SINTEF mini-membrane pilot (ECCSEL) can accommodate membrane modules at an intermediate development stage for testing with real flue gas containing acidic gases (SOx, NOx) from gas burner with mini-blower (max 2 - 3 bar, ca. 1 Nm3/hr). The mini-pilot will provide an efficient and economic way of verifying membrane performances at realistic conditions before risky and costly pilot stage development.
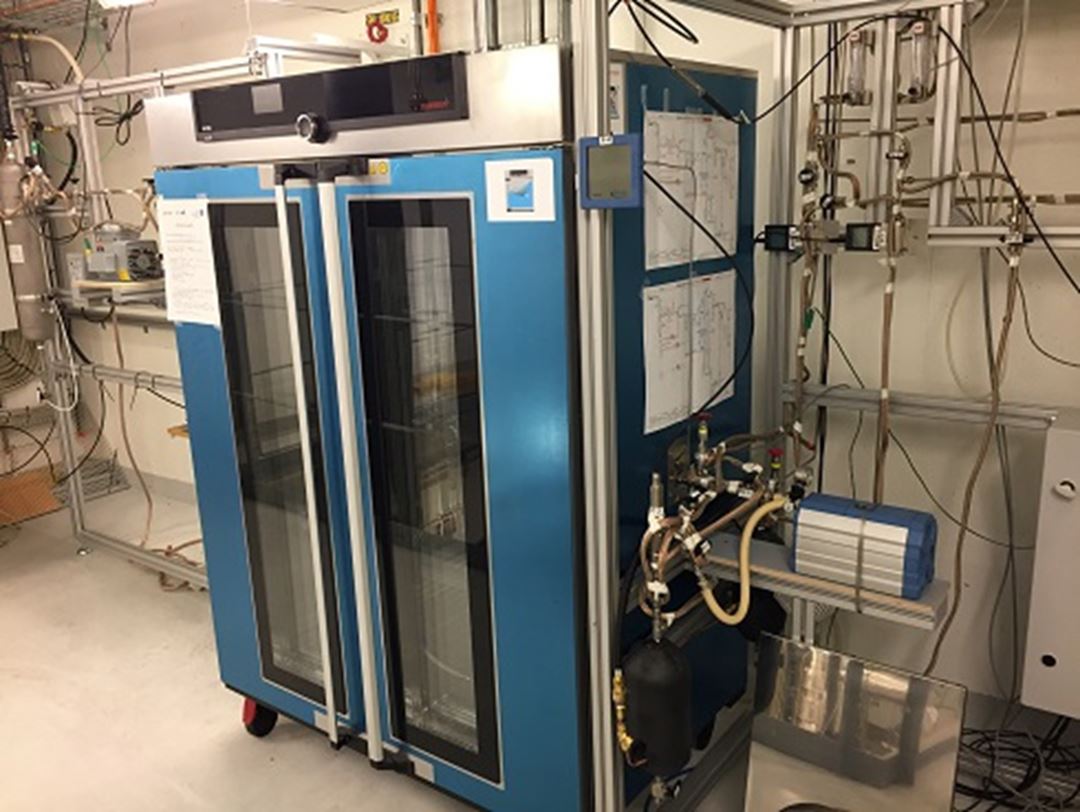
SINTEF high pressure membrane test rig (ECCSEL) equipped with mini-compressor can accommodate high pressure, high temperature and high CO2 containing gas mixture (e.g. CO2-CH4). The test rig is a universal laboratory scale facility which can take any type of membranes of different materials (flat sheet, hollow fibre, polymeric, inorganic, etc.), applicable for various mild and harsh conditions, e.g. for natural gas sweetening as well as flue gas CO2 separation.
