Green hydrogen is a promising alternative to fossil fuels, allowing decarbonization of crucial industry sectors. It can be converted to electricity for use in the transportation sector, as a feedstock for metal production or can be burned to produce heat for use when making cement.
However, one of the challenges in the production of green hydrogen is that materials needed in the process are expensive and hard to find. Many of them have been designated as Critical Raw Materials (CRMs) or have negative environmental impacts. In addition, large investment and electricity costs lead to a prohibitively expensive production cost.
A new project funded through the Clean Energy Transition Partnership will seek to solve this by developing and demonstrating new technology for efficient production of green hydrogen.
– The innovations will contribute directly to the increased use of green hydrogen technologies, help Europe reach its emission reduction targets and enhance European expertise in green hydrogen, says researcher at SINTEF, Patrick Fortin.
Changing the electrolysis process
Green hydrogen is produced using a technique called water electrolysis. In this process, renewable electricity is used to split water molecules into hydrogen and oxygen gas. There are two main types of electrolysis in use today: alkaline, and PEM (Proton Exchange Membrane). The alkaline technology has been operating in Norway for almost 100 years (Source: nelhydrogen.com), whilst the SINTEF spin-off company Hystar is an example of a Norwegian company that are set to produce PEM electrolysers.
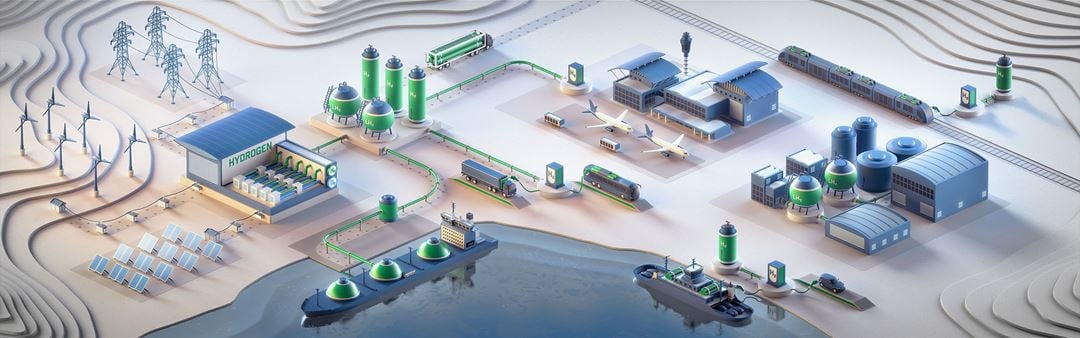
Currently "proton exchange membrane water electrolysis (PEMWE)” is the most promising route towards green hydrogen production. Compared to traditional alkaline electrolysis, PEM electrolysers have higher performance, and can respond to quick changes in power supply, making them ideal for coupling with renewable energy sources.
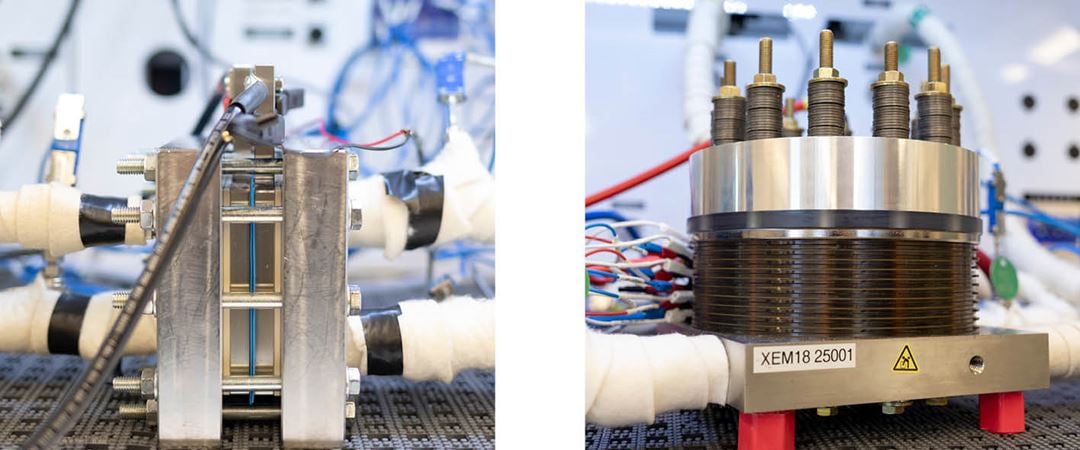
However, the major shortcoming of PEMWE is that it needs expensive and rare materials to overcome the harsh operating environment whilst producing high quality gasses in a safe way.
