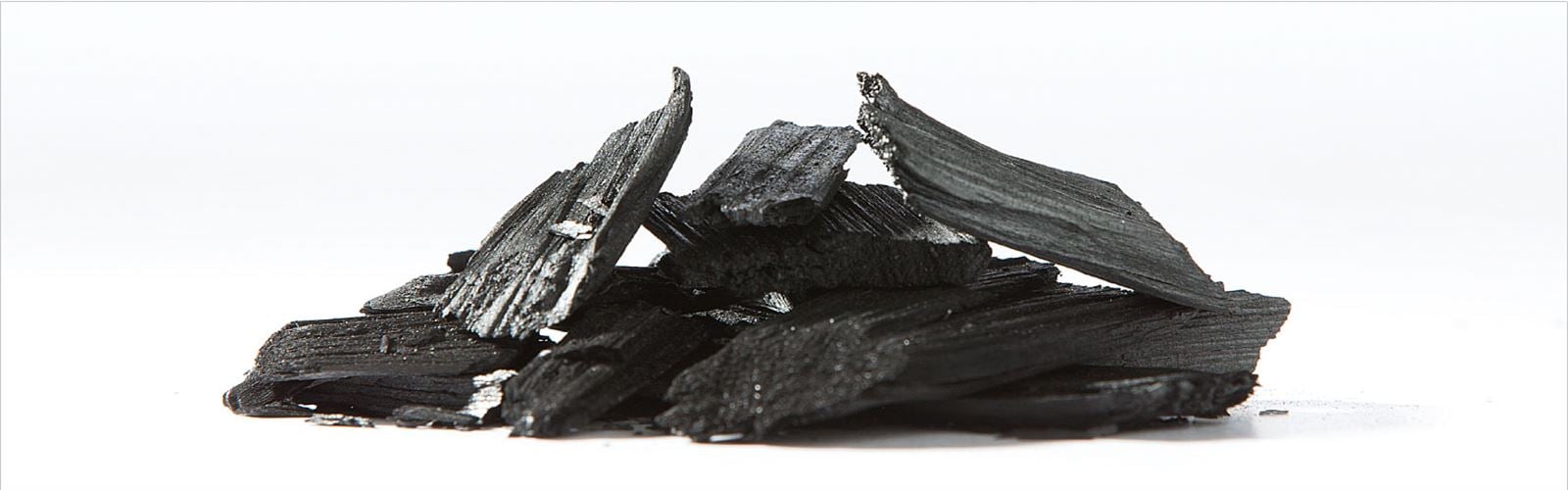
BioCarbUp - Optimising the biocarbon value chain for a sustainable metallurgical industry
Project overview
BioCarbUp responds to the national strategies and the goals of the metallurgical industry by analyzing and optimizing the biocarbon (BC) value chain to produce suitable and affordable reductants in a sustainable manner.
Producing BC, a renewable material from biomass resources, will have a twofold effect: (1) reduce CO2 emissions by substituting for fossil reductants and (2) increase forest resource utilisation by creating higher value material and/or energy products. Due to the BC quality demanded by the metallurgical processes, woody biomass, especially stem wood, is the most suitable candidate for reductant feedstock.
Although BC has some desirable reductant properties, substantial improvements are needed in other properties to completely reproduce the characteristics of fossil reductants. This especially relates to 1) increased strength and density and 2) reduced reactivity (for Mn-alloy and Al).
The BC reductant should not have significant negative influence on existing metallurgical processes, i.e. result in increased fixed carbon (fix-C) consumption, higher energy demand, or lower product quality. Hence, additional requirements for the BC include expectations for volatile matter and ash.
Maximising the BC yield and utilising by-products efficiently will ensure cost-effective and sustainable BC production. By optimizing carbonization, the fix-C yield can approach a theoretical yield defined by thermodynamic considerations. Fix-C is essential for the metallurgical industry as it is the key for the final removal of oxygen from the metal oxide ores, thereby producing pure metals or alloys.
In KPN BioCarb+, the predecessor to KPN BioCarbUp, the focus was partly on BC for energy production using forest residues as main biomass resource, and partly on BC production for metallurgical processes, using both forest residues and higher quality wood as resource. A main conclusion from BioCarb+ was that enabling the BC value chain for sustainable metallurgical industry in Norway would require the use of higher quality wood and that the BC quality and the overall BC value chain must be optimized. BioCarbUp builds on BioCarb+, advancing the knowledge further while focusing on BC for use in the metallurgical industry.
In BC production the by-products are normally burned for producing process heat and/or electricity, for primarily internal but also for external use. However, tar collection for further utilization and possible upgrading to higher value products or biofuels is an option. Another by-product in the BC value chain is charcoal fines, resulting from BC handling. This is a source for upgraded BC via compression or agglomeration, or can be used for energy production. In BioCarbUp we will look at these options.
The BC value chain for the metallurgical industry involves the resource side (forest operations), further handling, logistics and storage of the resource, BC production and by-products utilization or collection and upgrading, BC upgrading, BC logistics, and the end-use as reductant.
The whole BC value chain is included in BioCarbUp. The target is BC for sustainable metallurgical industry. Through sourcing of biomass resources to produce different BC qualities, several TWh/year increased biomass utilisation is possible within a moderate timeframe. For this to happen, research is needed across the span of the BC value chain.
The BioCarbUp project consortium covers all the necessary aspects, from resources to end-use, and includes large and central industrial players in the metallurgical and bioenergy areas in Norway: Norsk Biobrensel, Elkem, Eyde Cluster, Eramet Norway, Alcoa Norway and Norsk Hydro.