The construction of offshore wind and solar farms requires electrical cables, both as components of the farms themselves, and to carry the generated electricity onshore. Operators responsible for handling the cables during their manufacture, transport and installation have from time to time found that they quite literally have a tendency to twist and curl up. The same thing can happen to a rope when a climber is abseiling.
The tendency for subsea electrical cables and flexible pipes to twist during their manufacture, handling and installation is a phenomenon that up until now has proved difficult to explain. It is a major drawback during handling and storage, and can be very expensive.
“It will perhaps come as a surprise to many that the torsion is caused by friction inside the cable”, says SINTEF researcher and torsion enthusiast Philippe Mainçon.
Cable torsion can cost millions
There are many examples of instances where internal friction has caused major problems.
“In one case, a vessel had to abort the installation of a major electrical cable due to the cable writhing and curling on deck, says Mainçon, who has been called ‘Dr. Twist’ by one of SINTEF’s clients.
The cable had to be cut and abandoned on the seabed. The vessel returned to port and had to wait for months before the cable could be recovered, spliced together and the installation completed.
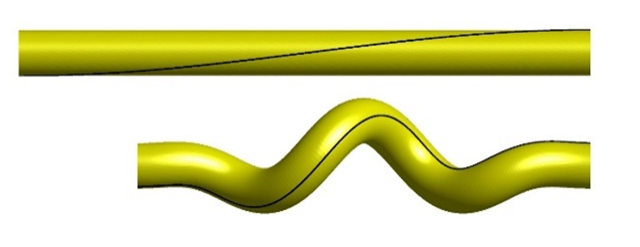
A cable exhibiting torsion (above) and writhing (below). Illustration: SINTEF
A cable can also incur localised damage, which in the best case can be beaten back into shape or spliced. In the worst case, however, the cable may have to be replaced.
“In some cases it can be difficult to determine there is damage to the conductor or the insulation”, says Mainçon. Damage of this kind can result in the failure of cables under operation, causing outages for large numbers of consumers”, he says.
An old problem, poorly researched
Such problems are old news. The oil industry has also experienced some incidents of this kind, with some incidents costing tens of millions of Euros.
“However, with the exception of our own contributions, we find no scientific literature published on this topic”, says Mainçon. “Nor are there any reporting requirements for such incidents, because they don’t cause injury to personnel or lead directly to environmental pollution. Moreover, no-one wants to tell the world about their embarrassing mistakes. As a result, the industry has too little knowledge of this phenomenon”, he says.
But now SINTEF has done something about the problem. In recent years, researchers have participated both in cable damage investigations and design support in collaboration with Norwegian and foreign companies, and their involvement has produced a important new knowledge.
“Even experienced engineers can be surprised by the level of advanced mechanics needed to explain the causes of the torsion we observe”, says Mainçon’s colleague Vegard Longva.
Climbing expertise
The two researchers, who are both enthusiastic climbers, have applied their scientific expertise when handling climbing ropes during their time off.
“We both have experience using climbing ropes, and this has helped us to gain insights into cables because some of the physics involved is exactly the same”, says Mainçon. “An effective installation vessel has more in common with a good belay device than you might think”, he jokes, while at the same time emphasising that the development of both mathematical and numerical models play a key role in their investigation of this problem.
Several mechanism can cause torsion in cables. One of the most important is linked to the fact that when a cable is guided, for example from the manufacturing facility onto the installation vessel, it is being bent in different directions.
“It’s easy to see that a lot of force is needed to bend a large cable and cause the reinforcement threads to start sliding”, says Longva. “But here comes the surprise”, he says, inviting us to make a small experiment.
“Put a piece of tape halfway along a piece of cable and bend it, for example into a downward bend. Then try to hold the bend in position while rolling the cableso that the tape takes a turn around the cable. You’ll be surprised how much force it takes. These same forces can damage during handling”, he says.
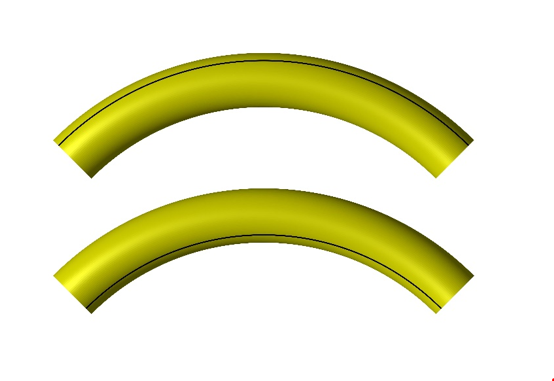
Bend the cable like this and try to roll it. It’s surprisingly difficult. Illustration: SINTEF
“No-one would build a major bridge without having made calculations to ensure that the structure will be sound”, says Mainçon “The same principle should apply to cable handling when we construct a cable manufacturing facility or an installation vessel”, he says.
The industry requests guidance on how to estimate torsion loads, equipment for the real-time monitoring of operations, and test rigs designed to evaluate the capacity of a cable to tolerate torque.
The researchers are now setting about the task of disseminating their new knowledge by means of the commercially-funded ‘Torsion Joint Industry Project’, in which many overseas cable manufacturers, installers and operators are taking part.
Dissemination will be achieved by means of workshops and a handbook that is currently in preparation. There are also plans to develop specific guidelines for torsion calculations.
“Complex situations in which torsion results in unfavourable geometries that in turn lead to further torsion will require highly specific numerical models, so there is no shortage of work ahead of us”, says Mainçon. “But our aim is clear – to ensure that the journey to fossil-free energy occurs without tangles”, he says.
Participants include Hellenic Cables, NKT HV Cables, Equinor, Aker Solutions, Ørsted and Petrobras.
- You can read more about torsion on this project webpage.
Publications:
- Vegard Longva and Svein Sævik. A Lagrangian-Eulerian formulation for reeling analysis of history-dependent multilayered beams, Computers and Structures 146 (2015) 44-58.
- Vegard Longva and Svein Sævik. On prediction of torque in flexible pipe reeling operation using a Lagrangian-Eulerian FE framework, Marine Structures 46 (2016) 229-254.
- Philippe Mainçon, Torsion in flexible pipes, umbilicals and cables under loadout to installation vessels, OMAE 2017, 62716.