- Name
- Armin Hafner
- Title
- Professor
- Organization
- NTNU
Components RA2
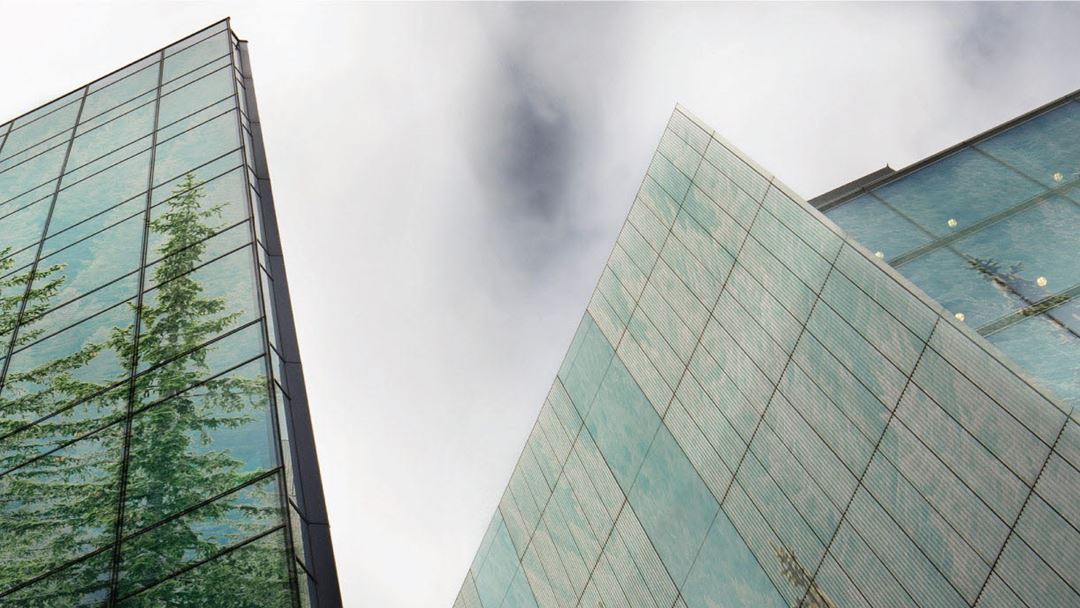
The primary goal of the RA2 team, in close cooperation with other RAs, was to develop cost-effective components for efficient heat pumping and conversion systems, focusing on heat exchangers, compressors, and expansion work recovery. To achieve this, we created design methods and tools, emphasising cycles with natural working fluid mixtures, thermodynamic properties, system optimisation, and experimental research. Additionally, we designed, supported the integration of, and maintained flexible test facilities for the HighEFFLab infrastructure at NTNU and SINTEF.
Final results
Heat exchangers development achievements
During HighEFF’s eight-year period, models and methods were developed to optimise heat exchanger geometry and processes simultaneously. The methodology, grounded in physical descriptions and geometry-dependent models, was enhanced by Computational Fluid Dynamics (CFD) to extend analysis beyond laboratory measurements.
Key achievements include:
- Establishing a link between optimisation models and CFD for validation, culminating in studies comparing CFD, experimental data, and optimisation models using tube-in-fin heat exchangers.
- Validating the CFD model with experimental data on heat recovery exchangers for offshore power cycles and metal processing units. This included examining the geometry effects.
- Conducting several case studies illustrating how design model selection affects weight (cost) optimisation in heat recovery exchangers.
Several publications have been disseminated, evaluating compact designs using optimised geometry variables with CFD analysis.
Achievements in compressor and expansion work recovery development
In the early phase of HighEFF, Multi-ejector expansion modules were designed and experimentally investigated. Results showed that four ejector geometries perform their vapour compression duties efficiently within the assumed range of operating conditions and achieved the highest ever recorded values of ejector efficiency, up to 36.8%. These multi-ejectors are nowadays applied in many CO₂ refrigeration and heat pumping systems.
A three-dimensional dynamic ring plate valve model was developed for reciprocating compressors, as applied in refrigeration, heat pump and High Temperature Heat Pump (HTHP) applications. The model investigates the three-dimensional dynamics of the ring plate discharge valve, using loosely coupled computational fluid dynamics (CFD) and finite element method (FEM).
The hydrocarbon based HTHP test facility has been utilised during the entire HighEFF period. Heat sink outlet temperature of 120 °C have be demonstrated, while producing ice-water on the cold side. The butane compressor from DORIN has been though several design intervals and is distributed to several successful industrial demonstration units alongside with HighEFF.
Natural working fluids accomplishments
The HighEFFLab Heat Exchanger test facility was used for industrial projects, and prepared for testing heat exchanger units with propane condensed on one side while butane is evaporated on the other side of a cascade heat exchanger. The results will be used to develop and validate a detailed model of such cascade heat exchangers needed in HTHPs.
In cooperation with our Japanese colleagues, a refrigeration system capable of heat absorption below -56˚C has been developed, addressing the challenge of CO₂'s equilibrium between dry ice and gas at such temperatures. A tapered evaporator/sublimator with a swirl promoter was designed to induce a swirling two-phase flow of dry ice and gas, preventing blockages and enhancing heat transfer. Tests demonstrated stable, continuous system operation, with the swirl promoter ensuring uniform dry ice particle distribution along the evaporator walls. This confirms the concept's effectiveness for ultra-low temperature refrigeration.
