In iProcess we are currently working with grasping of fragile food objects such as lettuce. Lettuce is an irregular, fragile compliant object of variable shape and size. Lettuce is a highly fragile product that requires adaptability when it comes to tactile sensing and exertion of forces during grasping. A RGB-D sensor is used to capture the images and algorithm extracts the relevant visual features necessary for estimating the grasping pose. Preliminary results are very promising.
Robotic grasping
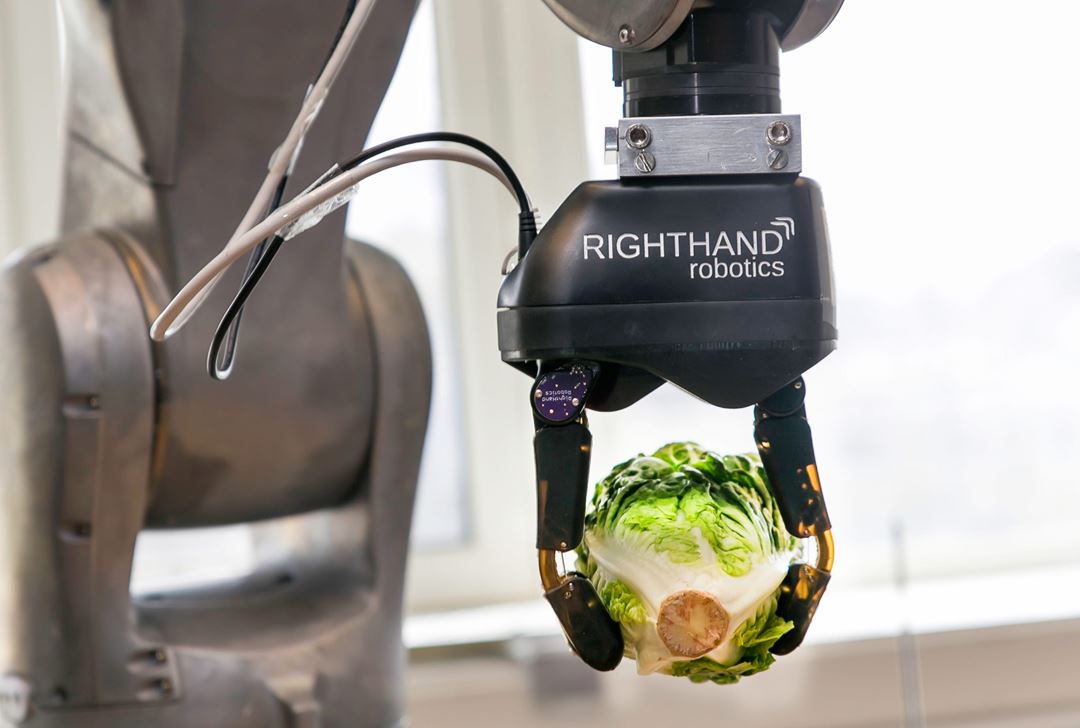
One of the greatest challenges in robotics today is the contact processing of a robot with an object and dexterous handling of compliant objects. This is particularly emphasized when it comes to dealing with handling and grasping in harvesting, post harvesting and processing operations of fragile and compliant food raw materials. The food industry is showing and increased interest for flexible robot based automation solutions that are also suitable for small-scale production volumes. Robotic optimal grasping and imitation of the complex manual dexterity of skilled human operators is therefore a prerequisite to enable a higher uptake of robotic automation in food industry.
Project Information
Project duration:
01/04/2016 - 12/12/2019