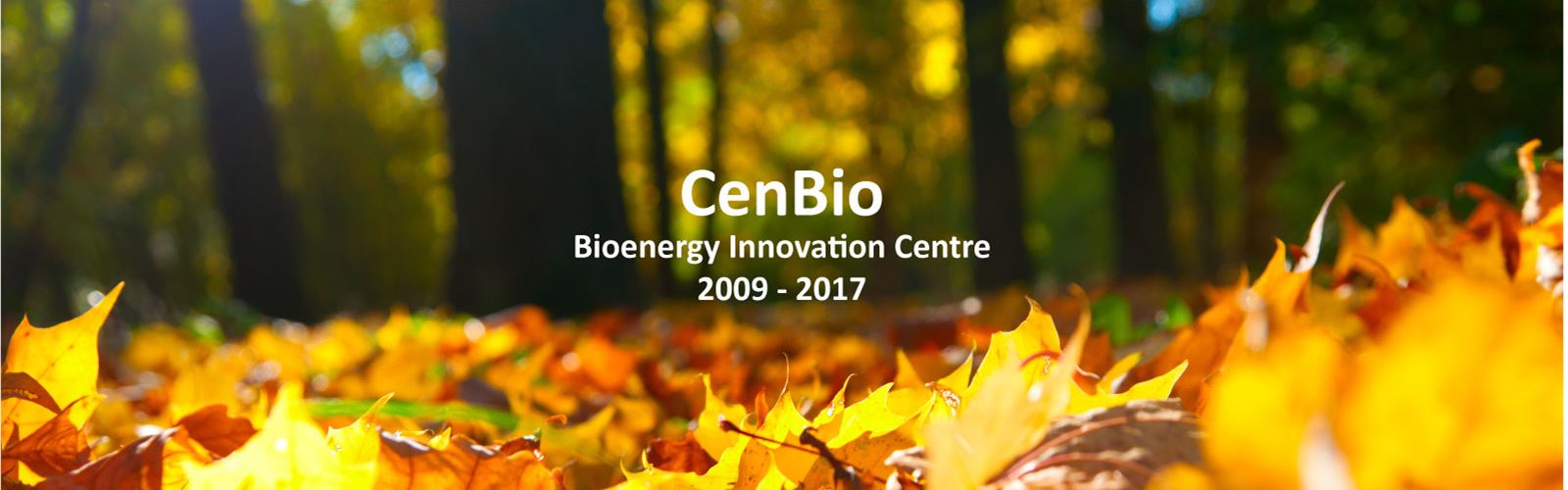
CENBIO - Enabling sustainable and cost-efficient bioenergy in Norway
SP3 - Conversion technologies and emissions
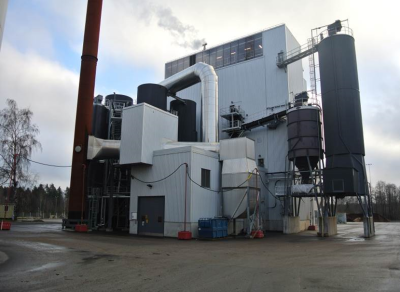
Making wood combustion cleaner is essential, especially for the local air quality. The CenBio goal for particle emissions from residential wood stoves is 2.5 g parti-cles per kg dry wood, and increased energy efficiency. The part load issue is also important, in addition to standardization of testing methods related to EU directives.
SP3 covers as well the demonstration of increased efficiency and innovative solutions for district heat. Working within networks, such as IEA Task 32 – Biomass combustion and co-firing, and IEA Task 36 – Integrating energy recovery into solid waste management systems, and together with Avfallsforsk (national research arena) and Prewin (European industrial network for Waste to Energy, WtE), is crucial to stay at the forefront of R&D and to understand the industry needs.
Innovative concepts for combined heat and power (CHP) are also investigated, such as the ChlorOut technology developed by Vattenfall. ChlorOut is a concept reducing corrosion and fouling for biomass-fired boilers, as well as NOx, CO and dioxin emissions. The concept has been tested at the Jordbro biomass combustion plant in Sweden.
