The production of ferroalloys is one of Norway's largest land-based industries, consuming several thousand GWh of electricity per year. The industry is continuously working on reducing its diffuse emissions and greenhouse gas footprint in order to improve the plant working environment, meet increasingly strict governmental regulations and fulfil climate ambitions.
Traditionally, the industrial focus regarding energy and environmental issues has been on design and operation of the furnaces, as they are the largest source of emissions and energy loss. Some plants (e.g. Elkem Thamshavn and Finnfjord) have also installed energy recovery systems on the furnace off-gas. As the industry looks for further improvements, it is expected that the casting process will be a focal point in the future. It is the second largest surplus heat source in a ferroalloy plant and typically stands for 20-40% of particulate emissions, but extensive dust handling and energy recovery from the casting process has not yet been implemented in Norway.
The NECast project
When designing the next generation casting process, dust collection and energy recovery should be considered simultaneously to avoid the risk of sub-optimisation. In addition, a new system should include improved instrumentation for better control of product quality and eliminate safety risks connected to pouring of molten metal.
In the NECast project, the viability of such a next generation casting process will be demonstrated. The project is a Novel Emerging Concept within the FME HighEFF research centre. It started in August 2020 and will continue until May 2021. Below, a possible layout of the next generation casting process to be studied in NECast is shown. The pouring from ladle into casting moulds should be ventilated and could be performed in a closed environment or controlled gas atmosphere for fume suppression. Similarly, the casting moulds should be placed within a closed environment to minimise heat losses to the ambient surroundings and enable efficient heat recovery.
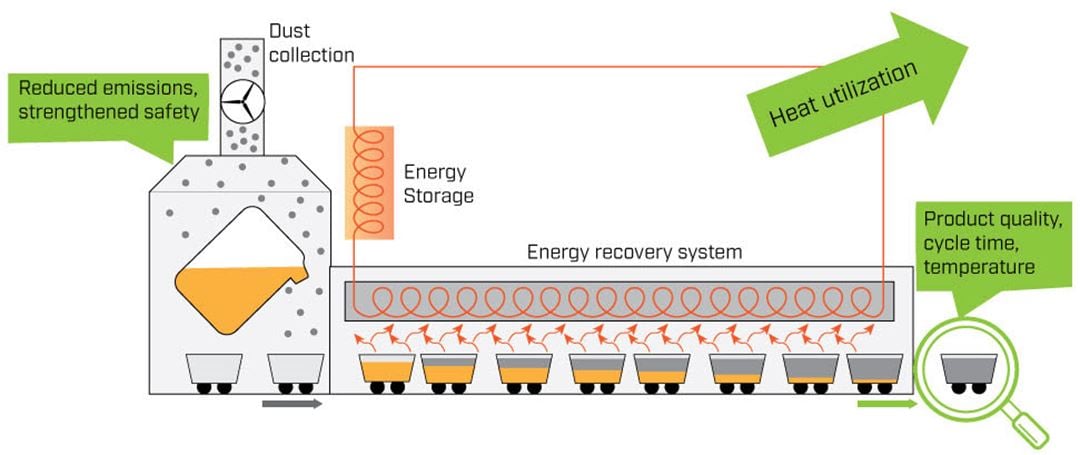
- From #SINTEFblog: Next-Generation Casting Process for the Ferroalloy Industry
Project partners: FME HigEFF consortium
Financed by HighEFF and Novel Emerging Concepts