Exploitation of RA2 results
The five PhD’s related to the research area, supporting the education of 15 master’s candidates, together with the team of research- and industrial partners, moved several ideas from a low TRL level towards applicable technology. All of them joined companies or institutions in Norway after graduation.
Collaboration both within the Centre and with external partners enabled the development of innovative energy-efficient systems, described in other research areas, with key components developed within RA2.
2023 Results
Heat exchangers
CFD model
In WP2.1, the team develops models and methodology to study the simultaneous effects of process and heat exchanger geometry optimisation. The methodology depends on the underlying physical descriptions being valid over the operating range, and on the models including the effects of all the geometry parameters subjected to optimisation. The underlying models are developed by laboratory measurements, but to be able to "measure" over a wider range of geometries, these can be supplemented with Computational Fluid Dynamics (CFD). Previously, the team established a link between the optimisation models and a CFD model, so that we can numerically verify the result. This led to a paper where we compared CFD results with literature data from experiments, and with results from the developed heat exchanger optimisation model using a traditional tube-in-fin heat exchanger as case. This work continued in 2022 in combination with a NTNU master's student's work. The work in 2022 validated the CFD model against experimental data on heat-recovery heat exchangers relevant for offshore power bottoming cycles. Effects of geometry parameters were studied. In 2023, a case study was conducted that illustrates how the choice of design models impacts minimum weight when optimising a heat recovery heat exchanger (OTSG).

The illustration above shows that when optimising a number of free geometry variables for a finned tube bundle, the choice of models will have a significant impact on the result. The optimised design is analysed with the CFD model in order to evaluate which model is suitable for a compact design. This work continues and will be published in 2024.
Plate Heat Exchanger measurements at HighEFF Lab:
Experiments for evaporation of hydrocarbon and hydrocarbon mixtures at 15 – 25 bar were done in the HighEFFLab heat exchanger test facility. The HighEFF test rig performed well with obtaining stable conditions and good agreement on the heat balance. High pressure loss on the Hydrocarbon side was measured due to an inlet flow restriction. For this same reason, the planned condensation experiments at the same pressures were not possible.
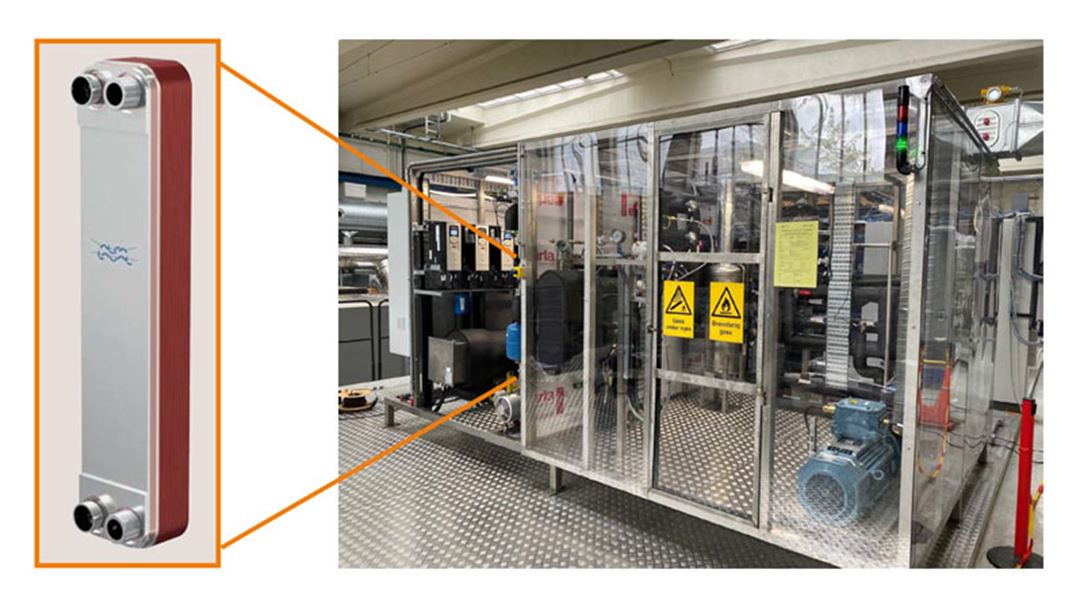
Work Recovery & Compressors
The R&D focus is directed at compressors and technologies for expansion work recovery. The application of environmentally friendly and future-proof natural refrigerants is a novelty of the research conducted by FME HighEFF. While the experimental investigation on the compressors was delayed due to Covid-19, the modelling achieved a major step forward.
Compressors
New compressors are under development that have an extended operation envelope e.g.: towards higher temperatures. These compressors are paving the way for compact and reliable industrial high-temperature heat pumps (HTHP) as applied in WP 3.2 (HTHP, Cooling and Drying) and used as input to RA6 Case Studies. HTHP’s delivering process heat up to 200°C can utilise renewable energy and may cover up to 37% of all industrial need for process heat.
The spin-off project IPN-SkaleUP, with Dorin, TINE, Cadio and SINTEF Energy Research joined forces with Skala Fabrikk. An industrial 300 kWth High Temperature Heat Pump was successfully installed and tested at TINE Tunga, in Trondheim, in 2021. The HTHP was operated until June 2022. The compressors have been sent for inspection and there are plans for further tests in 2024. The analysis on both the R290- and R600 compressor efficiencies were carried out and are comparable to the lab scale 30 kWh system installed at HighEFFLab. The total efficiency, combining isentropic and motor efficiency, are in the range from 0.65 to 0.78 at pressure ratios of 2.5 to 7. These are slightly elevated values for industrial scale compressors, mainly caused by thermal losses. Volumetric efficiencies are comparable as well, decreasing from values of about 0.85 to 0.66, when the pressure ratios increase from 2.5 to 7.
