In this project a new aluminium casting equipment for casting of large-diameter billets of 7000-alloys will be developed by extending the recent Hycast Low Pressure Casting (LPC) technology and combining with an alloy based automation system.
Hycast aims at upgrading LPC technology towards automated casting of large dimension billets of 7000 alloys in this project. The alloy-composition based model will be developed to link with the automation system for calculation of casting parameters enabling alloy-based casting parameter design. The updated LPC technology will be designed with a wiper to reduce the cracking tendency for large dimension billets. In addition to the substantial commitment of Hycast and Hydro, this innovation will be implemented based on results from the research activities carried at SINTEF and IFE.
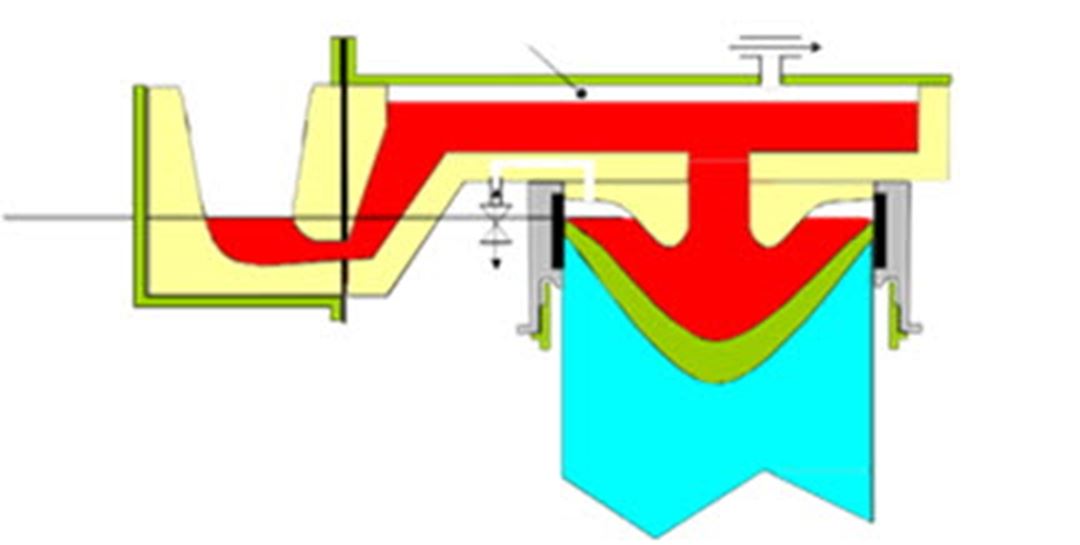
The main research methodology of this project is to combine advanced numerical simulation tools with dedicated laboratory and industrial scale experiments and trials. A microstructure model that is able to predict the correlation of the 7000 alloys composition and solidification conditions with as-cast microstructure will be developed. Design choices will be supported by processmodelling. Processmodelling will also be employed to address the relation between casting parameters and castability.
The successful execution of this project will enable the reduction in the thickness of the machined-off layer of an extrusion billet giving a potential of less scrapped material, or even eliminating the need for machining of the billets completely. The concept of alloy based casting design can be used to other alloy groups and will also be applicable to the other casting technologies.
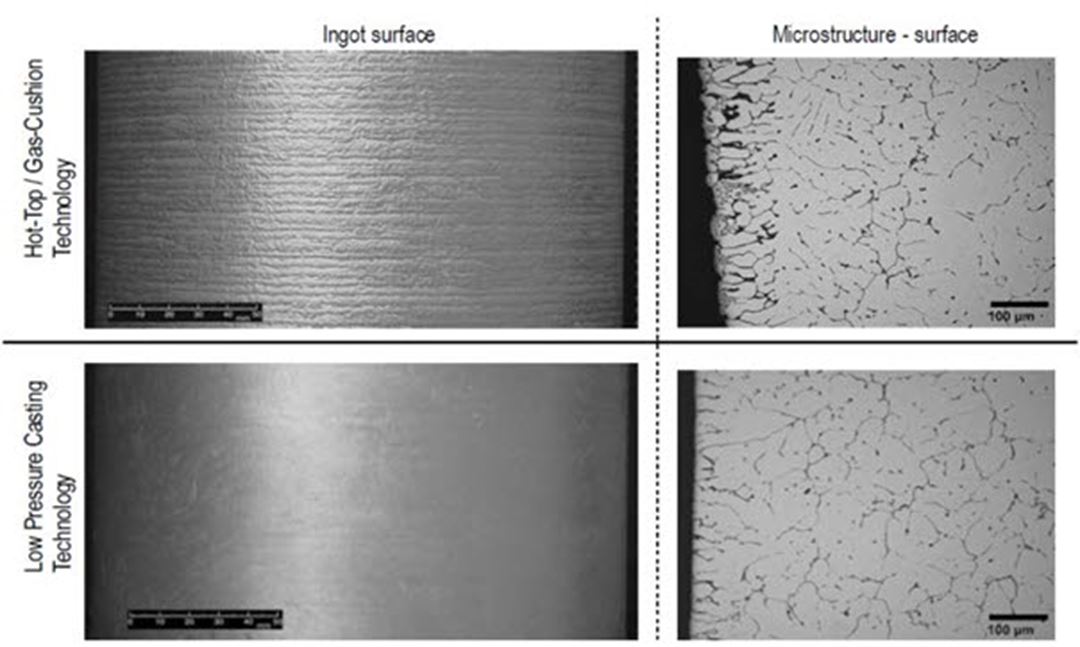
The project is an IPN (Innovation Project for the Industrial Sector) supported by the Research Council through the BIA-program. Project partners are Hycast, Hydro, SINTEF and IFE. SINTEF contributes with development of a microstructural model for 7xxx alloys and processmodelling to optimise the new design and the casting parameters. SINTEF also contributes to the development of an alloy based automation system.