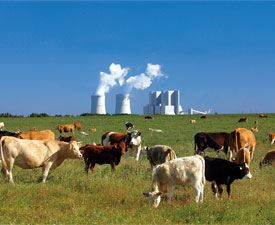
The Swedish Vattenfall company will be building an “all-green” coal-fired pilot plant in concert with this coal-fired power station in Germany.
Photo: Vattenfall
BERLIN/COTTBUS: Three pale grey housing blocks and a shabby, graffiti- laden workshop building flash past. Between the houses are glimpses of green meadows and low-lying forests. Half an hour out of Berlin, the train glides over miles of plains. The flat landscape rests on sand – transported from Scandinavia.
This last piece of information comes from my companion. “The ice brought the sand here during the last Ice Age”, explains Lars Strömberg, in his melodious Swedish. He is a director in the Vattenfall Group management team, and is Gemini’s “tour guide” in united Germany. Strömberg’s employers have made good money from the geological stratum that lies under the moraine sand.
One hundred metres beneath us, buried in light-brown sand, lies a thin layer of ancient plant remains, which time and the forces of nature have turned into brown coal: fuel for three huge power stations that Swedish Vattenfall owns here in the south-eastern corner of Germany.Wall-to-wall with one of them, Sweden will build a new plant that will turn Norwegian gas-power researchers green with envy.
SWEDISH ACTION
As the train winds its way through what used to be East Germany, Lars Strömberg tells Gemini more about his building plans. Just outside the village of Schwarze Pumpe, halfway between Dresden and Berlin, the Swedes are going to build a pilot version of an unusual coal-fired power station, the first in the world to capture the CO2 from flue gases.
Green electricity from brown coal is a promising innovation in a world that has four times as much coal as oil and gas together. Mankind will still be burning large amounts of coal in the future, no matter how much we invest in renewable energy. This reality has drawn even more attention to Vattenfall’s construction plans.
In Norway, SINTEF applied two years ago for public-sector support for a similar green effort on the gas-power side. However, it appears that gas-fired electricity generation with CO2 treatment is destined to remain at the laboratory stage in this country.
Meanwhile, Vattenfall was turning words into deeds. The pilot plant in Germany will be up and running by summer 2008. It will produce hot, high-pressure steam by burning brown coal. The energy input will be around 30 MW, enough for a steam turbine to produce 15 MW of electric power, which is sufficient, for example, to run 15,000 1 kW electric heaters.
In ordinary coal-fired power stations, CO2 makes up only about 12 – 14% of the flue gases, which makes it expensive to capture. But the pilot plant will discharge only clean CO2, explains Strömberg.
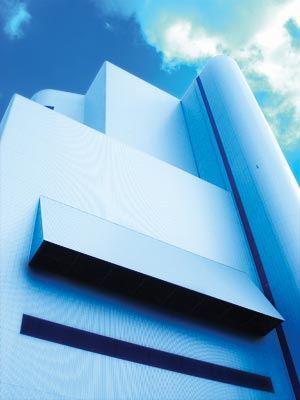
Behind this façade a giant furnace burns round the clock. The boiler of the Schwarze Pumpe coal-fired power station is 160 m high.
Photo: Svein Tønseth, SINTEF Media
ON BLOOD-SOAKED GROUND
Twenty kilometres from the Polish border we change to another means of transport. In the university city of Cottbus, Lars Strömberg climbs into a four-wheel-drive SUV. He is in his element as he drives me through the forest-covered plain – for this is territory with history.
Four hundred years ago, the Thirty Years’ War raged here, as the mercenaries of the King of Sweden and the German Emperor fought each other, and raped and killed civilians. The front moved back and forth, turning the local people into the victims of repeated raids. But some of the smarter locals realised what they had to do: they painted the water pump on village square black, the recognised warning of plague. After that, the people of Schwarze Pumpe (Black Pump) were left in peace.
“When we bought the power stations here four years ago, some Germans joked that Sweden had conquered them again”, says Strömberg as he brakes. I can see that we are nearly there; over the trees rises a white cloud.
A huge light grey building rise behind a flowerbed – Schwarze Pumpe Power Station. The pilot plant will be built here, and will be the seven-year-old power station’s nearest neighbour. Strömberg explains that the cloud that is rising from the cooling tower is harmless steam. He is more interested in talking about the flue gases from the boiler.
