The world is in desperate need of metals. Realisation of the so-called green transition is entirely dependent on obtaining both the scarcer metals and those for which we have a plentiful supply. However, the recovery of metals from the minerals we mine results in by-products that all too often end up as waste. This waste may also have major local and global impacts on nature and the environment.
Some of the research that we are conducting at SINTEF involves finding out how this waste can instead be used to provide us with more metals. We are now aiming to recover iron, cobalt, scandium and many other critical metals from these waste products.
Turning a problem into an opportunity
The problems associated with metallurgical waste disposal are obvious. But they may also offer us opportunities. And just as the demand for metals and other critical raw materials increases, new commercial initiatives will also emerge.
SINTEF is currently heading a major EU-funded project called HARARE. This involves a partnership with nine other European organisations who are aiming to use hydrogen to recover copper and aluminium from copper slag and bauxite residues (so-called red muds), respectively.
HARARE stands for ‘Hydrogen As the Reducing Agent in the REcovery of metals and minerals from metallurgical waste’.
“For every kilo of copper produced, we’re left with 2.2 tonnes of slag.
Three megatrends
There are three megatrends currently driving inevitable future increases in demand for metals. These are the transition to the use of renewable energy sources, the increased use of electric cars and the development of so-called smart cities.[1]. Copper and aluminium represent two metals that will continue to be important in the years ahead. Aluminium weighs relatively little and is corrosion resistant, making it an important construction material, among other things. Copper is a very effective conductor of heat and electricity and is easy to recycle. Sixty-five percent of all the copper produced since 1900 is still in use today[2]! These properties mean that the demand for aluminium and copper will continue to increase.
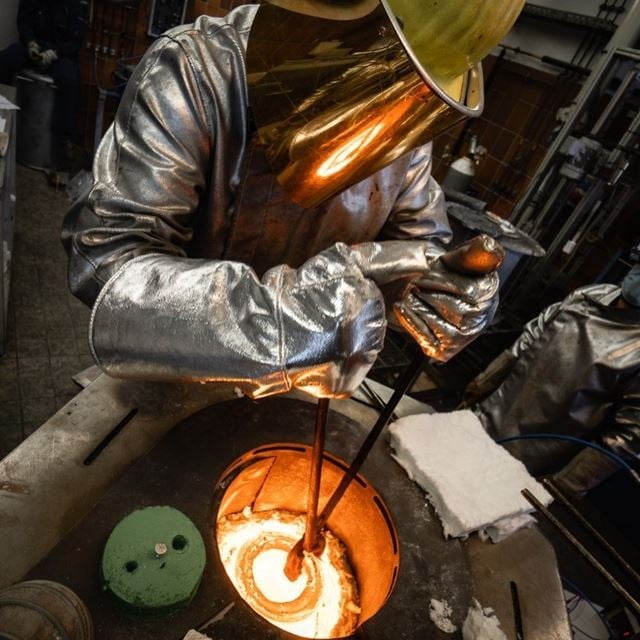
Tests being performed using copper slag at the RWTH Aachen University in Germany. Photo: Tom Gertjegerdes
The challenge we face is that standard aluminium smelting processes generate about twice as much red mud waste as aluminium metal. Red mud is very basic and is commonly dumped in reservoirs that occupy large areas of land. As well as creating major land use problems, red mud also represents a potential source of pollution and a safety risk to areas in the vicinity of the reservoirs.
Similarly, for every kilo of copper we produce, we are left with 2.2 tonnes of slag. In the EU, as much as four megatonnes of copper slag is produced every year[3]. Globally, the aluminium industry produces 160 tonnes of slag waste each year – equivalent to about 20 kilos per inhabitant[4]. If production of these metals is now expected to increase, the problem of waste will only get worse.