For each conversion technology investigated within SP3, issues related to emissions are in the spotlight. They are investigated through four approaches:
- Plant emissions mapping (e.g., Energos/Hafslund WtE plant at Borregaard in 2012 and Akershus Energi bioenergy plant at Lillestrøm in 2014)
- CFD modeling
- Experimental studies
- Literature surveys (e.g., NOx reduction methods)
Innovations from SP3 are initially expected in the following areas:
- New efficient clean-burning stoves and fireplaces
- Concepts for ultra-efficient district heating plants, possibly utilizing biogas and solid waste in synergetic combination
- Concepts for heat and power plants with close to 100 % combined energy efficiency
- New recipes for low-emission plants
WP3.1 - Wood and Pellets Stoves
Today, small-scale wood combustion in wood stoves accounts for close to half of the bioenergy use in Norway, and the use of wood logs in small-scale units and pellets in pellet stoves is expected to increase substantially towards 2020. The goal of this work is to more than double the energy output from those units within 2020. That means more than a double energy output from these units compared with today. This demands increased efforts both with respect to emission reduction and efficiency increase to prevent increased amounts of harmful emissions and increased negative health aspects.
The objectives of WP3.1 are to:
- Develop innovative new efficient clean-burning stoves and fireplaces;
- Reduce particle emissions by 75% compared to the present national emission requirements;
- Increase energy efficiencies from 75% up to 85%.
Since the utilisation of firewood is expected to substantially increase within the next decade, it is essential to ensure that harmful emissions (e.g., particles) are minimised, and that national requirements and regulations are uphold and improved. Those considerations should not be relaxed by new EU directives not taking into account the special Norwegian conditions. Partial load performance is very important, since firing at partial load will be the typical situation in Norway. Standardisation of testing methods is then a key issue, through active participation in the international standardisation work related to new EU directives.
Development and testing of new and improved combustion chambers and solutions for improved combustion and reduced emissions caused by incomplete combustion are the key research activities in WP3.1. The focus is primarily on various types of wood stoves (including light heat storing units), but also fireplace inserts, pellet stoves and combined units. Key aspects are efficiencies, cost-efficiency, emissions, fuel flexibility, fuel quality and user-friendliness.
Standardisation work
Through CenBio, SINTEF Energy Research has in recent years actively contributed to the European standardisation work, CEN/TC 295 working groups 5, 6 and 7.
CEN (Central European Norms) is a private, international, non-profit organisation based in Brussels and is one of three European standardisation organisations officially recognised by the EC and EFTA as being responsible for developing and defining voluntary standards at European level. The standardisation activities of CEN are steered by the Technical Board (BT). Technical Committees (TCs) prepare standards. Working Groups (WGs) develop the standards (e.g. CEN/TC 295 WGx). Experts, appointed by the CEN Members but speaking in a personal capacity, come together and develop a draft that will become the future standard. CEN started to develop standards for residential solid fuel-burning appliances in 1992 through CEN/TC 295. In 1999, CEN/TC 295 approved the first European product standards on most commonly used residential solid fuel-fired appliances. Since 2002, all CEN member countries have withdrawn their existing national standards giving requirements for construction, safety, heat output, efficiency and emissions. In 2000 TC 295 started new work to modify these four product standards into harmonised standards (EN) according to the rules of the EU Directive for Construction Products.
Regarding the wood stove test standard (Residential solid fuel burning appliances), a plurality of national standards, test methods and labels have emerged to compensate for the currently outdated standard. Meaning costly, confusing and time-consuming approval processes for the manufacturers. Some of the main reasons for harmonising the current plurality of standards are:
There is no harmonised particle measuring method for fireplaces and wood stoves in EuropeStandards (EN13240, EN13229) for wood burning fireplace insets and wood stoves set requirements mainly on safety, efficiency and CO emissionOutdated (1999) standards for wood burning appliancesParticle emissions from wood heating is regarded as a significant source of hazardous emissionsBeside countries applying the EN 13240 including DIN+ (VDI 2066) for dust measurements, a few European countries such as Norway and the United Kingdom have their own standards for measuring particles and also other countries (Austria, Germany, Denmark) set emission limits for PM from wood firingDifferent traditions in Europe how to measure particles makes it difficult to find a compromise for one measuring method (8+15 years and counting as of today)Norway and the United Kingdom use a dilution tunnel to measure solid + condensed particles all over the combustion cycle at different burn rates (both good and poor combustion conditions were tested)Germany's most frequently used method VDI 2066 measures in the chimney with a heated filter for 15/30 min at nominal heat output
Through this work a series of documents have been prepared, the FprEN 16510-series, by Technical Committee CEN/TC 295 "Residential solid fuel burning appliances", the secretariat of which is held by BSI. The documents have been prepared under a mandate given to CEN by the European Commission and the European Free Trade Association. As of February 2016, the proposed 16510-series of documents has been submitted for a formal vote. Together the FprEN 16510-2-1, FprEN 16510-2-2, FprEN 16510-2-3 and FprEN 16510-2-4 the series will totally supersede EN 13240:2001, EN 13229:2001, EN 12815:2001, EN 12809:2001. The revision of these European Standards takes into account the comments received at their 5-year review. The structure of EN 16510, Residential solid fuel burning appliances, is as follows:
- Part 1-0: General requirements and test methods;
- Part 2-1: Roomheaters;
- Part 2-2: Inset appliances including open fires;
- Part 2-3: Cookers;
- Part 2-4: Independent boilers — Nominal heat output up to 50 kW;
- Part 2-5: Slow heat release appliances;
- Part 2-6: Appliances fired by wood pellets.