“As you can see, there is no chimney here. After the flue gases have been scrubbed, they are so clean that we could have discharged them at ground level”, says Strömberg.
QUOTAS IN THE ACCOUNTS
According to Strömberg, only one environmental problem remains at Vattenfall’s German coal-fired power stations: CO2 emissions. He explains that while generating energy from renewable sources is Vattenfall’s highest priority, renewable sources of energy have their limitations. For example, both Denmark and Germany will soon have reached the limits of the amount of wind-power an energy system can tolerate without also resulting in regulation problems, and Sweden, one of the world’s bio-energy giants already has to import 30% of the biofuel it needs to burn in its “green” boilers.
“And another thing”, says Strömberg as he locks the car. “In Central Europe there is no point in trying to ignore fossil fuels. There is no alternative to them down here”.
Strömberg, an expert in combustion, is one of Vattenfall management’s advisers on fuelpowered electricity generation, and is also a professor at Chalmers University of Technology in Göteborg. As we stretch our legs, he explains that gas-fired power stations have been the traditional alternative to coal in Central Europe, and that the price of gas is going to rise. It will follow the price of the liquified (and therefore more expensive) gas that Europe will soon be shipping to the USA. Vattenfall is aware that gas-fuelled electricity generation also produces CO2 emissions, and that the world’s coal reserves will last much longer than its oil or gas. That was why the company began to calculate the cost of CO2-free coalfired electricity generation.
Underlying its estimates was the technology for CO2 capture on which Vattenfall has been working for a long time. The CO2 quota trading system formed the backdrop to its calculations, and gave the answer: capture and storage of CO2 from coal-fired power stations would be competitive at a quota price of ¤20 per tonne of CO2. The cost of capture is estimated to be around NOK 130 per tonne, while the rest goes to transport and storage.
“We believed that the quota price would become sufficiently high in 2015, but it is already more than ¤20”, says Strömberg in the car park. The enormous aluminium façade of the building in front of us gleams in the sunlight. A large coal-fired power station that generates 2000 MW, with CO2 capture technology installed, would cost around 25 billion Swedish kronor. Strömberg knows well that no one hands out such sums of money on a whim.
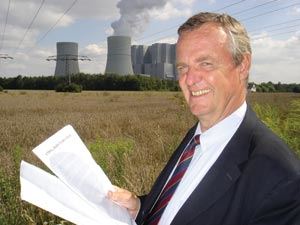
“If Central Europe wants to do anything about
its CO2 problem, dealing with CO2 emissions
from the electricity generating sector will be
essential”, says Lars Strömberg of Vattenfall..
Photo: Svein Tønseth, SINTEF Media
UNTESTED TECHNOLOGY
Vattenfall will use oxygen rather than air in the combustion process. This will leave only CO2 and steam in the flue gas mixture. The steam can easily be separated from the CO2 by cooling. This process has still to be tested on a large scale. And, as Strömberg points out, no one invests in a power station before they are sure that it will work.
This is why the company is building the pilot plant,which will be followed by a demonstration version designed to generate around 250 MW,which will take five years to build. This version will be used to optimise the technology. A commercial plant will not be ready until 2020.
In the pilot project, Vattenfall will have to be content to test the capture side of its CO2 concept. The company had hoped that a research team studying CO2 deposition in aqueous geological strata outside Berlin would store the greenhouse gasses generated by the Vattenfall pilot, but the timing was not right.
The pilot project will never be profitable, but making a profit was never the idea. “We are building the pilot plant in order to verify our calculations and to check that the combustion chemistry functions as we believe it will”, says Strömberg, as we walk towards the vestibule of the Schwarze Pumpe Power Station.
WANTS NORWAY TO GET OFF THE FENCE
In Norway, the concepts of pilot and demonstration plant have turned up again and again in the debate over gas-fired electricity generation and CO2 treatment. Fifteen hundred kilometres north of Schwarze Pumpe, in an office overlooking Trondheim’s Nidaros Cathedral, sits a Norwegian combustion expert who would like to have passed Norway’s own natural gas through environmentally friendly pilot and demonstration plants.
Nils Røkke coordinates SINTEF’s research on CO2 treatment. He is following developments in Schwarze Pumpe with admiration, but also in some despair. As long ago as 2003, Røkke proposed to make use of SINTEF’s research results in a pilot plant for CO2-free gas power. His initiative was aimed at the authorities, but it fell on deaf ears.
