Extractive industries, including refractory raw material production, are responsible for a significant part of the world’s carbon emissions and has a strong impact on the loss of biodiversity. Establishing a circular economy and developing an efficient recycling process for this industry is essential to reduce CO2 emissions in Europe, as well as preserve natural resources.
– Refractory products for industries using high-temperature processes, such as cement-, glass- and steel industry, are precisely adapted to the needs of each individual customer. Since many different products are used in each application and get mixed after treatment, this is a challenge for the recycling, explains Alexander Leitner from RHI Magnesita, the company that coordinates the project Refractory Sorting Using Revolutionizing Classification Equipment project (ReSoURCE).
– Gaining the raw material for refractory products is in general CO2 intense, RHI Magnesita invests to improve the recycling process. With ReSoURCE we hope to be able to save up to 800.000 tons of CO2 emissions in Europe per year.
Creating a multi-sensor sorting unit
The biggest challenge in recycling refractory products is the precise sorting of the different used materials consisting of a mixture of different chemical components. Being able to split (segregate) the components and sort them into different quality groups is crucial for the quality of future products created from these recycled secondary raw materials.
ReSoURCE is in the process of developing a solution for this by creating a multi-sensor sorting unit. Different types of optical sensing technologies can be used to sort out components in refractory materials. The unit combines laser-induced breakdown spectroscopy (LIBS) and hyperspectral imaging allowing for an element and material classification.
The research institute SINTEF contributes with its know-how in powder technology and sorting solutions for powder materials to develop novel solutions for sorting fine-grained refractory waste materials.
– We are delighted to bring our more than 40 years of experience in developing lab, pilot, and industrials scale solutions in powder science and technology to this important research initiative, states Akhilesh Kumar Srivastava, project leader and senior research scientist at SINTEF Industry.
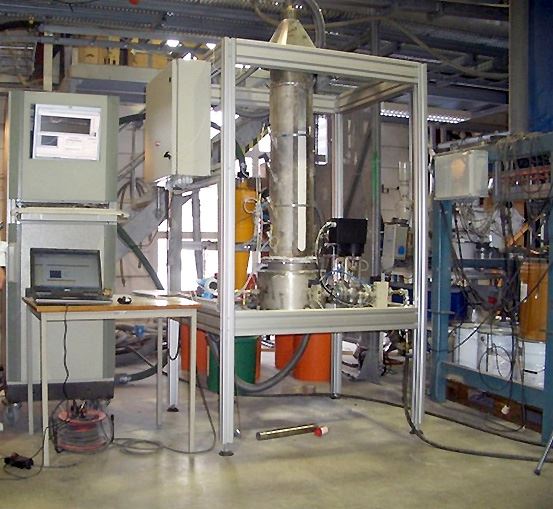
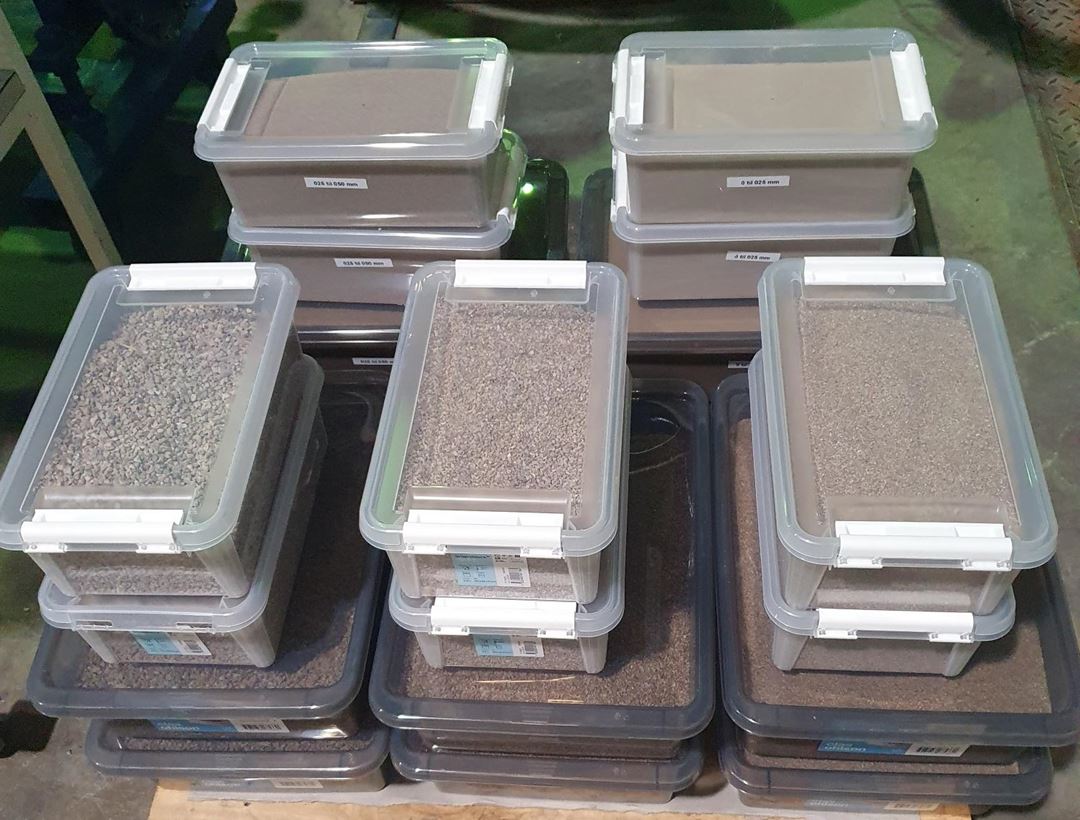
Sorting particles down to below 1 mm
The new unit should be able to manage the sorting of particle sizes down to 1–5-millimeter scale, also known as fine fractions.
– In refractory recycling, the fine fractions are mostly used as landfill. The challenge is to recover these fine fractions from the refractory waste through direct sorting methods, adds Chandana Ratnayake, chief scientist at SINTEF Industry.
Using cutting-edge technology to study recycled materials
The largest independent research and development organization in electro optics in Norway, Norsk Elektro Optikk (NEO), is contributing with its technology in hyperspectral imaging (HSI) to the project.
– Hyperspectral imaging is used across different industries to characterize surface compositions and quality changes of materials, says Friederike Koerting from NEO. She’s the geological hyperspectral expert at NEO.
– HSI enables us to optically inspect different materials using a wider spectral range than what the human eye allows. In this way we can detect changes between different minerals and mixtures based on their distinctive spectroscopic properties, allowing us to identify and highlight changes between recycling materials. HSI also has real-time material classification and machine vision capabilities aiding the sorting process.
– With our technology and the solutions developed by project partners, the used material on the conveyor belt will be analyzed and classified automatically. We have already seen in our first tests in the laboratory that the components we are working with can be distinguished with higher precision than that of the manual sampling, reports Koerting.
With the goal of a green and digital transformation of the refractory recycling value chain, the project ReSoURCE will innovate the entire recycling industry in the European refractory industry. When the project reaches its targets, it can contribute to massive annual CO2 reductions, up to 800 (kilo) tons per year, and energy savings of up to 760 GWh per year.