If you want to manufacture single prototypes or small-scale production series with plastics materials, injection moulding with 3D-printed moulds may be the way to go.
Imagine that the ski bindings manufacturer Rottefella has come up with a ground-breaking idea which they want to test before an important equipment expo next week. Where can they get quick and functional prototypes of the plastic parts? Injection moulding with a standard steel mould will take much too long.
Young and creative start-up entrepreneurs are experiencing a similar problem. Because steel moulds are so expensive, risky projects are likely to get shelved. Start-ups are simply not able to finance this sort of small-scale manufacture.
So a number of research groups and industrial partners have now joined forces to find a solution. They have launched the AddForm project with the aim of developing 3D-printed moulds in plastic materials, with the highest quality possible.
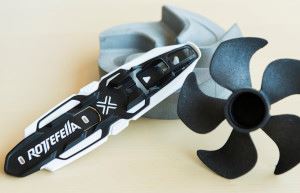
If you want just a few prototypes or small-scale production, 3D-printed moulds in plastic may be the way to go. Moulds of this type can then be made in a day or two, and the product can be injection moulded exactly the right plastic for the job. Photo: Werner Juvik/SINTEF
Click to open
From steel to plastic
“In mass production settings, machined steel moulds and 3D-printed steel mould components are just the job”, says Erik Andreassen at SINTEF Materials and Chemistry. “A good example is Lego’s production of its millions of bricks”, he says.
“But if you want just a few prototypes or small-scale production, 3D-printed mould inserts in plastic (or more correctly polymer composites containing ceramic or metallic particles) may be the way to go. Moulds of this type can be made in a day or two, and then the product can be injection moulded using exactly the right plastic for the job”, says Andreassen.
The right stuff
3D-printing, or additive manufacturing, was launched commercially more than 25 years ago, and researchers at SINTEF have been working in this field in many different projects through the years.
The aim of the AddForm project is to understand the performance of the mould materials in terms of the loading they are subjected to during the injection moulding process. In order for industrial manufacturers to obtain fast and satisfactory results, the materials must be tested and evaluated.
“There are a number of different 3D printing processes and a variety of materials types available”, explains Andreassen. “And all of them have their strengths and weaknesses when it comes to manufacturing moulds”, he says.
The researchers will also be working to identify quicker ways for assembling moulds and mounting them in the injection moulding machine. Another research topic is to find effective surface treatments to provide moulds with the desired surface finish.
The industry won’t just get fast and inexpensive prototypes. The injection moulded prototypes will also be made using the correct material – possessing the specified properties, and being ready for full-scale production.
“It’s important to note that for most industrial applications it isn’t yet possible to 3D-print plastic components with the ‘correct’ properties when it comes to attributes such as impact strength or fire resistance”, says Andreassen. “We have to take the injection moulding route in order to achieve this”, he says.
Global head start
The AddForm project was launched by OM BE Plast and SINTEF, who have since been joined by companies such as Rottefella, Stokke, Eker Design and Laerdal Medical.
There are several R&D groups worldwide working on mould manufacturing of this kind, but this Norwegian consortium believes it has a head start. It has already identified many effective solutions as yet not on the market.
It is also an advantage that the industrial partners are carrying out high-level product development, and most of the products are challenging. Many of the partners also have their own 3D printers.
OM BE Plast has already received many requests for manufacturing such novel moulds. “The technology is ready for some of these requests, but many will have to wait until we’ve obtained the answers and results we’re hoping for from this R&D project”, says Andreassen.