– Today’s commercial PEMWE systems all rely on materials lead to a high cost of the electrolyser and have been identified as critical raw materials, or materials with sustainability/environmental concerns. These materials are noble metal catalysts and protective coatings, titanium-based bipolar plates, and perfluorinated sulfonic acid (PFSA)-based membranes, tells Patrick Fortin.
In the project’s electrolyser stacks, the critical raw material titanium is replaced with stainless steel, and the iridium loading is decreased by 50 percent. In addition, replacing fluorinated membranes will improve the sustainability, providing more environmental friendly hydrogen production, at a significantly reduced cost.
– The main goal of the project is to develop and demonstrate a proton exchange membrane (PEM) electrolyser stack with increased performance, reduced costs and increased sustainability compared to current PEM electrolyser systems,” says Fortin.
The innovations will be tested initially on a lab-scale before upscaling with the help of the project’s industrial partners.
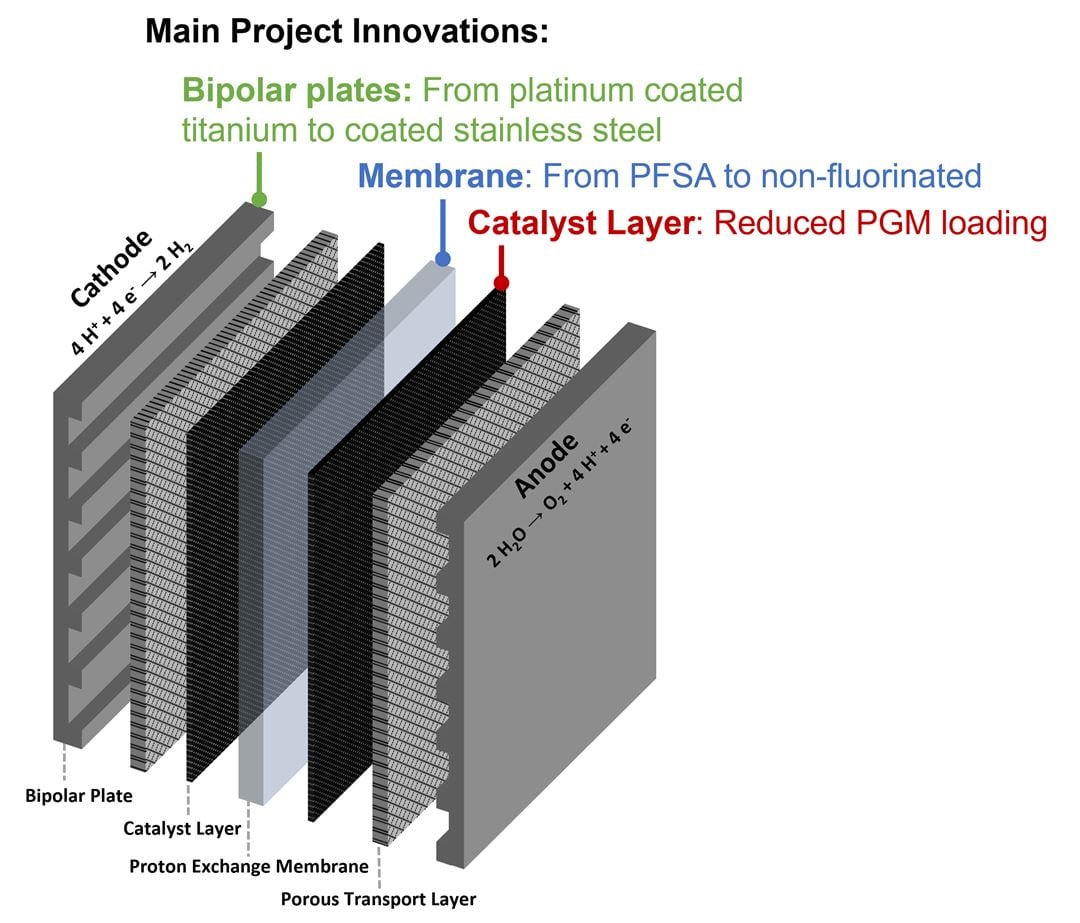