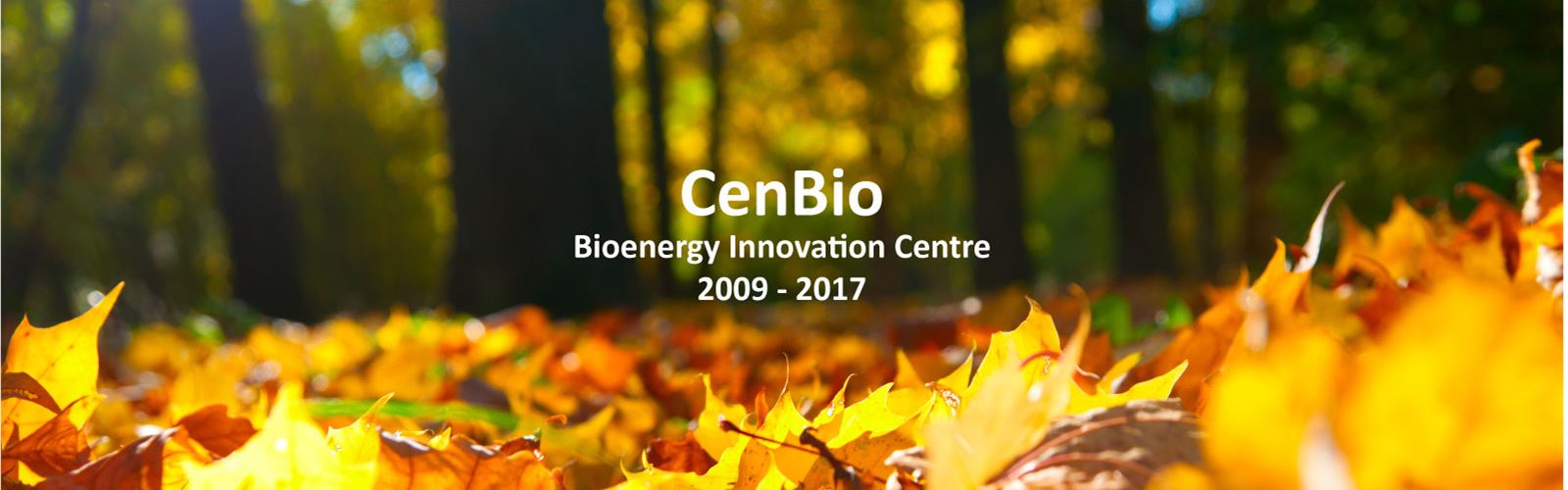
CENBIO - Enabling sustainable and cost-efficient bioenergy in Norway
SP6 - Value chain assessment
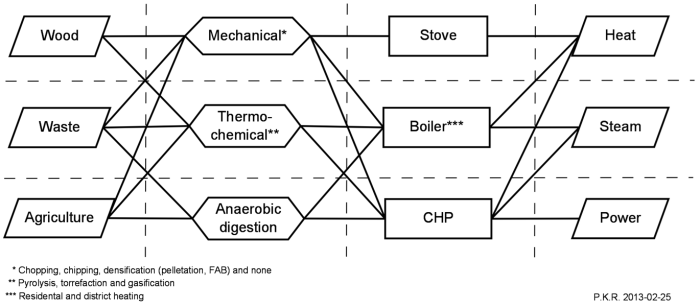
The specific objective of SP6 is to identify the portfolio of individual value chains that will enable a sustainable increase of bioenergy utilization in Norway. This task entails the following four sub objectives:
- Identification of the environmental and economic characteristics of current individual Norwegian bioenergy value chains (individual performance)
- Identification of the total overall environmental and economic characteristics of the current Norwegian bioenergy system (total performance)
- Identification of the environmental and economic characteristics of prospective novel individual Norwegian bioenergy value chains (individual performance)
- Identification of the total overall environmental and economic characteristics of alternative scenarios for different prospective Norwegian bioenergy systems (total performance)
The value chains concept can be seen as a combination of many research activities from CenBio. Per today, CenBio accounts for 30 value chains, grouped by fuel type.
In 2015, the SP6 team has been working on the calibration of the value chains, with a focus on the Waste-to-energy (WtE), the Biogas and the Wood stove value chains. See a representation of the CenBio value chains in Figure 1.
![]() |
Figure 1: CenBio's 30 value chains. |
WP6.1 – Environment and Cost Assessments
Waste-to-energy (WtE) value chain
WtE plants have the dual objective to reduce the amount of waste sent to landfill and simultaneously to produce useful energy (heat and/or power). Energy from WtE is gaining steadily increasing importance in the energy mix of several countries. Norway is no exception, as energy recovered from waste currently represents the main energy source of the Norwegian district heating system. Also, 50% of the energy from the WtE sector is accounted for as renewable in Norwegian national statistics, and the sector is thus an interesting candidate in helping to reach the national renewable target.
The Norwegian WtE sector has been a growing industry for the last decade, increasing from a total capacity of 1.3 million tonnes/year in 2010 to 1.7 million tonnes today. The sector currently accounts for 17 plants, spread all across Norway. The average throughput is 90% of the capacity, and the production is around four TWh for district heating networks, in addition to some electricity and process steam for industries located near the plants. Yet several Norwegian WtE plants are currently suffering from low profitability. The main reason is that the processing capacity exceeds the waste produced in the Scandinavian market, where the gate fee is set by the Swedish WtE plants.