A newly designed and implemented ammonia compressor test facility was established within HighEFFLab. The test facility was commissioned in Q2 2023 and will be able to operate compressors with an electric power of up to 150 kW and suction flow rates of up to 330 m³/h.
Motion modelling in piston compressor valves has been further developed through a novel method coupling computational fluid dynamics (CFD) and finite element method (FEM). The model accounts for the complex physics of the reciprocating compressor. It was demonstrated that it is necessary to consider the particular aspects of the flow inside the cylinder head as it exits through the discharge valve. Using a typical inlet boundary condition to the valve cage cannot capture the full physics of the flow. Employing a full model of the cylinder space captures in detail the reversed flow that occurs when the piston passes top dead centre, which leads to a more rapid closing of the valve. This modelling enables investigation of the volumetric efficiency. The coupled simulation has also shown that the effect of pressure inhomogeneity in the flow field leads to a significant rotation of the valve ring, due to the gas damping effect and the mechanical impacts that occur subsequently, giving a lower maximum lift in terms of centre-of-mass.
Expansion work recovery
The HighEFF lab test rig "EXPAND" arrived in Q1 2022 in Trondheim. Due to unsolved challenges identified during commissioning, major components were sent back to the manufacturer, and have not been returned during 2023. The setup is dimensioned to provide experimental data of turbines/expanders in the 10-100 kW range using natural working media.
Natural Working Fluids
The HighEFFLab Heat Exchanger test rig was installed and connected to local infrastructure at NTNU and SINTEF's thermal laboratories at Gløshaugen, during the spring of 2021. In 2022, the facility was operated mainly for an industrial project. In 2023, finally, preparations were carried out for tests with propane (R290) condensed on one side while butane (R600) is evaporated on the other side of a cascade heat exchanger. The results will be used to develop and validate a detailed model of such cascade heat exchangers to be used as a design and optimisation tool.
2022 Results
CFD model
In WP2.1, the team develops models and methodology to study the simultaneous effects of process and heat exchanger geometry optimisation. The methodology depends on the underlying physical descriptions being valid over the operating range and on the models including the effects of all the geometry parameters subjected to optimisation. The underlying models are developed by laboratory measurements, but to be able to "measure" over a wider range of geometries, these can be supplemented with Computational Fluid Dynamics (CFD). Previously, the team established a link between the optimisation models and a CFD model, so that we can numerically verify the result. This led to a paper where we compared CFD results with literature data from experiments, and with results from the developed heat exchanger optimisation model using a traditional tube-in-fin heat exchanger as case. This work continued in 2022 in combination with a NTNU master's student's work. The work in 2022 validated the CFD model against experimental data on heat-recovery heat exchangers relevant for offshore power bottoming cycles and effects of geometry parameters were studied. This work also developed a direct link between the optimisation tool and the CFD model.
Work Recovery & Compressors
The R&D focus is tuned towards compressors and technologies for expansion work recovery. The application of environmentally friendly and future-proof natural refrigerants is a novelty of the research conducted by FME HighEFF. While the experimental investigation on the compressors was delayed due to Covid-19, the modelling achieved a major step.
Compressors
New compressors are under development that have an extended operation envelope e.g.: towards higher temperatures. These compressors are paving the way for compact and reliable industrial high-temperature heat pumps (HTHP) as applied in WP 3.2 (HTHP, Cooling and Drying) and used as input to RA6 Case Studies. HTHP’s delivering process heat up to 200°C can utilise renewable energy and may cover up to 37% of all industrial process heat.
The spin-off project IPN-SkaleUP, with Dorin, TINE, Cadio and SINTEF Energy Research joined forces with Skala Fabrikk. An industrial 300 kWth High Temperature Heat Pump and successfully installed and tested (HTHP) at TINE Tunga, in Trondheim, in 2021. The HTHP was operated until June 2022. The compressors have been sent for inspection and will be installed again Q2 in 2023. The analysis on both the R290- and R600 compressor efficiencies were carried out and are comparable to the lab scale 30 kWth system installed at HighEFFLab. The total efficiency, combining isentropic and motor efficiency, are in the range from 0.65 to 0.78 at pressure ratios of 2.5 to 7. These are slightly elevated values for industrial scale compressors, mainly caused by thermal losses. Volumetric efficiencies are comparable as well, decreasing from values of about 0.85 to 0.66, when the pressure ratios increase from 2.5 to 7.
A newly designed and implemented ammonia compressor test facility was established within HighEFFLab. The test facility will be commissioned in Q2 2023 and will be able to operate compressors with an electric power of up to 150 kWel and suction flow rates up to 330 m3/h.
Motion modelling in piston compressors further developed a novel method coupling computational fluid dynamics (CFD) and finite element method (FEM). The model accounts for the complex physics of the reciprocating compressor. It was demonstrated that it is necessary to consider the particular aspects of the flow inside the cylinder as it exits through the valve. Using a typical inlet boundary condition to the valve cage cannot capture the full physics of the flow. Employing a full model of the cylinder space captures in detail the reversed flow that occurs when the piston passes top dead centre, which leads to a more rapid closing of the valve. This modelling enables investigation of the volumetric efficiency. The coupled simulation has also shown that the effect of pressure inhomogeneity in the flow field leads to a significant rotation of the valve ring, due to the gas damping effect and the mechanical impacts that occur subsequently, giving a lower maximum lift in terms of centre-of-mass.
