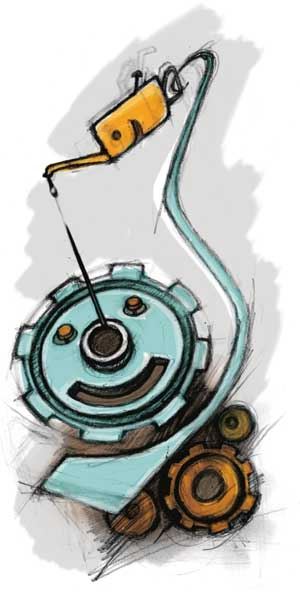
GOOD NEWS: A ball bearing – or a slide bearing around an axle – needs lubricating at all times.
Illustration: Line Halsnes
A ball bearing – or a slide bearing around an axle – needs lubricating at all times. If a leak causes the lubrication in the bearings of large machines to dry out, there can be huge cost implications. Metal surfaces can grate against
each other and seize up, in the worst case result ing in a total write-off.
Wind turbines, for example, have high maintenance costs, where an overhaul of their mechanical components alone accounts for 30 per cent. Other cost savings for the industry involve energy consumption, personnel, lubric-ation expenses and maintenance and spare parts.
Lubrication in tiny capsules
As part of an internal project at the Gemini Tribology Centre (friction, wear, lubrication), a group of researchers from SINTEFand the Norwegian University of Science and Technology (NTNU) have spent two years building ground-breaking expertise in coatings and thermal spraying. The researchers are now testing whether it is possible – where two metal surfaces are in contact with each other – to apply a coating to the sur-faces formed of hard particles and capsules filled with liquid lubricant. “We apply the lubricant using a thermal spray technique, where powder and capsules are fired at the surface using a flame,” says Sergio Armada of SINTEF Materials and Chemistry. “When the metal surfaces come into contact with each other, the coating is broken down in a controlled manner, releasing the contents of the capsules, and the lubricant will then prevent further friction.”
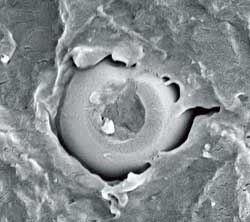
LUBRICATION: The coating of the capsule is broken down in a controlled manner, releasing the contents.
Photo: NTNU
The researchers have carried out a number of tests on slide bearings in industrial settings, in which they have measured friction on surfaces with and without the capsules. When a coating without capsules was applied to the slide bear-ing, the friction coefficient was 0.7, while friction was reduced to 0.15 in bearings coated with a layer of capsules.
Industry on the lookout
The idea of self-repairing metals is not a new one. Two years ago, a metallic coating of capsules and the “electroplated layer” lubrication method was presented in the Economist magazine. Materials researchers from Fraunhofer and the University of Stuttgart were behind the article. The disadvantage of this method was that since the lubrication was applied using electricity, it was only possible to apply a single metallic layer.
Another challenge was that the capsules in the coating were too big. Since a surface layer should preferably be only 15–20 micrometres thick, the capsules must be a fraction of this size if they are not to be released too quickly.
“In our case, the capsules must be smaller than 10 micrometres, so that they do not block the nozzles and cause problems during the spraying process. We have now created capsules as small as 2 micrometres,” says SINTEF researcherChristian Simon.
His colleague Ruth Schmid is producing capsules with an extremely low friction coefficient that could provide the coating with even better tribological properties.
Many applications
“Our method has many potential applications, and is suitable for a wide range of coatings,” says researcher Sergio Armada. “It will be possible to apply the coating to large surfaces and components, and the actual material of the coating can also be varied – from metals to polymers and ceramics.”
Armada thinks that the coating could also be used in the medical sector in hip and knee replacements. These are also places where surfaces move against each other, and grating can occur if there is not enough fluid in the joint. Patients would therefore benefit from lubricants applied in a coating of capsules which is sprayed onto the implant before it is inserted. Nuria Espallargas and Ragnhild Aune of NTNU are working on new materials that have capsules filled with medication or antibiotics that can be released when they are needed.
The project has now come to an end, but the parties have written a project proposal and have applied to the EU to be able to continue their work on thermal spraying and biocompatible coatings.
See http://www.ntnu.edu/ipm/gemini-center
Åse Dragland