Anyone who wants to combine gas-fired electricity generation with CO2 treatment has three choices: the first is to separate the carbon from the gas as the first step, and then use what is left – hydrogen – as fuel in the power station. An alternative is to replace the combustion air with oxygen, as Vattenfall will do in its coal-fired stations. Finally, it is possible to scrub the CO2 out of the flue gases by using chemicals such as amines. Flue-gas scrubbing is currently regarded as the simplest method available , and this was Røkke’s choice of methodology. His preference was not well taken.
“My proposal was received with irritation in the oil and gas industry,which felt it was a step backwards to go in for a solution that was as little future-oriented as amine scrubbing”, remembers Røkke.
From Røkke’s perspective, the most important thing was to use the technology that is furthest developed, in spite of the fact that SINTEF itself is working on what could be the next generation of CO2-free technology, including membrane-based solutions. If if there is one thing he is certain of, it is that if society always waits for new technology before building the first pilot plant, nothing will ever happen.
“We would never have had today’s Mercedes cars if no one had built the Benz Patentenwagen in 1886”, says Røkke. But he admits that he has committed a political blunder.
ANOTHER NOKIA?
Røkke proposed publicsector financing of a flue-gas scrubbing system at a commercial gas-fired power station; a small 40 MW pilot plant for tests of an aminebased system. This would remove five percent of the flue-gases from a medium-sized gasfired power station.
“Five percent was a mistake”, says Røkke. “The politicians didn’t want to know about such a low clean-up rate”.
The following year Røkke announced that SINTEF had more ambitious plans for a fullscale amine-based 200 MW pilot plant. The SINTEF scientist is eager to enable Norwegian equipment suppliers to qualify for contracts for future green power stations by using a pilot plant as a training ground. He wants to see more value-added products in this country, based on Norway’s major research efforts in this area.
Røkke remembers what happened in the telecommunications world, when Europe chose technology from SINTEF and Telenor for the GSM system. Norway’s early lead did not give the country a mobile telephone industry, and jobs went to neighbouring countries. When reports of Vattenfall’s German plans first surfaced, Røkke dug out his overheads about SINTEF’s CO2 research. To one of them he added the following question: “Could this be another Nokia situation?”
“A MATTER OF URGENCY!”
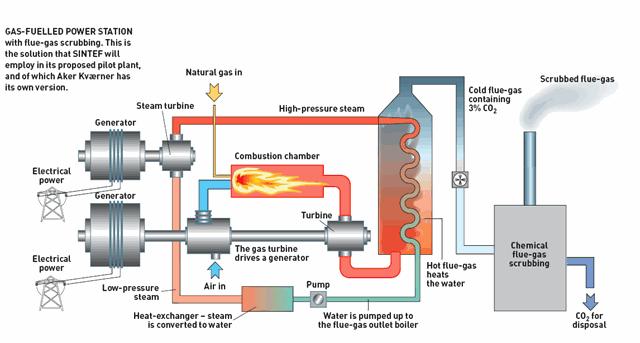
Illustration: Jan Helge Johansen, SINTEF Media
In 2004, SINTEF drew up a “CO2-free scenario” for Statoil. Its conclusion was that standard amine-based scrubbing with an extraction rate of 90% would cost around NOK 400 per tonne of CO2 removed from a gas-fired power station. The scientists included minimal downtime in their calculations. However, other Norwegian sources have come up with quite different cost estimates. Sargas, a small Norwegian technology company, hired in help from Siemens in Germany and formed an alliance with Hammerfest Energi in northern Norway. The company’s philosophy is that building now is essential for the environment and for the future development of the this field in Norway.
Sargas’s engineers realised that Siemens had turbines and that the UOP Group had scrubbing systems that would be suitable for what they were thinking of – a power station that could be built with proven components, with satisfactory lines of responsibility and guarantees.
“However, this would mean accepting for the time being a somewhat lower degree of generating efficiency than normal gas-fired power stations, but we will be able to raise the level of efficiency in time”, says Dr. Thor Christensen, of Sargas. He points out that plants in current operation reach somewhat higher levels of heat production as well as extremely efficient CO2 and NOx scrubbing.
Sargas would like to remove CO2 in a pressurized environment. Flue gases at high pressure and with high concentrations of CO2 need only a small CO2 scrubbing system. According to Christensen, this means scrubbing costs that are lower than current quota prices – not to mention the advantages involved in siting the plants, which are compact, as well as the possibility of employing them offshore, where discharge levels are high.