Expansion work recovery
The HighEFF lab test rig "EXPAND" arrived in Q1 2022 in Trondheim. Due to some challenges identified during commissioning, major components have been returned to the manufacturer. Therefore, the experiments to verify the operation envelope are planned in Q3 2023. The setup is dimensioned to provide experimental data of turbines/expanders in the 10-100 kW range using natural working media.
Natural working fluids
The HighEFFLab Heat Exchanger test rig was installed and connected to local infrastructure at NTNU and SINTEF's thermal laboratories at Gløshaugen, during the spring of 2021. In 2022, the facility was operated mainly for an industrial project. In 2023, finally, propane (R290) will be condensed on one side while butane (R600) is evaporated on the other side of a cascade heat exchanger. The results will be used to develop and validate a detailed model of such cascade heat exchangers to be used as a design and optimisation tool.
2021 Results
Heat Exchangers
VARGEO
In order to realise useful heat recovery from off-gas cooling, it is important to get the size of the large heat recovery heat exchanger (HRHE) to an acceptable level. Another issue is that the off -gas contains particles.
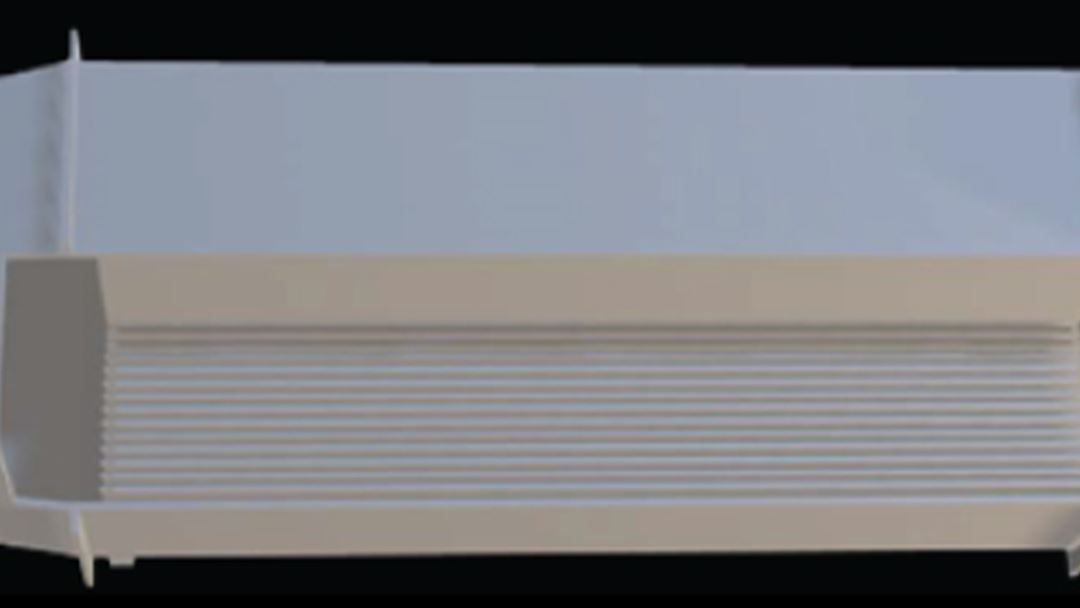
The target is to design a heat exchanger that will have low velocities at the inlet, to avoid particles entering further into the heat exchanger – but for good heat transfer properties, the gas should accelerate once inside.
In 2020, we studied such a HRHE by extending the general heat exchanger modelling framework to create a simulation model that allows the geometry to be adapted to the changes in the off-gas conditions.
In 2021 the variable geometry model was extended to have a continuous change of flow area on the hot and cold side represented by a smooth curve In addition, the shape of the curve was added into an optimisation framework so that such a heat exchanger could be designed for minimum weight given an allowable off- gas pressure loss and required duty.
CFD MODEL
Much of the work in WP2 1 is to develop models and methodology to study the simultaneous effects of process and heat exchanger geometry optimisation. The methodology depends on the underlying physical descriptions being valid over the operating range and on the models including the effects of all the geometry parameters subjected to optimisation. The underlying models are developed by laboratory measurements, but to be able to "measure" over a wider range of geometries these can be supplemented with Computational Fluid Dynamics (CFD) In 2020, we have established a link between the optimisation models and a CFD model, so that we can numerically verify the result. This led to a paper where we compared CFD results with literature data from experiments, and with results from the developed heat exchanger optimisation model using a traditional tube-in-fi n heat exchanger as case. This work continued in 2021 in combination with a NTNU master's student's work.
Work Recovery & Compressors
The R&D focus is tuned towards compressors and technologies for expansion work recovery The application of environmentally friendly and future proof natural refrigerants is a novelty of the research conducted by FME HighEFF While the experimental investigation on the compressors was delayed due to Covid-19, the modelling achieved a major step
COMPRESSORS
New compressors are under development that have an extended operation envelope e g: towards higher temperatures. These compressors are paving the way for compact and reliable industrial high-temperature heat pumps (HTHP) as applied in WP 3 2 (HTHP, Cooling and Drying). HTHP’s delivering process heat up to 200°C will work with renewable energy and may cover up to 37% of all industrial process heat.