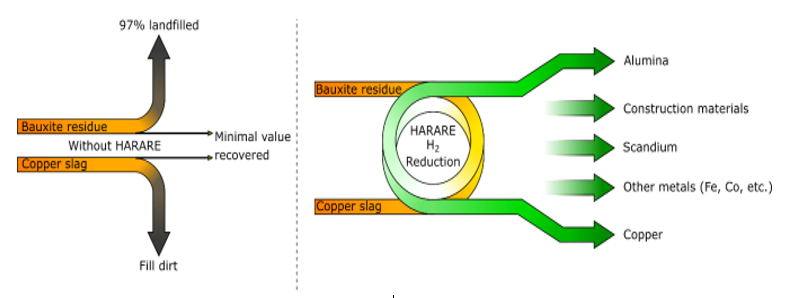
Left: In a traditional linear economy, only very minimal volumes of metallurgical waste are used for other applications. Most of the waste remains as such and is dumped in large landfill sites. Right: In a more circular system, all of the value in the waste is exploited. Dumping is minimised and in ideal situations is eliminated entirely. The aim of the HARARE project is to use hydrogen to recover rare minerals and metals from the waste streams of our aluminium and copper industries. Diagram courtesy of SINTEF
Six-fold increase in demand
In theory, metallurgical slags containing mineral and metal residues may represent a resource. However, one of the challenges is that these residues contain only low concentrations of the metals and minerals of interest. For example, it is possible to recover copper from copper slag that contains more than one percent of the metal. Slag that contains less than one percent copper will normally be regarded as waste and dumped.
The challenge we face is that standard aluminium smelting processes generate about twice as much red mud waste as aluminium metal.
Other rare and valuable metals and minerals occur in even smaller concentrations. The concentration, the nature of the mineral mixture and how these occur in the slag material will determine how difficult it is to recover the pure metals. However, it is becoming increasingly important to identify methods for such processes that can be industrialised.
The International Energy Agency (IEA) estimates that the demand for critical materials will increase six-fold by 2040 if we are to achieve the zero emissions target by 2050[5]. The EU is operating with the express target of being self-sufficient in critical raw materials, but at present, we are a long way from achieving this target.
While it may be profitable to recover metals from smelting slags, it is also necessary to reduce CO2 emissions generated by metallurgical processes. Metals production is universally energy-demanding, so it should be possible to reduce what we call ‘indirect emissions’ by selecting better energy sources and optimising the smelting process. On top of all this, metals production will almost always generate CO2 emissions simply as a result of the production process. These are called ‘direct emissions’, which can only be reduced by capturing the CO2 produced or by not generating any CO2 in the first place.
Where does all this CO2 come from?
In order to find out whether it is possible to entirely remove direct CO2 emissions, we first have to look at how the gas is generated. Most metal ores exist as oxides in which each metal atom is bound to one or more oxygen atoms. In such relationships, the bonds between the atoms are very strong and we have to use a lot of energy to break the bonds and release the metal. We also have to tempt the oxygen atoms to find affinities with alternatives to the metal atoms which they find so attractive.
Oxygen atoms are not only fond of metal atoms. They also find carbon atoms very attractive It is for this reason that during the smelting process, we mix the carbon atoms that occur in coal or wood chips with metal oxides in large ovens. We input large amounts of energy, often in the form of electricity, and produce the metals we are seeking, together with CO2. We say that the carbon has reduced the metal and that the carbon is thus a ‘reducing agent’.
What about water instead of CO2?
We all know that oxygen atoms mix readily with hydrogen. After all, it takes one oxygen atom and two hydrogen atoms to make a water molecule. Could it be possible to produce a pure metal and release water instead of CO2? This sounds too good to be true and for some metals this approach simply doesn’t work. Hydrogen is not always a sufficiently effective reducing agent, although theoretical calculations and lab experiments indicate that it should be possible for several metal oxides to achieve either complete or partial reduction using the hydrogen in water.
Waste, land use and greenhouse gases
As part of the HARARE project, our aim is to tackle several problems all at once. The world needs more metals. But this will only generate more waste and increased land use, both in the form of mining and the excavation of landfill sites. Not to mention all the CO2 emissions. We want to see specific methods developed for the recovery of residual aluminium and copper, as well as iron, cobalt, scandium and many other critical minerals from the two major copper slag and red mud waste streams. The use of hydrogen will enable us to make the metallurgy sector both circular and carbon-free.
My colleague Casper Van der Eijk is Project Manager for the HARARE project.
Follow us on social media:
- On Instagram: @h2020_harare (https://www.instagram.com/h2020_harare/)
- On Facebook: @H2020harare (https://www.facebook.com/H2020harare)
- On LinkedIn: HARARE (https://www.linkedin.com/company/harare)
- On Twitter: @H2020_Harare (https://t.co/tjbnMPXyJ6)
Sources:
[1] Megatrends to Increase Copper Demand.pdf
[3] International Copper Study Group (ICSG), The World Copper Factbook 2021
[4] Safarian and Kolbeinsen, Sustainable Industrial Processing Summit SIPS 2016, Vol. 5: Starkey Intl. Symp. / Mineral Processing, pp. 75-82
[5] The role of critical minerals in clean energy transitions