Concerning the measurement method, the current documents now include two methods of choice when it comes to measure the total amount of suspended particles - one method much like the current DIN+ method and one method similar to, although much changed, the current Norwegian dilution tunnel test method NS 3058-59. - Annex F in part 1 contains two methods to measure particulate matter. The first method is measurement by sampling a partial flue gas sample from the measurement section over a heated filter. The heated filter samples the solid fraction of the total particulate matter concentration. The second method measures particles by sampling a partial flue gas sample from a full flow dilution tunnel using a filter at ambient temperature.
The following comments all the main objections from the Norwegian experts, to the full flow dilution tunnel method currently implemented in FprEN 16510-1: 2013 Residential solid fuel burning appliance general requirements and test methods:
The inclusion of the second method is much thanks to the active participation from SINTEF Energy Research, SP Fire Research AS, Standard Norway and the Norwegian Environment Agency, in the compilation of these standardization documents. The work of assuring that a sufficiently acceptable test method is implemented will continue at SINTEF, at least in 2016, depending on available budgets. Related to this work is also the harmonization of FprEN 16510 with the current Eco-design requirements, as there is currently a mismatch between the requirements in Eco-design and the test methods described in FprEN 16510. The three methods referred to in Eco-design are the current valid standards in Europe; NS 3058-59, EN13240 DIN+ and the English method, while the two methods described in FprEN 16510 are some altered versions of the German and the Norwegian test method.
Eco-design
Several standards and regulations setting emission measurement methods are currently aiming at significantly stricter emission limits for point source heating applications like wood stoves. The most important among these are the Eco-design Directive, the European standard (CEN), The German DIN (Deutsches Institut für Normung) and DINPlus method, the German BImSchG (Bundes-Immissionsschutzgesetz) regulations As Well As the Nordic Ecolabelling of stoves. A working group (LOT20) has been given a mandate to assess whether it is appropriate to set stricter Eco-design requirements for energy efficiency and for emissions of particulate matter (PM), organic gaseous compounds (OGC), CO and nitrogen oxides (NOx). The Eco-design requirements were recently approved in September 2014. The new requirements will be operative from 1 January 2022.
The new requirements for seasonal space heating energy efficiency for typical solid fuel wood stoves shall be no less than 65 %. The seasonal space heating energy efficiency shall be calculated as the seasonal space heating energy efficiency in active mode (based on the net calorific value of the fuel at nominal heat output) corrected by contributions accounting for heat output control, auxiliary electricity consumption and permanent pilot flame energy consumption.
When it comes to emissions of PM from closed fronted solid fuel local space heaters, these shall not exceed 20 mg/Nm3 at 13% O2 when measured with a heated filter (first method/current European method) at nominal load as well as at part load if appropriate. When measured by the second method (Norwegian method), i.e. over the full burn cycle using natural draft and a full flow dilution tunnel with particle sampling filter at ambient temperature, the requirements are 5 g/kg (dry matter). When measured by the third method (English method), i.e. PM sampling over a 30 minutes period, using a fixed draft of 12 Pa and a full flow dilution tunnel as well as either a particle filter at ambient temperature or an electrostatic precipitator, the requirements are 2.5 g/kg (dry matter). For OGC, CO and NOx the requirements are 120 mgC/Nm3, 1500 mg/Nm3 and 200 mgN/m3 expressed as NO2¸ all values taken at 13% O2. Additional requirements for product information/technical documentation have also been formulated.