A 3-dimensional dynamic ring plate valve model for reciprocating compressors, as applied in refrigeration, heat pump and HTHP applications, was developed. The model investigates the three-dimensional dynamics of the ring plate discharge valve, using loosely coupled computational fluid dynamics (CFD) and fi nite element method (FEM). The model was further compared
to measurement results giving an insight into key elements of the compressor valve dynamics. The dynamic motion of the valve ring is controlled by the combined actions of forces resulting from applied pressure, spring reaction, impact with the valve's plate and cage, and damping effects. Examining these phenomena in greater depth will allow to understand the wearing of the valve and enable the compressor manufacturers to build more efficient and reliable compressors.
EXPANSION WORK RECOVERY
The implementation of ejectors for expansion work recovery enables increased efficiency and makes environmentally friendly refrigeration systems more competitive. Investigations of the real system performance of an ejector-supported supermarket refrigeration system have been performed 3 months of various system operation modes were analysed, concluding with an energy saving potential of about 10% when using the ejector technology in a real supermarket. Further improvements were identified, which have to do with heat recovery of the CO₂-based refrigeration system. The largest benefits of the investigated systems are seen in warmer climates, such as southern Europe or India.
Natural Working Fluids
Ehsan Allymehr fi nished his PhD work performed at NTNU with HighEFF funding (see page 7). The HighEFFLab Heat Exchanger test rig was installed and connected to local infrastructure in NTNU and SINTEFs thermal laboratories at Gløshaugen during the spring of 2021. Shake-down testing was performed and by the end of the year the rig was tested with both propane and a propane/ethane mixture. The rig is now operational and the first heat exchanger test campaign has started. The rig can be used to test novel heat exchangers and hydrocarbon working fluids Both heating, evaporation, cooling and condensing of hydrocarbons against water or water/ glycol can be performed. Plans have been made to use the rig in 2022 to investigate a cascade heat exchanger used in high temperature heat pumps. For these tests, propane (R290) will be condensed on one side while butane (R600) is evaporated on the other side in the heat exchanger. The results will be used to develop and validate a detailed model of such cascade heat exchangers to be used as a design and optimisation tool.
2020 Results
RA2.1 Heat Exchangers
VARGEO
In order to realise useful heat recovery from off-gas cooling, it is important to get the size of the large heat recovery heat exchanger (HRHE) to an acceptable level. Another issue is that the off-gas contains particles. The target is to design a heat exchanger that will have low velocities at the inlet, to avoid particles entering further into the heat exchanger – but for good heat transfer properties, the gas should accelerate once inside.
In 2020, we worked in collaboration with WP4.2 (Surplus heat recovery) in HighEFF, which has given us the opportunity to study such a HRHE by extending the general heat exchanger modelling framework to create a simulation model that allows the geometry to be adapted to the changes in the off-gas conditions. Research on how to obtain the optimal variable geometry will continue in 2021.
CFD MODEL
Much of the work in WP2.1 is to develop models and methodology to study the simultaneous effects of process and heat exchanger geometry optimisation. The methodology depends on the underlying physical descriptions being valid over the operating range and on the models including the effects of all the geometry parameters subjected to optimisation. The underlying models are developed by laboratory measurements, but to be able to "measure" over a wider range of geometries these can be supplemented with Computational Fluid Dynamics (CFD). In 2020, we established a link between the optimisation models and a CFD model, so that we can numerically verify the result. This led to a paper where we compared CFD results with literature data from experiments, and with results from the developed heat exchanger optimisation model using a traditional tube-in-fin heat exchanger as case.
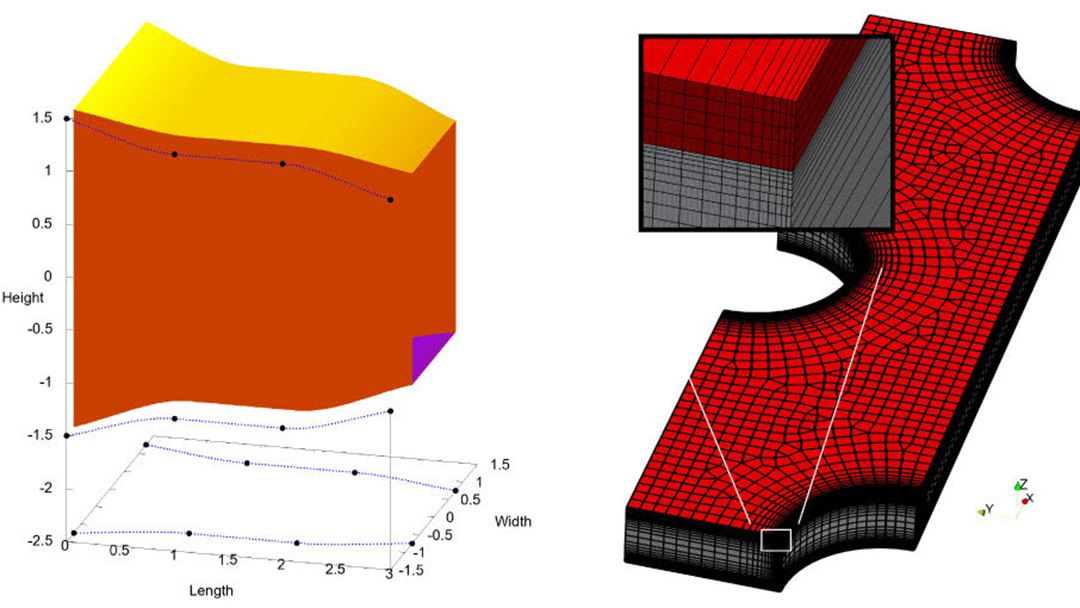
RA 2.2 Work Recovery & Compressors
The R&D focus is tuned towards compressors and technologies for expansion work recovery. The application of environmentally friendly and future proof natural refrigerants is a novelty of the research conducted by FME HighEFF. While the experimental method investigation on the compressors was delayed due to covid-19, the modelling achieved a major step.
