The focus of their work is the gas, oxygen, which forms bubbles in the silicon during cell manufacture. The presence of oxygen reduces cell quality to the extent that large amounts of silicon that could be turned into high-quality solar cells either go to waste or end up as low-efficiency solar cells.
To combat this, the researchers are experimenting with changing the flow pattern in the molten silicon during manufacture, so that the oxygen distributes itself more evenly within the raw material.
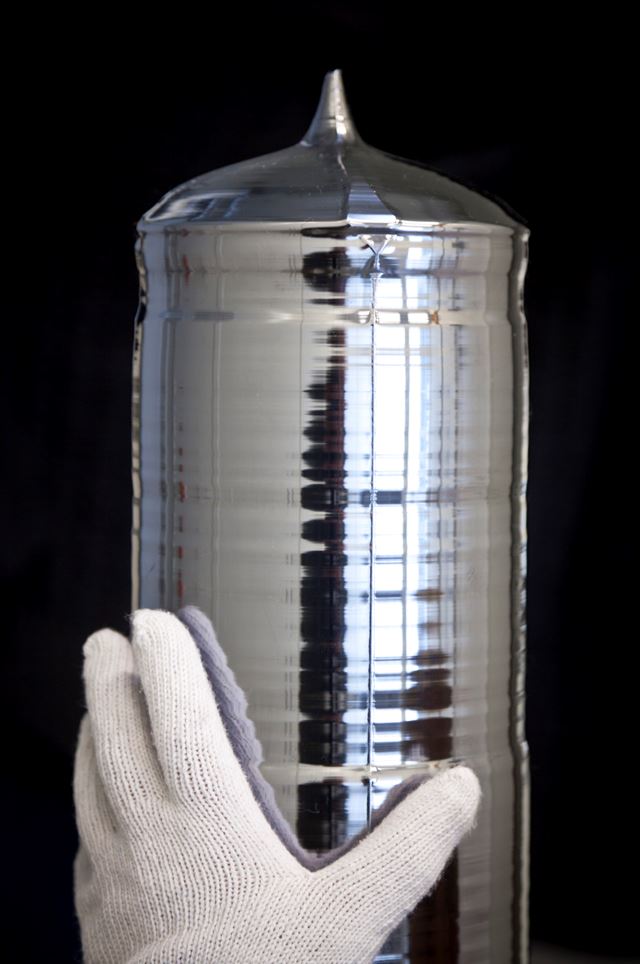
This is what the silicon crystal looks like after it has been extracted from the crucible. Photo: Thor Nielsen.
Solution lies in the crucible
“In order to manufacture the silicon wafers used to make solar cells, we use almost one hundred percent pure silicon”, explains Martin Bellmann, a research scientist at SINTEF. “The silicon is melted in a container, a so-called crucible, and a single cylindrical silicon crystal is then extracted from the melt. The cylinder is then cut and shaped into a square block, which is then sawn into extremely thin silicon wafers just 0.13 millimetres thick”, he says.
Bellmann is heading the Norwegian-Indian research project called SUCCESS, which is working towards optimising the silicon smelting process.
“Each wafer is used to manufacture a solar cell that can be connected to a solar panel that captures energy from the sun and converts it into electricity”, says Bellmann.
Energy- and resource-demanding
The problem with the current manufacturing method is the variation in oxygen content of the crystal extracted from the melt.
“The oxygen content is too high at the beginning and then reduces towards the end of crystal extraction”, says Bellmann. “As a result, the first 20 to 25 percent of the cylinder is unsuitable for the manufacture of high-efficiency solar cells. Nor does this silicon meet the material quality requirements demanded by the solar cell manufacturers”, he says.
This means that silicon crystal manufacturers have to cut away that part of the cylinder containing too much oxygen.
“This can be mixed with new silicon and used to extract a new crystal, but it is not possible to use all the material. The process is very energy- and resource-demanding, and is vulnerable to the formation of crystal defects, which also make the silicon unsuitable for solar cell manufacture”, says Bellmann.
Searching for the optimal “mixmaster”
The aim of the project is thus to achieve a more even distribution of the oxygen, which the researchers hope to do by changing the flow pattern within the silicon melt.
“The standard process involves rotating the crucible at a constant velocity in one direction while rotating the crystal, also at a constant velocity, in the opposite direction”, explains Bellmann. “We’re aiming to find out the optimal rotation velocities for the crucible and the crystal in order to minimise oxygen content and ensure that the gas is more evenly distributed in the silicon”, he says.
The researchers are now looking into a variety of different rotation patterns. They have abandoned the idea of constant velocities and are experimenting with alternating between accelerating and decelerating rotation velocities.
First calculations, then a full-scale experiment
Up to now, the researchers have been making a number of advanced 3D flow calculations as a means of investigating which rotation patterns provide the optimal result.
“We are currently using a three-dimensional model representing real-world scales and geometries”, explains Bellmann. “Our test involves running numerical models on a super-powerful computer that is able to resolve all the detailed flow patterns in the silicon melt during extraction of the crystal”, he says.
The next step will be a full-scale experiment designed to verify the results of the modelling. This is the part of the project for which SINTEF is responsible. Project research partners at the Indian Institute of Technology Bombay (IIT Bombay) will then use the material to manufacture solar cells and solar panels in order to demonstrate the results.
The industrial partners in the SUCCESS project are the Norwegian solar cell manufacturers NorSun and Norwegian Crystals.
Hoping to minimise waste
The researchers are aiming to identify a method of mixing the melt that ensures that almost all the silicon extracted in a crystal can be used to make efficient solar cells.
“Some material will always be lost at the start of the smelting process”, says Bellmann. “However, if we succeed in optimising the process, we will also contribute towards making solar cells an even more eco-friendly product. Not only because we minimise oxygen defects, but also because we reduce raw materials waste. This means that we can manufacture even better and more efficient solar cells”, he says.
The project is being funded by the Research Council of Norway.