The increased stringency of these European standards will at some point have to be reflected in the Norwegian standard. It is therefore expected that the Norwegian standard, NS3059, which have had the same emission limits since 1998, will have to tighten up its current weighted emission limit of 10 g/kg, possibly down to 2-5 g/kg. The maximum allowed emission of 20 g/kg will also probably have to be reduced with at least 50% or more, down to 5-10 g/kg. Emission limits for OGC and CO will also probably be included as provided by the new Eco-design requirements.
KPN WoodCFD - new in-kind project in CenBio
KPN WoodCFD is the successor to KPN StableWood, a CenBio in-kind project that was finalised in 2014, focusing on clean and efficient wood stoves through improved batch combustion models and modelling approaches, specifically:
- Model development: improved transient wood log and gas release models, transient heat transfer and storage models, reduced kinetics models (NOx and soot), and transient models and approaches for heat distribution in the building; and verification of these.
- Simulations: transient and stationary CFD simulations of wood stoves, and room and building integration simulations; and verification of these.
The project started January 2015 and will last until December 2018, and involves the same partners as in StableWood. See the WoodCFD webpage for more information.
WP3.2 - District Heat
This work package focuses on Waste-to-Energy (WtE) challenges. In 2015, the activity was related to discussions on the future of Norwegian WtE and a workshop on bioenergy, as well as participation in international networks, such as the IEA Bioenergy Task 36 (Integrating Energy Recovery Into Solid Waste Management Systems).
"Norwegian WtE 2030": ICheaP12 conference article
SINTEF-ER, Statkraft, Hafslund, EGE Oslo and Energos co-authored a peer-review conference article and a poster presentation addressing the opportunities and challenges in Norwegian WtE. A difficult but necessary exercise is to secure the place of the sector in an ever-changing market and regulatory environment: see key points in the conference poster reproduced below.
Clinical waste – Is co-combustion in WtE plants feasible?
There is an increasing interest for the disposal and energy recovery of "new/unusual" waste fractions, especially hazardous ones, in MSW incinerators. This opens the opportunity for a win-win situation: local and responsible treatment of non-material recyclable waste fractions and additional economic revenue for WtE actors. What about healthcare-related waste fractions?
Several important points relevant for (combustion and/or) co-combustion of clinical wastes from health care institutions can be inferred from the information gathered in D3.2.16:
- Combustion behaviour: a very heterogeneous material & some problematic elements
Wastes from health care institutions are clearly a very heterogeneous waste fraction. While some fractions have high-energy content (plastics), others will have high moisture contents (materials contaminated by organic matter).
Some fractions contain high amounts/concentrations of potentially harmful substances and/or chemical elements such as PVC that contains more than 50 wt% Cl, a chemical element involved in corrosion. However, MSW is also heterogeneous so this aspect may not be a main challenge for large MSW incinerators, especially as the amounts of this specific waste fraction is small. The wastes can be mixed and/or shredded to improve homogeneity but it may not be possible to do this together with MSW as the Waste Incineration Directive (WID) article 6.7 states that Infectious clinical waste should be placed straight in the furnace, without first being mixed with other categories of waste and without direct handling.
It is similarly specified in Avfallsforskriften for infectious waste (§ 10-12. Smittefarlig avfall): Ved forbrenningsanlegg som har tillatelse til å behandle smittefarlig avfall, skal dette føres direkte inn i forbrenningsovnen uten at det blandes med andre avfallstyper først og uten direkte berøring.
- Logistics: transport, handling and storage may pose specific requirements
In order to reduce the specific risks associated with these wastes, for HSE and/or regulatory reasons imposed by the authorities, some specific measures may have to be implemented to ensure proper and safe handling of health care wastes from their collection sites to their introduction into the combustion chamber. Typical measures include: dedicated containers for storage and transport, possibility for disinfection, dedicated loading system or direct introduction in the feed hopper, segregated storage and transfer areas, eventually with refrigeration.
- Technological considerations: thermal treatment technology – is there a preferred solution?
For dedicated installations burning hazardous/infectious wastes, rotary kilns have often been a preferred technology as they are very robust and reach high operating temperatures that can destroy most harmful substances.