COMPRESSORS
New compressors are under development having an extended operation envelope e.g.: towards higher temperatures. These compressors are paving the way for compact and reliable industrial high temperature heat pumps (HTHP) as applied in WP 3.2 (HTHP, Cooling and Drying). HTHP’s delivering process heat up to 200°C will work with renewable energy and may cover up to 37% of all industrial process heat.
In WP 2.2 (Work Recovery & Compressors), a 3-dimensional dynamic ring plate valve model for reciprocating compressors, as applied in refrigeration, heat pump and HTHP applications, was developed. The model investigates the three-dimensional dynamics of the ring plate discharge valve, using loosely coupled computational fluid dynamics (CFD) and finite element element method (FEM). The model was further compared to measurement results giving an insight into key elements of the compressor valve dynamics. The dynamic motion of the valve ring is controlled by the combined actions of forces resulting from applied pressure, spring reaction, impact with the valve's plate and cage, and damping eff ects. Future studies of these phenomena in greater depth will allow to understand the wearing of the valve and enable the compressor manufacturers to build more efficient and reliable compressors.
EXPANSION WORK RECOVERY
The implementation of ejectors for expansion work recovery allows to increase efficiency and make environmentally friendly refrigeration systems more competitive. Investigations of the real system performance of an ejector-supported supermarket refrigeration system have been performed. 3 months of various system operation modes were analysed, concluding with an energy saving potential of about 10% when utilising the ejector technology in a real supermarket. Further improvements were identified, which have to do with heat recovery of the CO2 based refrigeration system. The largest benefits of the investigated sytems are seen in warmer climates, such as southern Europe or India.
Natural Working Fluids
Hydrocarbons as a 4th generation of working fluids has the capability to be utilised in many different applications, but in order to do so, hydrocarbon charge needs to be minimised to ensure safety. Internally enhanced tubes offer a possible solution, wherein the reduced volume minimises the charge. The critical design parameters such as pressure drop and heat transfer coefficient are unknown in these conditions. Experimental tests were performed at NTNU to measure these values in smooth and internally enhanced tubes. The results provide reliable prediction methods for design of heat exchangers. In the next steps, these predictive methods will be used for designing a heat exchanger in a predefined system.
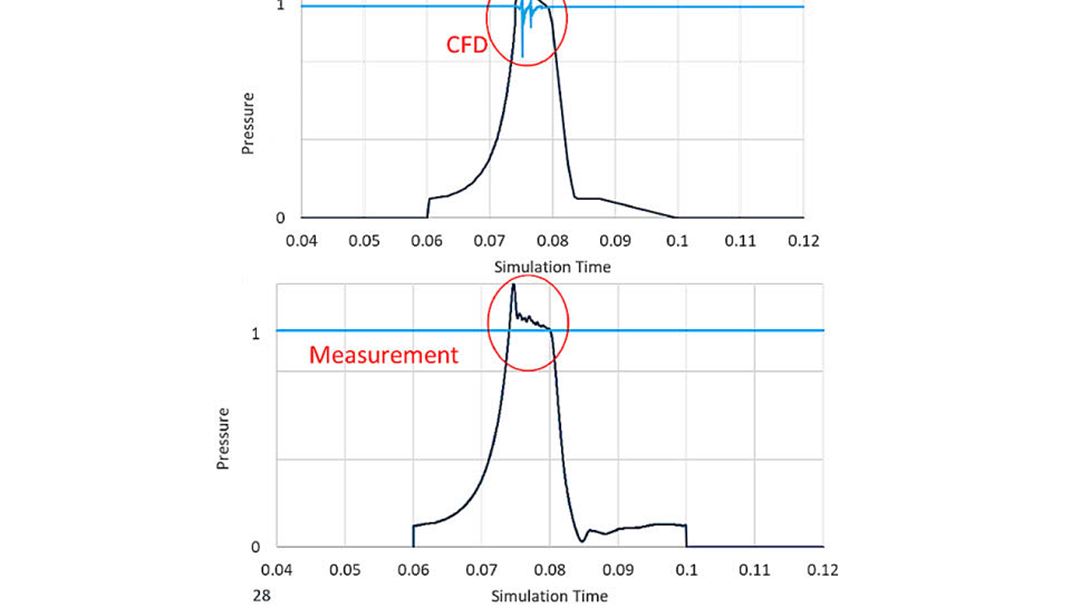
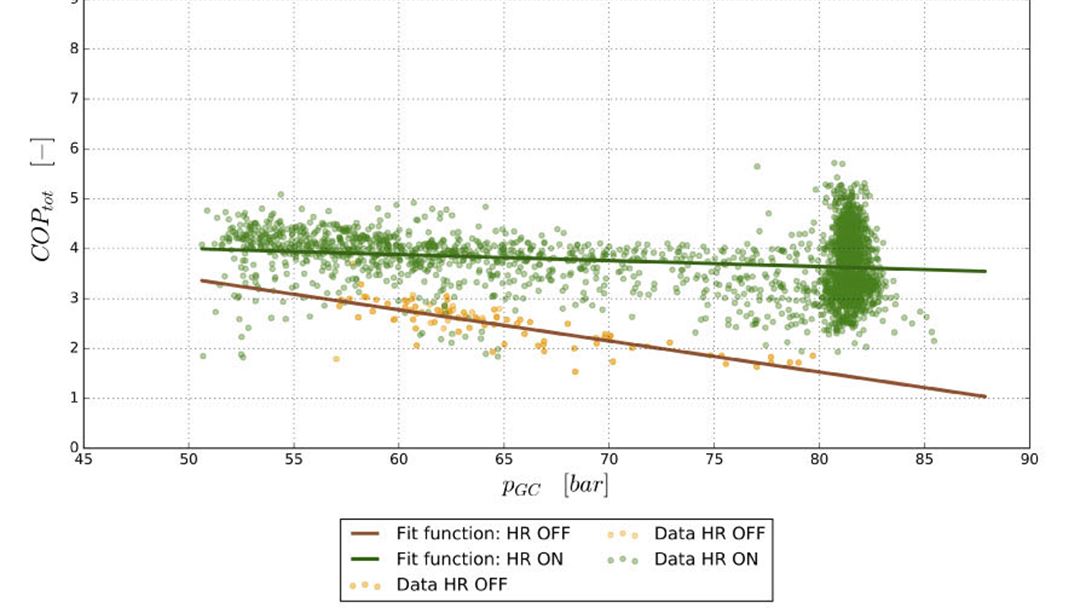
2019 Results
Dry ice sublimation
We are developing a refrigeration system with heat absorption below –56˚C. The challenge is that CO2 exists in an equilibrium between dry ice and gas at temperatures below -56 ˚C. Thus, in order to realize a refrigeration system with heat absorption below this temperature, one needs to develop a heat exchanger concept that enables sublimation of dry ice and to understand the phenomena related to this.