A market with excess capacity will put the gate fees under pressure, which is not financially viable in the long run. Two alternatives are either to reduce the processing capacity or to increase the demand for processing capacity. An increase in demand for processing capacity can be achieved by importing waste from markets with insufficient capacity, i.e. countries where the waste would otherwise be landfilled and/or by the insertion of challenging new waste fractions. The latter opportunity has further been investigated by the SP6 team this year, and the insertion — and thus co-combustion — of challenging new waste types such as car fluff, clinical waste and waste wood is assessed.
Life cycle assessment (LCA) is a methodology that has been used extensively within the last decade to evaluate the environmental performance of waste treatment systems and in particular WtE technology such as incineration, and an innovative approach for combining detailed LCA with technology evaluation is used to assess CenBio's WtE value chain (see a schematic drawing of the WtE value chain in Figure 1). Mass transfer coefficients and leaching coefficients are used to trace emissions over the various life-cycle stages from waste logistics to final disposal of the ashes. In addition, the plant model together with actual data on the input waste, air and water emissions and ash composition are used to assess the influence of a change in waste composition on the environmental performance of a WtE plant in a Norwegian context. The Heimdal plant, owned by Statkraft Varme is used as a case study, with close collaboration with the plant owners.
![]() |
Figure 1: Waste-to-Energy value chain. |
The results indicate that the insertion of waste fractions containing a higher amount of heavy metals and fossil CO2 decreases the overall environmental performance of the plant for an input-based functional unit while the opposite might be true for an output-based functional unit if the new waste fraction has a higher energy content than the common waste mix. We benchmark the environmental performances of our WtE systems to those of fossil energy systems, and we find better performance for the majority of environmental impact categories, including climate change, although some trade-offs exist (e.g. higher impacts on human toxicity potential than natural gas, but lower than coal). In addition, the insertion of challenging new waste fractions is demonstrated to be an option to both cope with the excess capacity of the Norwegian WtE sector and to reach Norway's ambitious political goals for environmentally friendly energy systems.
Wood stove value chain
Improvements in wood stove technology will influence the emission profile, but technology improvements have monetary costs. This year, an integrated analysis considering environmental and economic aspects of two different wood stove technologies (old and new wood stoves with technology for staged air combustion, which reduces particle emissions) operated on different loads (partial and nominal) has been performed. See Figure 2 for an overview of the wood stove value chain.
The environmental analysis is a state-of-the-art LCA, where greenhouse gases as well as other air pollutants affecting human health and having environmental impacts were included. The economic analysis is a cost assessment, analysing cost structures and comparing costs between different wood stove technologies and operation modes. The costs estimated in the analysis are levelised cost of energy, meaning no margins or profits are included. The addition of margins is also analysed, through three levels of margins in addition to the base case. This way, trade-offs between environmental impacts and between environment and economy can be revealed. The analyses are based on empirical and experimental data from the CenBio project partners, describing the current situation in Norway.
![]() |
Figure 2: Wood stove value chain. |
The results from the environmental analysis show that the switch from an old wood stove technology to a new technology with staged air combustion gives a decrease in all emissions and impact categories. However, we see that the effect of the stove load is even more important for many of the impacts and emissions. Climate change can be reduced by more than 80 percent, and particulate matter by more than 90 per cent, going from the most polluting technology to the cleanest. Combustion in the wood stove is the main contributor to all impacts and emissions except ozone depletion and freshwater eutrophication, where transportation dominates.
The results from the economic analysis show that the cost reduction from the most expensive to the cheapest technology is approximately 10 per cent. The largest costs arise at the end of the value chain, where operational expenditures for transportation and firewood production and capital expenditures for the wood stove make up approximately 75 per cent of the cost. Adding margins to the levelized cost of energy, we see that even a moderate margin of 10 per cent affects the cost as much as a switch from the cheapest to the most expensive technology.
Comparing the results from the environmental and economic analysis, we see that there is a clear trade-off in terms of environmental impacts and costs. The cleanest technology is the most expensive and the most polluting is the cheapest. However, the emission reductions are overall substantially higher in per cent than the cost increase. For both environmental impacts and costs, the main hot spots in the value chain are transport and combustion in the wood stove.
Biogas value chain
The production of biogas through anaerobic digestion has grown rapidly over the years, mainly due to the increasing global concerns about mitigation of greenhouse gas emissions from the energy sector and enhancement of energy security. Biogas can be used directly for heating and electricity generation and as a substitute for other fossil fuel applications, e.g. transportation fuel. The potential utilization of the digestate as fertilizer can also reduce dependence on energy intensive mineral fertilizers, to further mitigate greenhouse gas emissions. However, the quantification of the climate change impacts and possible benefits of biogas systems is highly dependent on many factors, such as the type of feedstock, operational practices, energy and materials consumed for cultivation and transport of feedstocks, biogas utilization and demand for transportation and disposal of the process residues. In addition, choices related to the LCA methodology undertaken in the analysis, such as allocation issues, definition of system boundaries and functional units, can also shape the final outcomes. See the biogas value chain in Figure 3.
![]() |
Figure 3: Biogas value chain |
In order to prevent possible burden-shifts of concerns, other environmental impact categories than climate change should also be factored in the assessment, such as eutrophication, acidification, toxicity, primary energy consumptions. All these factors have to be considered in the quest for environmental friendly and sustainable energy production from biogas.
To calibrate the biogas value chain to Norwegian context, the SP6 team has been working in close collaboration with the Lindum plant, located in Drammen and which uses Cambi technology.