An outstretched hand gives me a firm welcome. Then it pulls on a big blue glove and dives into a brown paper bag. A second later, chief scientist Aud Wærnes has a fistful of stuff that could be icing sugar – if only it hadn’t been pitch black.
“Did you know that car tyres were white until the world got powder like this?”, says the quiet Norwegian voice, then she continues:
“This stuff is dirty and messy. But if everything goes according to plan, it will soon be in use as an ingredient in a process that will help to make tonnes of a metal which will be pure enough to be turned into solar cells.”
Her voice is eager. For ten years, Aud Wærnes and her colleagues have been involved in a race to give the world more solar cell-quality silicon, a scarce material. Now they can see their goal approaching.
In her glove, the SINTEF scientist is holding billions of carbon particles, known in the trade as Carbon Black. Most industrial-quality Carbon Black still ends up in car tyres, but the version that is being produced by SINTEF and its partners is far purer.
Ultrapure carbon
Carbon is what silicon smelting furnaces need to be fed with in order to convert quartz to metallic silicon, which is the principal component of most solar cells. Starting with ultrapure carbon, SINTEF, the Norwegian metal manufacturer Fesil and a handful of international partners have developed a new process for producing solar cell quality silicon.
The results were so promising that this autumn, Fesil’s subsidiary Fesil Sunergy decided to base industrial pilot production of solar-cell metal on the process. Aud Wærnes makes it quite clear that we are talking about silicon produced at much lower cost and with lower energy consumption than the traditional raw material for these cells, but will it still give us efficient solar cells?
If all goes well, the first factory, to be built at a cost of more than a billion kroner, will be completed by 2011 and will provide between 100 and 150 jobs. The tug-of-war over where it is to be sited is already under way.
Yacht race was step-father
In the autumn of 1997, two men met on a quay in Cape Town. That is where it all started; the story that has turned Aud Wærnes and her colleagues into solar cell pioneers.
The Whitbread Round the World Race circus had just arrived in South Africa. Thirty days after the start in Southampton, “Innovation”, the Norwegian entry, moored to the quayside in Cape Town. The boat was skippered by Knut Frostad and was sponsored by Kværner.

Aud Wærnes led SINTEF’s and Fesil’s solar cell project since its predecessor started in 1988 until 2005. Today, she is in charge of all of SINTEF’s metallurgical activities. Her colleague Caspar van der Eijk is now project manager.
Photo: Geir Mogen © SINTEF Media
Click to open
The Norwegian industrial company had a development project that was being run by Aud Wærnes and her colleagues. The partnership had resulted in a new process for splitting natural gas into hydrogen – much in demand – and ever-increasing quantities of Carbon Black.
Adding Carbon Black to tyres makes them strong and resilient. The standard product used in tyres is produced from heavy oil from refineries. Natural gas, which is the raw material used by SINTEF and Kværner, is much purer, leaving the project partners with a type of carbon that contains far less foreign matter than ordinary Carbon Black.
As the yachts arrived in South Africa, two men were meeting and wondering whether the ultrapure black powder could find a new application beyond the walls of tyre factories.
One of these men was Kværner’s “hydrogen and Carbon Black boss”, the late Steinar Lynum. The other was Benno Wiersma, a Dutch businessman who was extremely enthusiastic about both sailing and renewable energy.
Lynum was keen to find alternative uses for Carbon Black, while Wiersma wanted to make money from solar cells.
Triggered by long-distance call
While the two men were chatting near the southernmost point of Africa, the solar cell industry was satisfying its still relatively modest hunger for silicon by consuming the leftovers from the electronics industry’s plate.
Most solar cells employ a thin wafer of silicon, one of the most common materials on the earth’s surface, as their active core. Silicon is the main component of quartz, in which it is combined with oxygen.
The two elements are separated at a temperature of 1800 degrees Celsius by the ferroalloy industry, from whose furnaces emerges melted silicon, known as metallurgical silicon, which is mostly used as an additive in aluminium alloys and to produce pure silicon, an ingredient in everything from jointing paste to cosmetics and babies’ dummies. This material cannot be used direct from the furnace to generate solar power, as it first needs to be purified of other elements, traditionally an expensive and energy-intensive process.
Throughout its infancy, the solar cell industry has obtained its pure silicon by purchasing surplus material from producers of raw materials for the highly demanding electronics industry. Solar cells are made from manufacturing rejects and cutoffs from the ingots of ultrapure silicon that are used to make the chips for PCs and other electronic devices.
BennoWiersma was aware of the solar cell industry’s anxiety that sooner or later there would be a shortage of these traditional materials – metal that is purer than the solar cell industry really needs, since solar cells do not require silicon as pure as PC chips do.
Wiersma and Lynum also knew that ferro-alloy plants use coal and coke in their furnaces to bind the oxygen in the quartz and thus separate it from the silicon.
“Did you mention “downturn”? We had lots of difficulties from 2002 until 2004.”
Aud Wærnes, Research Director
While Africa’s sun was shining over the Cape, the two men asked themselves if the ultrapure carbon from SINTEF could be substituted for coal and coke and become the key to a new type of smelter that would serve the solar cell industry. In other words, could this material, because it contaminates the metal less than coal or coke, produce silicon straight from the furnace that would be pure enough to be used in solar cells?
The men agreed to ring Trondheim and ask SINTEF.
Hotter than Dante’s Hell
Eleven years on, the calendar says 2008.
“We accepted the challenge right away,” Aud Wærnes remembers, adding: “Several years of research had already given us wide-ranging competence in producing metallurgical silicon. We had also worked on solar cell-quality silicon back in the 80s. For us, it was really exciting to be able to examine this topic at close hand.”