“We can enter the market quickly, which is an important factor. Our country has published a great deal in this field, so now we need to show the world that we are doing something. Other countries will follow us then”, says Christensen. A decision regarding investment has still to be taken. But if things go as Sargas and Hammerfest Energi hope, a large-scale pilot plant will be ready for use in Hammerfest, the most northerly city in the world, by early 2008.
ROCKET MOTOR IN JÆREN
In Hammerfest, most of the necessary infrastructure is already in place. According to the plans that have been drawn up, the power station will be supplied with natural gas from the Snøhvit field via the Melkøya terminal. The CO2 content of this gas is too high for it to be sold unscrubbed, so Statoil wishes to separate out the CO2 and inject it into a water-filled geological stratum on the continental shelf. The idea is that the gas -fired power station should use the same return pipeline for its own CO2.
In parallel with the plans being laid in the Arctic Ocean city, Lyse Energi, a Stavangerbased energy company, has been making its own plans for green power together with CO2 Norway, a consulting company in Kongsberg. These plans are based on technology from the American company Clean Energy Systems: turbines that generate electricity from a mixture of steam and CO2 in the same way as in a rocket motor. There is no steam boiler. Combustion takes place in a reactor that is supplied with gas, oxygen and water.
“We are still working on this. We have no definite plans in terms of milestones, but we know that we will be competitive”, says Jan Arve Øvestad of Lyse Energi.
In spite of all of these advances, it was actually one of Norway’s largest industrial companies that made the biggest headlines earlier this autumn.
FOCUS ON CUTTING COSTS
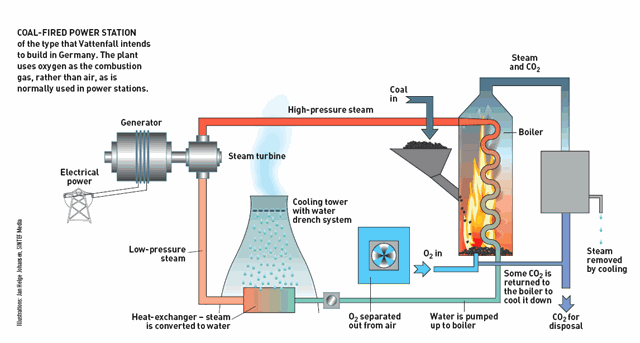
Illustration: Jan Helge Johansen, SINTEF Media
In September, Aker Kværner and the GassTEK organisation released a pilot study report. The aim of the study was to reduce construction and operating costs, explains Oscar Graff of Aker Kværner. The company has emphasised the importance of a solution that could be brought into use by 2010: an amine-based flue-gas scrubbing system that is independent of the design of the station and which can therefore be retrofitted.
The calculations assume a scrubbing efficiency of around 85 percent. In order to cut costs, the company has chosen simple solutions and alternative types of equipment. It has also dropped back-up systems for pumps, fans, etc., thus allowing for a certain amount of downtime. These compromises mean that their cost estimates for the scrubbing process are lower than SINTEF’s.
Graff points out that breaks in the operation of scrubbing systems are not critical, because electricity generation continues unabated. The report estimates the cost of scrubbing at NOK 184 per tonne CO2, with a margin of uncertainty of ±40%, as is normal in studies of this kind.
Aker Kværner and its most important partners are now starting a comprehensive development project based on the pilot study. The project has been designed as a two-year national programme with the aim of reducing the technical and commercial risks involved through detailed studies and physical tests.
“Our aim is to arrive at a cost estimate with an uncertainty of ±20%,which would be precise enough to enable most companies to make investment decisions”, says Graff.
Aker Kværner has been working on the development of various CO2 technologies for 15 years and has built a small-scale test plant at Kårstø near Bergen. Graff says that he agrees with SINTEF’s Nils Røkke: scrubbing CO2 from flue gas is the technology most likely to succeed in the near future.
At the end of summer there was more in the papers than there had been for a long time about the use of sequestered CO2 for enhanced oil recovery. But 2005 got off to a bad start for people who are interested in using CO2 to squeeze more oil out of our reservoirs.
CONFLICTING REPORTS
Last April, the Norwegian Petroleum Directorate published a report on the potential for use of CO2 offshore. “The conclusion is that CO2 does not appear to be a commercially viable alternative for enhanced oil recovery for licence-holders on the Norwegian continental shelf at present”, wrote the Directorate on its website. The Directorate continued: “CO2 injection is technically possible, and the potential for enhanced oil recovery is great. However, the threshold costs of establishing a supply chain for CO2 injection are so high that at present, other methods of enhanced recovery would appear to be more attractive for licence-owners”.