When it comes to co-processing clinical wastes in MSW incinerators, the situation is different as about 90% of MSW incinerators in the world are grate incinerators. Modern grate incinerators can handle solid fuels with large particle sizes and high moisture contents, a main limitation being the range of LHV (Lower Heating Value) accepted. As wastes from health care institutions often represent small volumes compared to MSW, and as long as they are incinerated on the grate with a large fraction of MSW, it is little probable that overall operation (combustion process and flue gas cleaning especially) will be significantly disturbed or that the eventual disturbances cannot be handled by the operators (after a period of adaptation). However, concerning operation, WID article 6.2 indicates that (bold added)
Co-incineration plants shall be designed, equipped, built and operated in such a way that the gas resulting from the co-incineration of waste is raised in a controlled and homogeneous fashion and even under the most unfavourable conditions, to a temperature of 850 °C for two seconds. If hazardous wastes with a content of more than 1 % of halogenated organic substances, expressed as chlorine, are co-incinerated, the temperature has to be raised to 1 100 °C.
Avfallsforskriften (Vedlegg IX) poses the same requirement for hazardous and infectious waste:
For forbrenningsanlegg som forbrenner farlig avfall og/eller smittefarlig avfall som inneholder mer enn 1% halogenerte organiske forbindelser, uttrykt som klor (Cl), skal temperaturen økes til minst 1100 °C i minst 2 sekunder.
This point infers that if infectious/hazardous wastes from health care have a high content of halogenated organic substances (halogens are F, Cl, Br and I), the minimum operating temperature has to be greatly increased. This is very detrimental to existing plants and such a case would probably mean that co-incineration with MSW is not to be considered as a viable option.
Co-incineration of wastes from health care institutions with MSW appears to be a win-win opportunity both for the waste producer (disposal of the waste by a professional actor) and the WtE sector (extra revenues). Operational challenges (combustion process) do not seem unsurmountable as long as the operating temperature does not have to be altered. However, the current regulation imposes stricter requirements on several aspects of the waste management value chain (transport, handling, storage, feeding) and all these measures will cost money if they are not eased or alleviated by the responsible authorities.
Workshop How to ensure bioenergy production in a sustainable and efficient manner in Norway? – From strategies to actions
CenBio partners appreciate workshops in order to get a quick overview on a specific topic, meet relevant actors and exchange ideas. In 2015, the following workshop was organised by SINTEF-ER:
- How to ensure bioenergy production in a sustainable and efficient manner in Norway? – From strategies to actions
- Both R&D representatives and industry (both CenBio and non-CenBio) were invited in order to cover the entire value chain.
The day began with a short introduction to how CenBio works with sustainability assessment of the various value chains. This was followed by two interesting and educational presentations from researchers in our neighbouring country, Sweden. We heard what the Swedish forestry sector looks like, what are their challenges and which opportunities they investigate and implement in order to get a more efficient forestry industry ("Efficient forest fuel supply system" / "Storage"). Then we followed a presentation from Arbaflame, a company that produces upgraded biofuels by steam explosion for use as coal substitute through cofiring in coal fired plants.
The first part of the afternoon was devoted to Norwegian district heating and we heard interesting presentations from Hafslund, Telemark University College and Statkraft. They all presented district heating from their respective angle, including new technologies, opportunities and challenges. Waste-to-Energy, biomass combustion and biogas production were covered during this part of the workshop. The presentations gave a good insight into this part of bioenergy production that is the biggest in Norway when it comes to bioenergy production apart from residential heating (wood stoves). Finally, an interesting report from the Norwegian Environment Agency (Miljødirektoratet) was presented. This report presents concrete measures that can be implemented to reach a low-carbon society in the coming decades. It will be a central support/tool for politicians in their decision-taking processes including policy shaping.
The day ended with a good discussion about politics, profitability and obstacles. During the discussions it became clear that there are some political issues (clear strategy, regulatory/legal framework) which represent great obstacles. As there were no politicians present the attendants discussed shortly how it could be possible to inform decision makers and cooperate with politicians.