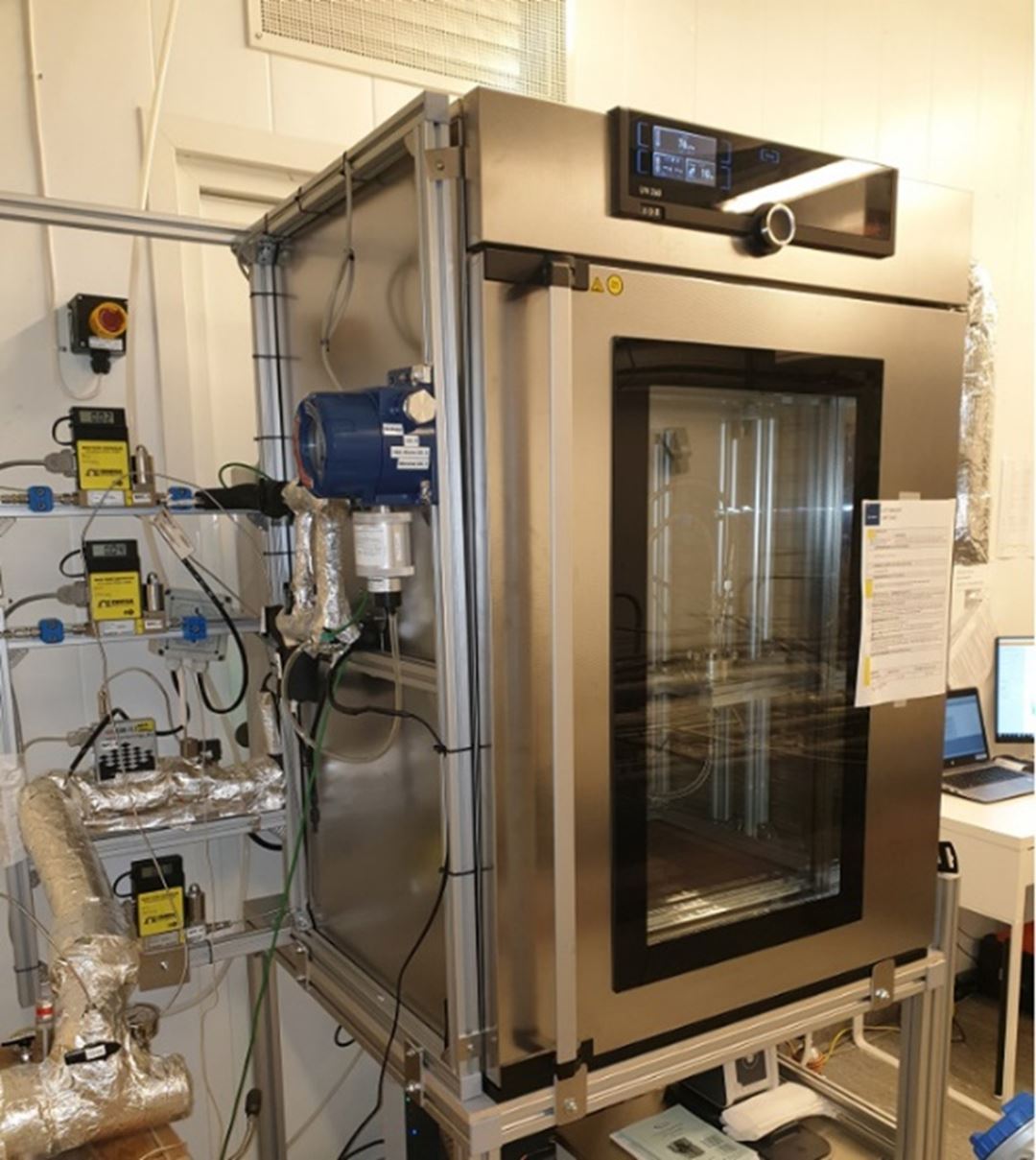
SINTEF compact hollow fibre spinning machine (ECCSEL) is suitable for efficient study of spinnability of new and unstudied materials (polymers, hybrids of polymer and inorganic materials, etc.). It can perform spinning test while easily changing various spinning parameters without the need for preparing a lot of dope solution.
