Reusing waste heat: a practical example
Martin Grimstad, a 26 year old process engineer,got to experiment with waste heat reuse in a veryhands-on way at the Alcoa aluminium smelter inMosjøen.
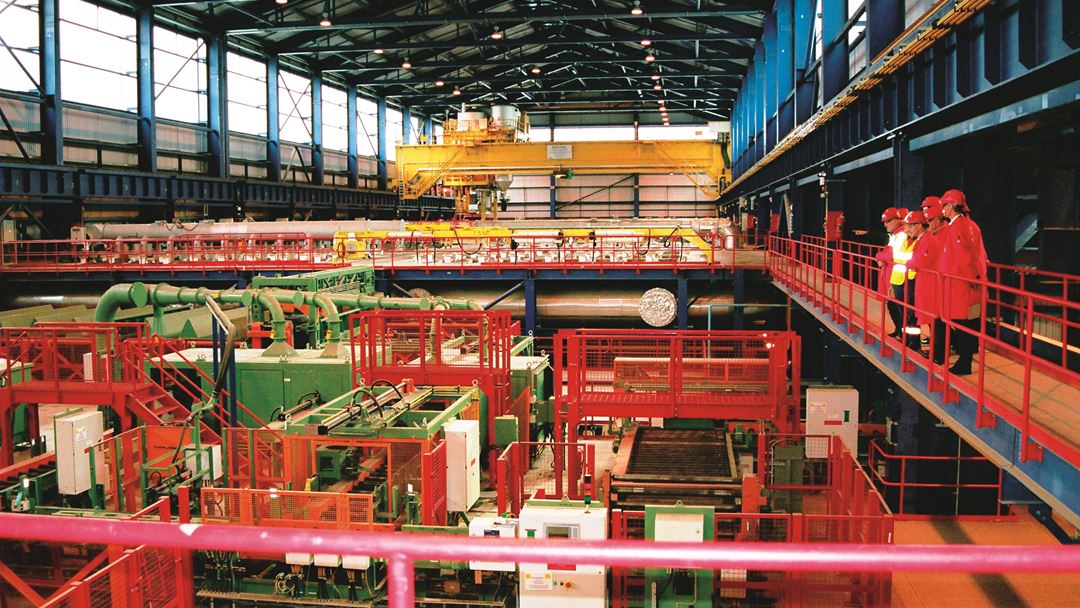
His HighEFF- related master's thesis was about "pre- warming anodes in aluminium production" and demonstrated how heat that would otherwise go to waste can be used to save electricity – and money.
Aluminium production explained
To understand exactly what Martin tested, we first need to take a look at how aluminium is produced. First you take a large steel vat called a reduction pot. In the bottom of that pot are carbon cathode. Next you have an electrolyte solution, the input material (aluminum oxide) and fi nally, at the very top, some anodes, also made of carbon. These weigh one tonne each when they are new.
An electric current gets passed through the anode, the electrolyte solution and the cathode, and a chemical process happens that results in liquid aluminium (which sinks to the bottom) and CO2 gas.
The fact that CO2 is emitted means that the carbon gets slowly used up, so the anodes have to be replaced about once every month. Because there are 18 anodes in the vat, and because it would be logistically impractical to switch them all at once (and also cause great disturbance to the cell), every two to three days, two anodes are replaced.
These old, used up anodes will be recycled to make new ones, but fi rst they must cool down. This is where Martin Grimstad comes in.
Reusing heat
"The chemical process that makes aluminium only works well at temperatures around 960°C, says Martin Grimstad. When you place two new, room- temperature anodes in the vat, you cool down its contents signifi cantly, particularly in the area that's immediately adjacent to the new anodes." It takes about one to two days for the temperatures to go back to normal after new anodes are put in.
The idea, then, was to simply use the old anodes to warm up the new ones.
This was done by simply placing two hot, old anodes on either side of one cold, new one. Let them sit there for a while and then measure the eff ect. Measurements were taken after 1 hour, 2 hours and 4 hours. A hole was drilled in the new anode to measure its core temperature. Results were encouraging. After four hours between two old anodes, a new anode's core temperature was 150°C, while its surface temperature was 250°C. This is energy that won't have to come from the vat anymore, which means less use of electricity, and ultimately a cheaper production process.
All this from heat that would have been wasted anyway.
Presenting results
Martin Grimstad got to present his results at the HighEFF Annual Consortium Meeting. "It was a bit nerve-wracking to present in front of all these smart people, but ultimately a nice experience. The results were well received by the audience."
A solution full of potential
The technique used for heat reuse in this case was quite simple, according to Martin Grimstad, and could be improved upon even further. "We could have the hot anodes in some kind of closeable enclosure to minimise loss from radiating heat."
More work also needs to be done before such a solution gets put to use. "Switching those anodes is precise work that requires careful planning. With 400 vats at the smelting plant, it's a lot of anodes to switch and if they have to sit there for 4 hours to warm up, it will change the whole schedule. In the future, this could be solved with other improvements like robot cranes, for example."
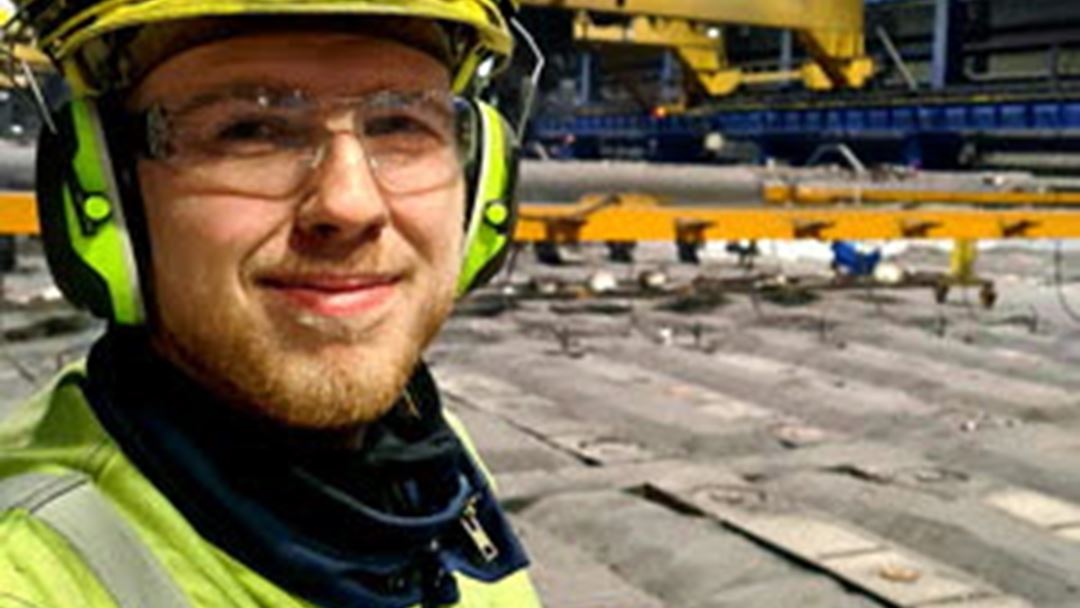