Over the last 15 years Elkem has focused on silicon and silicon related products. The traditional products have been Silgrain, metallurgical grade silicon, ferrosilicon and foundry products, but since introduction of Elkem Solar Silicon® in 2009, a continuous work on product development has taken place including a BIA project focusing on Si to anodes in Li batteries. A general trend for the new markets is the need for small sized particles and the consequence for Elkem is to find robust technologies for making homogenous particles with desired properties. Traditional casting techniques cause segregation and uneven distribution of dope and alloying elements. They are also associated with significant generation of dust and fumes. The regulations on dust exposure in working environment will in coming years force the industry to change the process. Both challenges can be handled by thin casting methods. This opens a new window of opportunities on controlling the process for tailor-making product properties. Redesigning of casting equipment for thin casting opens up to improvements:
- towards more controllable solidification and cooling stages
- of the process yield by reducing the need for crushing.
A thin cast material has a different microstructure and thereby different product properties than thicker cast materials. The subsequent crushing step after casting will also benefit from the thin cast microstructure through the need of less energy for crushing, i.e. the degree of size reduction is smaller. Therefore, less low grade material called fines will be generated and the volume of high quality silicon will increase.
The main objective of the CorSiCa project is to develop a tool, Sistruc, for designing controllable, homogeneous microstructures in silicon, silicides and silicon alloys which make the products suitable for further processing to use in new applications like Li batteries and thermoelectric generators.
In order to achieve the ambitious goal of CorSiCa project, SINTEF will focus on:
- Developing a numerical model in order to predict the microstructure formation and intermetallic compounds precipitation depending on alloy and thermal history
- Providing support in establish an efficient method for microstructure characterization via advanced characterization techniques (e.g. SIMS, TEM)
- Developing a mathematical model for the novel thin casting process in order to understand the complex phenomena within the process
- Support the design of next version of the thin casting process by establishing the relation between process design and operating parameters
CorSiCa project in short:
BIA-IPN project supported by NFR from 2015 to 2017, total budget: 10.5 MNOK
Partners: Elkem AS (project owner), SINTEF, Teknova
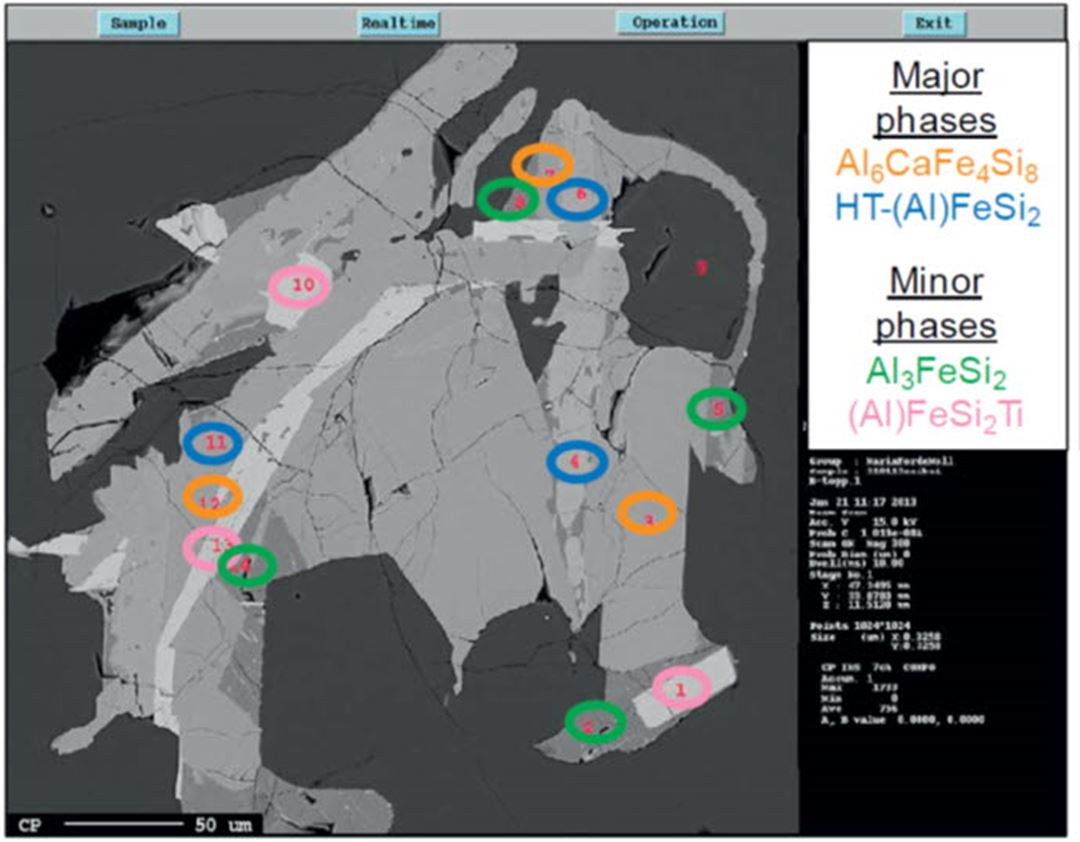