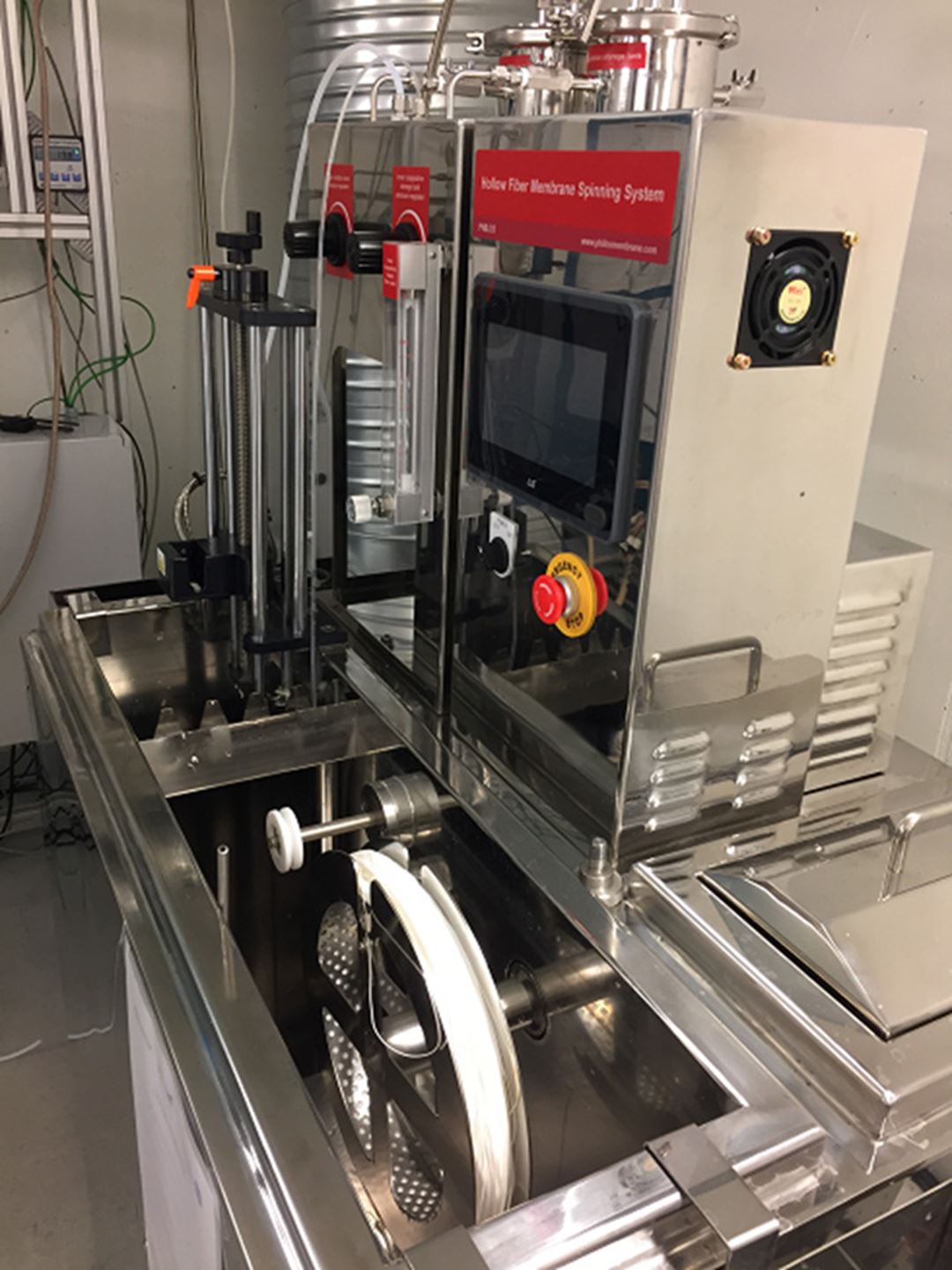
A pilot scale membrane test facility built in close cooperation with NTNU in the TillerCO2Lab can test commercial scale membrane modules (ca.4 - 10m2) with real flue gas from gas or coal/biomass burner. With the help of compressor the feed flue gas to membrane can be pressurized up to ca. 5bar (ca. 10 – 50 m3/hr) to test various process parameters. The acquired data and information can be processed further for process modelling and simulation by SINTEF experts.