Pinch analysis of a fish meal production process
Sverre Foslie, Research Scientist, SINTEF Energy Research
Fishmeal and fish oils are used worldwide as feed or omega 3 fatty acids, playing an increasingly important role as the world’s population increases and the available land area for production of food is decreasing. Utilizing the sea for food production is one of the solutions for increasing food supply, and the focus on sustainability in the sea food production chain is increasing. Fishmeal and oil are mainly produced from waste from other fish products, and are important for utilizing as much as possible of the captured fish.
The fish meal production process is quite standardized and has not changed much in the last decades. Within energy efficiency, the main developments have focused on evaporation of water, where mechanical vapor recompression (MVR) has significantly reduced the energy consumption of the process. When it comes to drying technologies, the hot air dryer still dominates the market even though more energy efficient technologies exist, such as superheated steam dryers.
However, as the fish meal production has a long history, several facilities exist where the evaporation is still based on older technologies, such as the less energy efficient multi-stage evaporation. In contrast to the MVR evaporators which are electricity-driven, these use heat as the driving force. The heat is either delivered by steam from fossil fired boilers or from waste heat from the dryers.
In this case study, a pinch analysis methodology has been used to identify energy efficiency measures in a fish meal processing plant which currently uses a multi-stage evaporator heated by a combination of waste heat and process steam. The study was based on an energy analysis carried out in 2018, identifying process streams suitable for heat integration or heat upgrade.
Two different options were evaluated, one where the process is kept more or less as it is today, and one option where the multi-stage evaporator is replaced by a modern MVR evaporator. In both options, several different cases are evaluated. The pinch analysis identified the pinch temperature of the two different processes and the minimum external heating requirement. The pinch temperature is the temperature for which no external heating is required below, and no external cooling above, if full heat integration of the streams is achieved. The pinch temperature therefore also tells us which temperature range a heat pump should operate in.
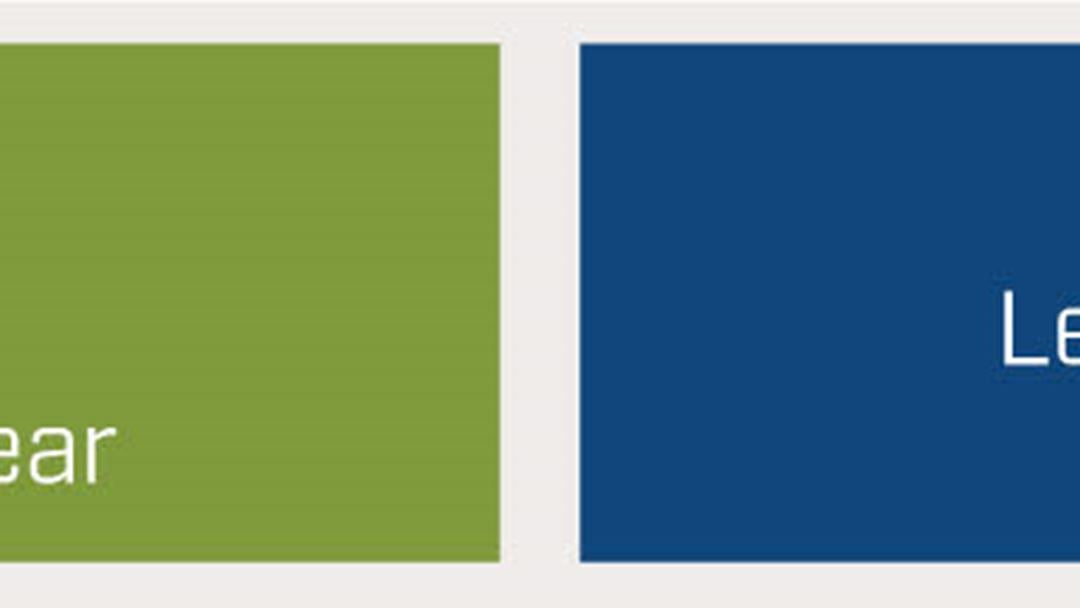
The main finding of the study was that implementation of a heat pump utilizing the waste heat from the existing multi-stage evaporator can provide nearly as high energy saving as replacing the evaporator with a new MVR evaporator. This is likely to have a significantly lower cost than replacing the evaporator entirely, with much smaller changes of the process. The energy saving potential ranged from 17% to 39% with reduction in CO2 emissions of 18% to 41%.
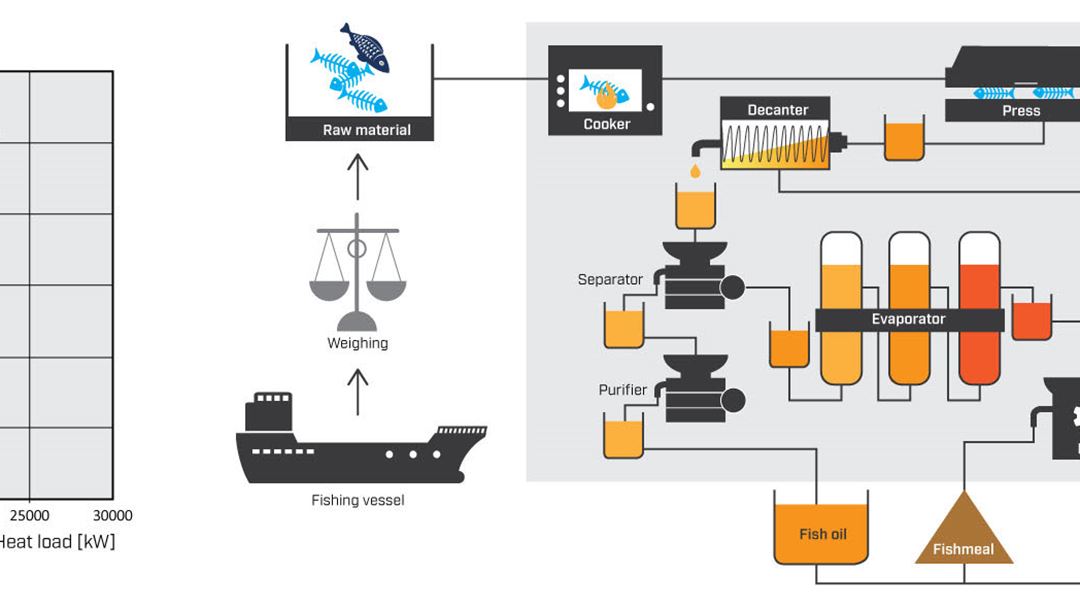