New heat exchanger concept for aluminium smelter off-gas
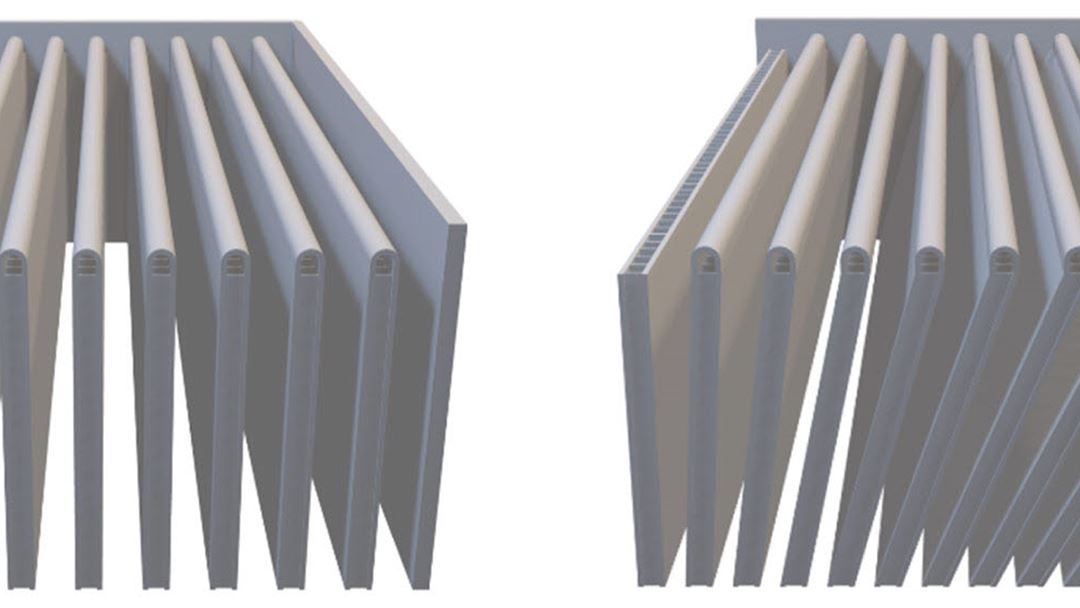
Vidar Torarin Skjervold, Research Scientist, SINTEF Energy Research
Significant amounts of surplus heat between 100-150 °C is available at aluminium production plants. The larger plants in Norway each reject around 1 TWh each year through the off-gas, but due to a lack of internal and external heat demands this heat is commonly not utilised. In addition to energy recovery, efficient heat exchangers are required for further process improvements on efficiency and emissions reductions. Aluminium smelter off-gas contains particles and fines from the electrolysis that can form solid layers on surfaces, a phenomenon often referred to as scaling. In order to avoid scaling and ensure operational stability, additional considerations must be made in the heat exchanger design.
Heat exchangers that are designed to cool clean, particle-free gases often apply surface enhancements to increase the heat transfer. However, such concepts are not suitable for aluminium off-gas due to the risk of scaling. By drawing inspiration from clean gas concepts, we have investigated a modified plate-type heat exchanger without any fins on the gas side. Two variations of the concept were investigated: a straight exchanger and an exchanger with a gradual contraction along the heat exchanger length (see pictures below). Detailed heat exchanger simulations were performed, and results were compared to a clean gas reference exchanger. The analysis revealed that the proposed concepts are competitive both in terms of weight and compactness compared to the clean gas concept.
We will develop these heat exchanger concepts further in 2020. In collaboration with industry partners we are seeking opportunities for testing and validating our new concepts in an industrial environment.