Late summer saw the appearance of a report from Bellona, a Norwegian environmental foundation, which claimed that the Petroleum Directorate was wrong. Viktor Jakobsen, a Bellona consultant, has said to Gemini that the Directorate employed two false premises. It assumed that a single oil field would bear the whole cost of capturing and transporting CO2. “It is quite obvious that this could not be economic”, says Jakobsen. According to Jakobsen, the Petroleum Directorate also assumed excessively high total CO2 capture costs.
The Bellona report emphasises that CO2 is a resource that offers us the opportunity to increase value creation on the shelf – a possibility that we will lose if we are unable to supply oil fields with CO2. Bellona points out that it is the state that earns most from enhanced oil recovery via taxes and its direct ownership of the shelf. Bellona therefore challenges the state itself to start up CO2 transport to the continental shelf. If the state pays a quota price of NOK 160 to emit one tonne of CO2, it loses NOK 700 in increased revenues from hydrocarbons. Jakobsen points out that without CO2 injection, the state will never benefit from this revenue.
In the report, two imaginary newly established companies are located between the emission source and the oil reservoir. One of them will operate the scrubbing plant. The other, a state-owned company, will buy CO2 from the scrubbing companies and sell it to the petroleum industry. This company will invest in transportation pipelines and shortterm storage facilities for CO2 in selected fields on the continental shelf.
The system would offer the owners of emission sources a reasonable and predictable way of getting rid of their emissions. Jakobsen emphasises that the most important thing is to get the CO2 out on the shelf. Where it comes from is actually of no interest. But to start with, Bellona would use the CO2 from the Norwegian gas-fired power stations currently being planned, plus a large new power station in south-western Norway, as well as from the process industry. The environmental foundation wants to export most of the gas power, but would also use CO2-free gas-fired power stations to supply continental shelf installations with electricity in order to reduce Norwegian CO2 emissions even further.
Just before the report went to press, exciting news came in from abroad.
GREEN GAS POWER IN SCOTLAND
BP and several of its partners wish to build a gas-fired power station with CO2 treatment in Scotland. The hydrocarbon gas will be split into its two components before use: the hydrogen will be fuel for the power station, while the carbon will be liberated in the form of CO2 and will be injected for enhanced oil recovery. A decision regarding investment will be made in 2006.
In Trondheim, the scientists are getting ever more impatientitchy. Because SINTEF still lacks flue gas from gas-fired power stations to practise on, Nils Røkke went to Svalbard,where he discussed an exciting idea with the Store Norske Kullkompagni. How about testing amine scrubbing on flue gases from the coal-fired power station in Longyearbyen?
“It would actually be possible to start work on Svalbard”, says Røkke.
“WELCOME TO MANHATTAN”
Lars Strömberg of Vattenfall, Røkke’s Swedish professional colleague, is focusing on the flue gases from the future pilot plant in Schwarze Pumpe. Outside the main power station we are met by a smiling female information officer. “Welcome to Manhattan”, she says in broken English, waving at the sky-high walls of the boiler-house.We are soon standing on the roof of the huge building, 175 metres above the ground.
To the east and north, Schwarze Pumpe’s two sister power stations break the line of the horizon. To the north-west we can see the opencast mine from which Vattenfall wins its brown coal. In front of me is a briquette factory and a hall for the production of gypsum,which is a by-product of the flue-gas scrubbing process. These factories stand on ground that is rich in industrial history. This is where the Nazis produced ersatz petrol from coal, to fuel Hitler’s vehicles during the Second World War. On the same site, the East German regime used the brown coal to produce gas for domestic use. Seventy percent of the gas used for heating and cooking in the DDR came from here. Now, industrial history will be married with new environmental technology.
“Down on the ground there, people have produced everything that can be made from brown coal”, says Strömberg. In 15 years, he and his colleagues will probably have reached the goals of their project, when we can hope that they will have demonstrated that it is both possible and profitable to deal with CO2 from power stations.
Perhaps generations to come will re-baptise the little village where it all started. What about calling it “Green Pump”?
By Svein Tønseth
The post A LITTLE PIECE OF SWEDEN appeared first on Geminiresearchnews.com.