Is a facility adequately anchored? Are the wet-well vessels in the right place at the right time? Do the net pens have weaknesses which can result in escapes? It’s now possible, with the help of a couple of key strokes and techno assistance from above, literally to obtain an overview of all these issues.
“The use of small unmanned aircraft, or drones, and “flying eyes” (cameras attached to remote-controlled helium balloons) opens the way for new opportunities linked to the documentation and inspection of both facilities and marine operations”, explains SINTEF researcher Eirik Svendsen. “This is why we’ve started testing this technology”, he says.
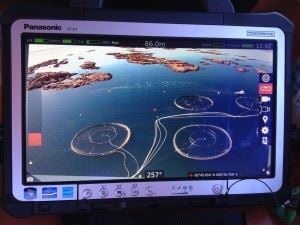
The equipment is an ideal decision support tool, according to the scientists. Foto: SINTEF.
Click to open
The project, named Sensodrone, has recently conducted experiments with these types of equipment at an aquaculture research facility, and the results are very pleasing.
“The equipment has provided us with excellent and very detailed images”, says Svendsen. “For example, we were able to see how the fish behaved when the nets were drawn in. Such observations make the equipment ideal as a decision support tool. The images obtained also provided us with good information about aspects such as HSE factors, combined with aerial views of the locations of vessels in use”, he says.
Exposing potential weaknesses
One of the applications envisaged by SINTEF is that aerial images can be linked to drawings and other information about the facility, making it possible to identify and compare non-conformances related to issues such as moorings or the deformation of floating collars. In this way we can obtain early warnings of weaknesses which in the worst case may lead to ruptures in equipment and subsequent escapes.
Facts:
The project is being funded by the Research Council of Norway's MAROFF programme, together with the following industrial partners:
SIMICON: A service and equipment supplier (video documentation and airborne vehicles).
MARITIME ROBOTICS: A service and equipment supplier (unmanned water- and airborne vehicles).
KONGSBERG SEATEX: Equipment supplier (supplier of the decision support system and navigation sensors such as AIS, among others).
SEMEKOR: Works with Norwegian and global network building, project management and concept development linked to safe and efficient marine transport.
The “flying eye” can also be equipped with a so-called AIS (Automatic Identification System) transponder which makes ongoing operations visible. This may be useful for other vessels in the area.
More stringent documentation requirements
The reason behind the testing of this equipment is that the aquaculture industry is having to meet increasingly stringent documentation requirements in relation to HSE issues, pollution and escapes. When an accident occurs, it must be possible to record exactly what happened.
“Since this technology also makes it possible to record video material, it will make the work of investigating incidents and non-conformances that much easier. We will be able to see what happened, when and how”, says Svendsen.
Arctic experience
SINTEF has demonstrated this type of equipment previously in collaboration with the Norwegian Coastguard, and obtained good results in connection with monitoring of a fisheries inspection in Arctic waters.
However, the equipment can also be used for activities such as search and rescue, oil spill response operations and to assist vessels sailing in frozen waters.
“We now intend to look into the requirements necessary to ensure that airborne monitoring devices can operate safely in the marine environment”, says Svendsen. “Our guiding principle has been the need for steering and control capabilities, combined with adequate communication between the operator and the technology”, he says.
In this experiment, researchers used the “OceanEye” system supplied by Maritime Robotics (photo). The balloon, which is equipped with a remote-controlled camera, can remain airborne and will supply clear aerial images, even in “fresh breeze” conditions. The experiment was carried out at the Rataran facility, operated by SALMAR and ACE. The latter carries out the development and large-scale testing of new aquaculture technologies.