A tapered evaporator/sublimator with a swirl promoter, which induces a swirling flow of solid (dry ice)-gas two-phase flow, was designed and constructed and installed into a CO2 ultra-low temperature cascade refrigeration system. By means of the heat transfer of solid (dry ice) -gas two-phase flow is investigated. Based on the measurement of heat transfer characteristics, it was verified that the CO2 refrigeration system can operate continuously and stably without dry ice blockage in the evaporator/ sublimator. It was understood that dry ice particles are uniformly distributed along the inner wall of the evaporator/sublimator by installing the swirl promoter, where the heat transfer coefficient is largely improved.
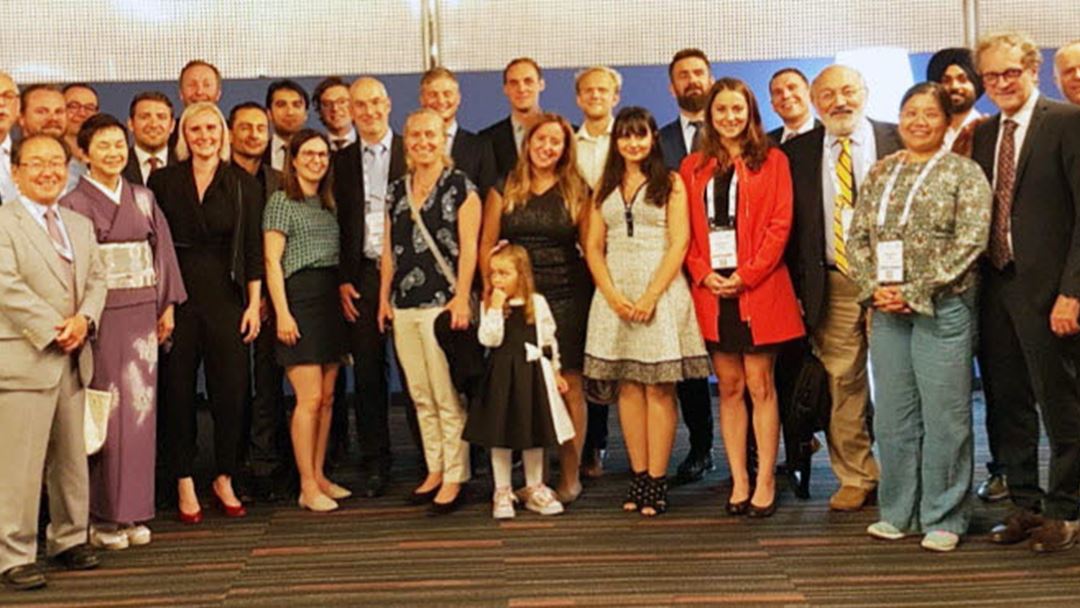
LT-Compressor replacement ejector
Decreasing the complexity of R744 commercial refrigeration systems for supermarkets could substantially reduce their cost, promoting worldwide spreading. Typically, the share of the low-temperature (LT) load in the total load for supermarkets is low. Nevertheless, significant investments must be made to cover the LT demand, including dedicated compressors, inverter, desuperheater, and oil management equipment.
A new concept development based on high-pressure lift ejector to support LT evaporators reduces the system cost by replacing the whole LT compressor section with a fixed geometry ejector. In addition, elimination of the compressor(s) allows overfeeding operation of LT evaporators.
Propane evaporation in smooth and microfinned tubes
Utilize and adapt an in-house heat transfer test facility (inside small diameter tubes) to perform experimental investigations with hydrocarbons and mixtures. Experimental campaigns for maintaining and adapting specially designed in-house tools, for analysing and developing correlations for hydrocarbons and their mixtures.
A new test section has been developed in order to measure the heat transfer coefficient and pressure drop of hydrocarbons in small diameter tubes. Following a study of different methods, a model was analysed and then a prototype built. The preliminary tests were positive and will be the basis for the final test section.