She has just shown me into a high-ceilinged laboratory that looks like a workshop. We are surrounded by grey concrete walls in the heart of the Gløshaugen university campus in Trondheim. On a gallery above us towers a steel-clad monster, a presence that Wærnes and her colleagues are very fond of.
On the outside, the machine seems to consist of black pipework and heavy nuts and bolts, but Wærnes is more interested in its inner workings, for this is where the process that gives us pure carbon was born.
This process is based on plasma technology, and the productive “womb” on the gallery is a pilot-scale metallurgical plasma reactor, I am informed. A plasma is a gas whose atoms or molecules have been ionized (i.e. have become electrically charged). If an electric current is passed through such a gas, it can reach extremely high temperatures.
Standing under this machine, I listen to the history of the solar cell project that has been under way at Gløshaugen virtually since Aud Wærnes finished her telephone conversation on that memorable day in 1997; a story with its ups and downs.
Pure carbon and pure quartz
The phone call from Africa led to a pilot project that She started with her colleague Ola Raaness. This was followed by an EU project, in which SINTEF was joined by one of Wiersma’s Dutch companies, plus the Swedish industrial company ScanArc and energy researchers from the Netherlands.
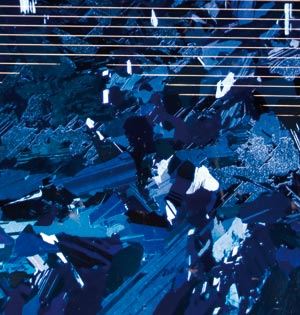
New production of solar-grade silicon
The lack of super-pure silicon has been holding back the growth of the solar energy sector. Norwegian companies are world leaders in the development of new, inexpensive methods of production of solar-grade silicon.
REC Silicon is building two new plants in the USA. These purify silicon in the gaseous phase and deposit the purified gas on silicon granules suspended in a fluidized bed reactor.
Elkem is about to open a brand-new plant outside Kristiansand; production will be based on a metallurgical process for purifying silicon.
Fesil Sunergy will start pilot production in 2009, based on a metallurgical process for the production of solar-grade silicon.
Hydro and Umicore are constructing pilot-scale equipment for the production of silicon for solar cells on the island of Herøya.
Photo: Thor Nielsen © SINTEF Media
Click to open
At Gløshaugen, Roar Jensen, Steinar Prytz, Ingeborg Solheim and Eivind Øvrelid were soon brought in, and all became long-term members of the project team.
The process being developed by the team has been christened “Solsilc”, a name that must not be confused with “Sunsilk”! Clean hair has no connection with this matter, although other pure materials do play a role. The Solsilc process uses not only pure carbon but also extremely pure quartz. Metal recovery takes place in a specially modified furnace, from which the metal is fed into another furnace in order to remove any carbon that is still dissolved in the silicon.
“Benno Wiersma’s vision was that we should contribute to the whole value chain, from metal production to creating acceptance for solar cells in society. It is not often that contract researchers like ourselves are handed such an opportunity,” says Aud Wærnes.
But she also remembers times when funds were tight and the project was put on the back burner.
“Did you mention “downturn”? We had lots of difficulties from 2002 until 2004.”
But it was in 2004 that the lack of traditional solar cell materials began to make itself felt, just as the growing solar cell industry had feared. Raw materials from the IT industry, which is not growing particularly rapidly, have become scarce. This adds weight to SINTEF’s argument that the new process will make it possible to produce solar cell material in large volumes.
At that time, the EU team was producing silicon in small pilot-scale batches, while carbon removal was taking place at a large laboratory scale. SINTEF invited Fesil into the project as an industrial partner, and the company accepted.
“An important turning point,” Wærnes points out as she looks back.
New fire in old halls
This brought in a player with 30 years of experience of producing metallurgical silicon.
“We very extremely pleased about this, as it gave us an industrial company that possessed a great deal of experience which could be transferred to the new process”, continues Wærnes.
After two years of cooperation with SINTEF and the other team members, Fesil and its Dutch project partners established the company Fesil Sunergy, with Fesil as its largest shareholder. In September 2008, the world was told that the company had got far enough to initiate full-scale test production of solar cell material, which will actually start during 2009.
The following day, I drive to a huge corncoloured factory building on the outskirts of Trondheim. The gate is closed, with not a puff of smoke to be seen from its six rusty chimneys. This is Lilleby Smelteverk, established in 1927 and once famous for producing the purest ferrosilicon in the world, until it closed in 2002.
Now the plant can draw a final, but vital, breath before it is demolished. This is where test production will take place. After the promising small-scale production phase in Sweden, Fesil Sunergy invested NOK 150 million (USD 21.5 million) in what is to take place in the hall in front of me.
Further to the east of the city, in an office building on the motorway to Værnes Airport, technical director Lars Nygaard in Fesil Sunergy shares office space with the rest of Fesil’s management team. Nygaard explains that full-scale test production is important, not least for the sake of deciding on the right production equipment.
Nygaard makes no secret of the fact that the project has its risks, as do all technological developments. But he also points out that the NOK 150 million (USD 21,5 million) investment is an indication of the strength of the company’s faith that the project will reach its goals. He tells me that any decision to build a new plant will be made in the second quarter of 2009 at the earliest.
“If we decide to build in Norway, it will probably be in Orkanger, but there are better possibilities of obtaining investment subsidies elsewhere in Europe, and that is tempting for the shareholders,” he says.
On the way back to town I stop at Gløshaugen, where Aud Wærnes has removed her dirty gloves and is sitting in her office. Since she took that decisive telephone call from South Africa eleven years ago, the Round the World Race has changed sponsor, name and route, and there are no Norwegian yachts in this year’s circumnavigation.
“All the same, we can always hope that life will offer an equally exciting phone call again,” smiles Aud Wærnes, ready for the next stage of this race for the sun.
By: Svein Tønseth