Agenda and participants list was as follows:
WP3.3 – Heat and Power
CenBio aims for close to 100 % combined energy efficiency
Heat and power plants based on waste and biomass including also residues (e.g., sawdust) and upgraded fuels (e.g., pellets), are complex and challenging plants compared to most other heat and power technologies. This is due to the influence of the fuel on plant performance and economy. Small- to large-scale heat and power (CHP) plants are key technologies for an increased and efficient bioenergy utilisation in Norway and worldwide. The objective of this WP is to develop innovative concepts for heat and power plants with close to 100 % combined energy efficiency.
Industrial biomass heat based on combustion of forest/wood residues is important in, e.g., the paper and pulp and the wood processing industry, while municipal solid waste (MSW) is important in waste-to-energy plants. In both cases, there is a potential for significant improvements. It is essential to:
- Assess the potential for efficiency improvements through improved combustion process control and process integration in industrial heat plants, and to assess the cost-efficiency potential of this,
- Assess the potential for emission reduction through efficiency improvements, fuel modifications and operational changes.
Several technology options exist for CHP plants (e.g., steam turbines, gas turbines, gas engines, Organic Rankine Cycle (ORC), Stirling engine, etc.) suitable for different plant sizes. However, they differ with respect to achievable efficiencies, operational reliability and costs. In addition, combinations of different CHP technologies can be applied to further increase the electric efficiency, e.g., combined cycles or gasification in combination with ORC. Hence, for a significant introduction of biomass- and MSW-based CHP in Norway, it is essential to assess the suitability of the existing technologies and the potential for further improvements with respect to cost-efficiency and emission abatement, including framework conditions, and operational optimization. In 2012, a pop-tech. article on the status of biomass CHP in Norway, and the way forward, was published in Xergi. The list below shows the main ideas of the article:
- The power production from biomass and waste reaches a significant level in Norway today, with about 0.4 TWh per year.
- That is made possible due to the low cost of fuel, or even its negative cost, e.g., MSW.
- The dominating technology is steam turbine for solid biomass, with one steam engine as the only exception.
- The only technology is gas engine for biomass derived gas (landfill gas or biogas).
- The possibility of increased electricity generation from biomass will depend heavily on economic framework conditions.
- The introduction of green certificates in Norway, through the common Swedish-Norwegian green certificate market is an incentive for increased electricity generation from biomass, though, with a value of about 15 øre/kWh, this is still insufficient, notably to defend investment in small-scale CHP plant in Norway (< 10 MW fuel effect), unless:
- The fuel cost is very low, or
- The framework conditions for small- and especially micro-scale CHP is significantly improved (investment support, etc.)
- Continuous focus on fuel cost reduction is required to help improve the CHP plant economy.
Energy storage and low-temperature heat utilization for heat and power production
District heating consumption in Norway has increased during the last 10 years as shown in Figure 1. From 2012 to 2013, the increase was 11.3 % partly due to the start-up of new district heating and cooling plants and the expansion of existing plants. During the entire period service industries have accounted for the largest share of the consumption, and in 2013 their use of district heating accounted for about 3 TWh (65%). The average price for district heating rose from 56.6 øre/kWh in 2012 to 59.2 øre/kWh in 2013. For households and the service sector, the average price was 59.8 and 61.5 øre/kWh respectively, while it was lower for the industry, with 31.4 øre/kWh.
Waste-to-Energy (WtE) is a contributor to renewable energy production all over Western Europe with about 400 plants. In Norway, waste incineration is the main energy source for district heating accounting for 43% with 2.3 TWh produced in 2013 (Figure 1). The second largest contributor to district heating is wood chips combustion (1.1 TWh).
![]() |
Figure 1: Consumption of district heat by consumer group (left), net production |
WtE is the major contributor in the district heating plants in the largest cities in Norway and constitutes the base load. The supply of waste is quite constant during the year, while the heat demand varies significantly during the year. The result is a need for peak load from other heat sources during the winter season while there are significant amounts of excess heat during the summer. Options for utilizing this surplus heat produced during the summer season are requested. In this work a report has been written in close collaboration with Statkraft Varme and EGE Oslo, which gives an overview of some existing possibilities for utilising the surplus heat either through storage until the winter season or for production of electricity.
ChlorOut
Operational problems during biomass combustion can arise in the presence of certain elements such as alkali and chlorine (Cl) in the fuel. These problems are often described as alkali related. High levels of potassium chloride (KCl) in the flue gas often result in enhanced deposit formation, while high content of Cl in deposits may accelerate superheater corrosion. The main strategies to reduce alkali related problems are co-combustion and sulphur/sulphate containing additives.