Humid gas
The work on humid gas in 2019 includes the modelling of two heat transfer scenarios using the thermo- dynamic model for humid gas implemented in 2018. The first scenario is to simulate the heat transfer of humid gas on a cold flat plate, where the calculation of heat transfer is based on the traditional method for dehumidification process. The second scenario is to simulate a tube-intube heat exchanger with humid gas flowing in the inner tube and cooling water flowing in the annulus. The method treats the humid gas as normal mixtures and uses the thermodynamic libraries for mixtures.
It requires further validation of the results based on experimental data, which is not available at present. Regarding the future work on modelling, it is suggested to find a suitable case relevant to the practical applications, such as the flue gases containing Sulphur components. The differences between using the dehumidification method and method of general mixtures should be further investigated.
2018 results
Heat Exchangers
The work related to heat exchanger (HX) for cold thermal energy storage (CTES), applicable for display cabinets in supermarkets continues, with focus on increased performance of display cabinets and power peak shaving. Experience has been gained on how the derivative free optimisation framework NOMAD can be implemented for process and HX optimisation. For simple Rankine cycles the gradient based method was compared to NOMAD in terms of time consumption and robustness.
The work on 3D-printing continues to streamline the process from HX geometry optimisation, on-screen visualization, 3D-editing and finally 3D-printing. The main outcome was a visualization scripting with Python toward Paraview, a well-known visualization toolkit for CFD.
HighEFF Lab – Heat Exchanger Laboratory was designed. The two test rigs cover: HX prototype test rig up to 40 kWth and a small-scale heat transfer coefficient and pressure drop test rig.
Work recovery & Compressors
Design and testing of Multi-ejector expansion modules continue. These devices are substituting standard high-pressure electronic expansion valves in refrigeration systems.
Two expansion devices designed for R744 (CO2) refrigeration systems (capillary tube and fixed geometry ejector) were experimentally tested to determine performance in different ambient conditions. Tests and numerical investigations concluded that ambient conditions did not significantly affect the operation of the capillary tube and the R744 ejector.
Three approaches to perform modelling of piston compressor processes have been developed: 1D model; 3D CFD model; and 3D FEM impact model. These modelling approached give complementary insights into the piston compressor processes and how to optimize compressors for increased efficiency and reliability. A measurement campaign has been performed with the prototype compressor for butane. The prototype compressor shows high isentropic efficiencies in the order to 0.70 to 0.78, nearly constant over pressure ratio investigated. The volumetric efficiency declined from 0.89 to 0.75 with increasing pressure ratios.
Natural Working fluids
The investigations on hydrocarbon heat transfer and pressured drop in small pipes continues. Calibration was done against correlation for single phase flow in vapor form; a 5.6 % deviation for the pressure drop; 1.6 % for heat transfer coefficient. For fluid visualization, a high speed camera will be installed in 2019.
A library for general humid gas "hglib" was built based on "hxlib" library. hglib is connected to THERMOPACK, enabling to calculate humid gas as real gas. The EOS, e.g. PR, EOCGC, GERG2008 have been tested with the reference result by hxlib at low pressure, and EOCGC, GERG2008 perform well. Available methods for calculating the viscosity of a hydrocarbon mixture at high pressures and temperatures were investigated. A sufficiently general correlation is difficult. The TRAPP method is quite accurate but tends to overpredict the viscosity. The CS2 model has a similar accuracy, but underpredicts the results. For both models the density calculations needs to be as accurate as possible. Refprop results are generally better than TRAPP and CS2 with some exception
2017 Results
Heat Exchangers:
A heat exchanger for cold thermal energy storage (CTES), applicable for display cabinets in supermarkets, has been developed and implemented into a dedicated CO2 laboratory refrigeration cycle. The CTES will increase the performance of display cabinets and enable power peak shaving.
A new laboratory rig, financed by the infrastructure project HighEFFlab, for testing of heat exchangers used in low temperature heat to power applications is under planning. A pinch point analysis of relevant hydrocarbon working fluids with low ODP and GWP has been performed to investigate which working fluids are the most interesting for testing in the laboratory rig and the optimal operating conditions for these.
Work recovery & Compressors:
Design and testing of Multi-ejector expansion modules, intended as a substitute for standard high-pressure electronic expansion valves, for performance mapping of four ejector cartridges is completed. Results shows that four ejector geometries perform their vapour compression duties efficiently within the assumed range of operating conditions, offering the highest ever recorded values of ejector efficiency up to 36.8%. the liquid compression reduces the effectiveness significantly, where the highest recorded recovery values of ejector efficiency were equal to 12.6%.
The propane - butane High Temperature Heat Pump test facility has been installed successfully and delivering heat sink outlet temperature of 116 °C. The R600 compressor from DORIN is functioning within expectation with a total compressor efficiency of 71%.
Natural Working fluids:
In the evaporator/sublimator process of CO2 (R744) ultra-low temperature cascade heat pump system, it is known, as a problem, that dry-ice blockage makes the system operation fail. The design of an expanding channel for the evaporation/sublimation process is one solution to solve the problem. In order to give better understanding to heat transfer process in the refrigeration system, particular attention is focused for CO2 dry-ice solid-gas two-phase flow to obtain the effectivity of heat transfer and to verify the flow-phenomena where a visualization test apparatus is placed horizontally. Development of a mathematical model for baseline and the enhanced systems for the next generation of refrigeration systems for chilling of fish in fishing vessel. By applying adapted ejector technology and parallel compression, these units can be applied globally with a significant energy saving compared to traditional system layouts.