Our technology options
Contact person
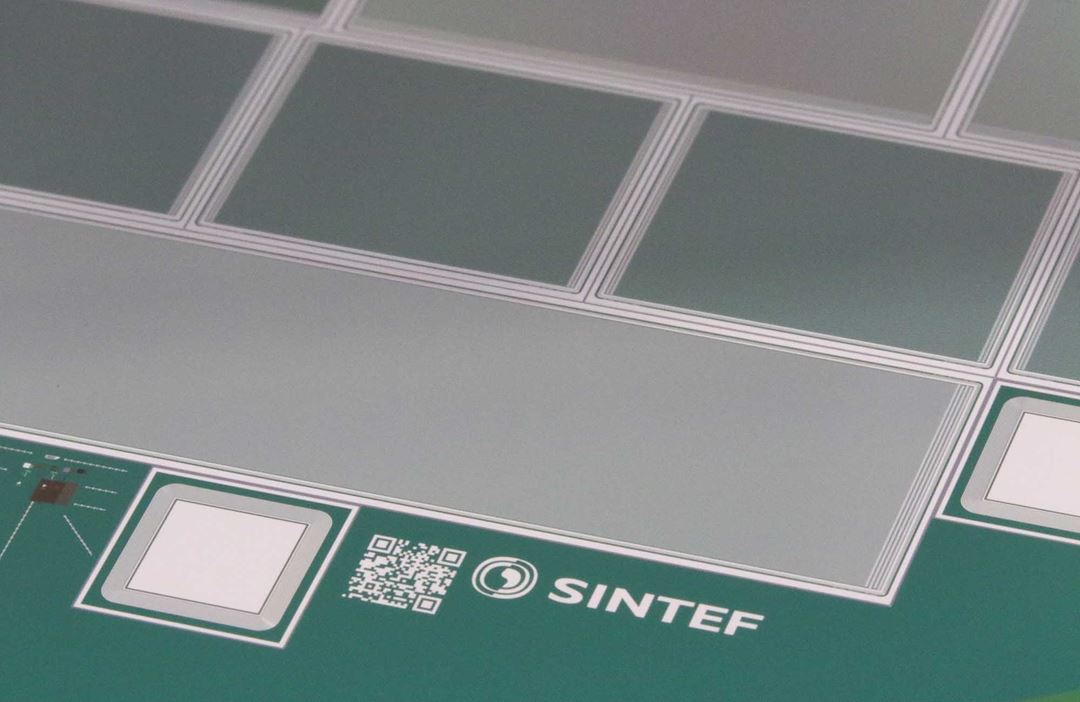
P-on-N technology
Our p-on-n technology is the most standard for silicon radiation sensors. This usually consists of implanted P+ electrodes into N-type silicon substrates and require 5 photolithographic layers. This technology is widely applied to microstrip and pixel sensors. The general design of a sensor usually consists of an advanced guard structure. The sensor guard ring structures serves the following purposes:
- Provide a sink for the current generated outside of the active
- Prevent avalanche breakdown by distribution the potential drop over a longer
- Improve the long-term stability by controlling the potential distribution at sensor surface
N-on-P & N-on-N technology
n-on-p technology where N+ electrodes are implanted onto P-type substrate is an alternative technology that provides readout for electrons and higher radiation tolerance. Like the N+ strips on N-type substrates (N-on-N) in double-sided strip detectors, the positive oxide charge induces a surface electron accumulation layer that may short-circuits the N-type implants. An isolation structure is needed to prevent shorting between pixels or strips. We usually apply either:
- P-stop: A well-defined area between N-type strips that is implanted with boron. The implanted area is defined by using photolithography, which provides masking during the boron implantation.
- P-spray: This is a low dose implantation of boron on the entire wafer surface where the N+ pixels or strips will be formed. This is usually done as the first step of the fabrication process of N-on-P sensors.
Double-sided technology
Our unique double-sided technology offers a high yield process for double-sided strip detectors and silicon drift diodes. All our equipment is carefully tuned and configured with edge-only handling to ensure the highest quality, even for sensors up to 2 mm or down to 10 µm thick.
Double metal layers
By using a 5 m thick polymide layer as a dielectric, sensors are made with a second aluminium layer. This layer can be used to route metal lines from pixels to bonding pads at the end of the sensors as an alternative to flip-chip bonding. It is also used for double sided sensors with orthogonal strips where the bonding pads to the readout electronics should be along the same edge for both sensor sides.
Biasing methods
Microstrip sensors can be biased with integrated polysilicon resistors or with FOXFET structures. High resistance bias resistors for low noise readout are made from polycrystalline silicon deposited by Low Pressure Chemical Vapour Deposition, followed by boron implantation. The resistance can be customised to a fixed value between 0.1 and 50 MΩ by adjusting the implantation doses and the length of the resistor. This technology has superior radiation hardness since the resistors have high tolerance against radiation exposure.
FOXFET biasing is an alternative biasing for AC coupled detectors that offers reduced fabrication cost and high dynamic resistance values. The low-cost process is compromised by the lower radiation tolerance when compared to the polysilicon resistor approach.
Shallow entrance window
Passivation layers, metal layers and highly doped regions will absorb radiation without contributing to the electrical signal. It is essential that such dead layers are minimized to detect radiation with a short penetration depth in silicon. Conventional standard p-n junction sensors, usually have a doping depth of around 1 µm on the doped window for incident radiation. While this type of sensors is more than sufficient for a lot of applications, our latest technology can offer a much shallower entrance window down to 0.1 µm for both p-type and n-type doped windows, providing much higher sensitivity for soft X-rays and low energy electrons and protons. We will also tailor all other layers such as passivation and metal layers to meet your application needs.