Special attention in this WP is directed to implementation and evaluation of the so-called ChlorOut concept in a full-scale boiler in Jordbro designed for wood fuels, e.g., demolition wood and forest residues. It is a BFB boiler, 63 MWth, 20 MWel, with the steam data 470 °C /80 bar. The implementation was performed as a cooperation between Vattenfall Research and Development AB (VRD) and Vattenfall AB, BU Heat (Heat). The ChlorOut concept consists of IACM, a device for on-line measurements of KCl in the flue gas, and a sulphate-containing additive that converts the alkali chloride (i.e. KCl) to a less corrosive alkali sulphate. The additive applied is often ammonium sulphate (AS) and it can also have an impact on certain other emissions including NOx and CO.
![]() |
Figure 2: Reduction of NOx and KCl during a transient test with injection of ammonium sulphate in two different positions. AS = Ammonium sulphae (additive). (Vattenfall) |
The major achievements from 2010 until February 2016 are summarised here. A permanent injection system for the ChlorOut concept has been installed and fully implemented in regular operation of the boiler. Measurement campaigns were carried out by VRD prior to the permanent installation to optimise the dosage of AS, and measurements with deposit probes revealed that addition of AS reduced the content of KCl in the flue gases and Cl in the deposits. These results supported the implementation of the ChlorOut concept as a strategy to reduce the corrosion rate of the superheaters in the boiler. The permanent installation has been further evaluated and the most interesting results were obtained during long-term corrosion probe measurements with and without injection of AS. Here, the corrosion rate was significantly lowered with the ChlorOut concept. Certain aspects on the flue gas chemistry of KCl, NO and CO during injection of ammonium sulphate was presented in a conference paper at the 22nd FBC Conference in Åbo in June 2015. The paper was honoured with The Best Paper Award at the conference. A measurement campaign was performed in the BFB boiler in Jordbro based on these experiences. Here the focus was on the flue gas chemistry involving NO and KCl during injection of AS at different operating conditions. Figure 2 shows the importance of position for the simultaneous reduction of NOx and KCl and the performance of AS was better in position L2 at these specific operating conditions.
WP3.4 - Emissions
CenBio develops new concepts for reduced emissions
Air contaminants generated from combustion processes include sulphur oxides, particulate matter, carbon monoxide, unburned hydrocarbons and nitrogen oxides (NOx).
Emissions from waste and biomass combustion are a continuous concern and continuous efforts with respect to emission minimisation are needed in order to ensure that the planned/future increase in bioenergy use is environmentally benign. Stricter regulations are expected in the future for WtE (waste-to-energy) and BtE (biomass-to-energy) plants, and also for wood stoves.
Reduction of harmful emissions from different combustion units are addressed in this work package. Based on advanced tools and improved methods, new concepts for reduced emissions will be developed. The objectives of WP3.4 are to:
- Mainly, develop new recipes for low-emission plants,
- Develop numerical tools and methods required to study concept improvements,
- Get increased insight into mechanisms for NOx formation and reduction,
- Define state-of-the-art for NOx reduction measures in WtE and BtE plants,
- Map emissions for one specific plant by carrying out extensive measurements,
- Map the emissions for BtE plants.
The activities in CenBio to obtain these objectives include:
- Plant emission mapping,
- Emission modeling (Computational Fluid Dynamics),
- Detailed chemical kinetics evaluation (CHEMKIN, DARS, COMSOL),
- Detailed experimentally studies using advanced measurement methods (see also WP3.1 and WP2.1).
Emission mapping
Emission mapping for WtE and BtE full-scale plants is carried out through literature survey, collection of available data from the CenBio partners and experimental activity. In 2011, data received from the CenBio partners through an extensive questionnaire were compiled, and the need for new measurements was identified. Based on this background work, a plant was selected. The mapping campaign was carried out in June 2012 at the Hafslund WtE plant in Sarpsborg (Norway), which is Energos' technology. State-of-the-art measurement diagnostic equipment (FTIR, GC – see Figure 1) was utilised to measure gas concentrations at several positions within the primary and secondary chamber. The mapping campaign was carefully planned and prepared in close cooperation with Energos AS, a necessity to be able to perform advanced measurements and obtain high quality results.
A similar measurement campaign was carried out at the Akershus Energi BtE-plant in spring 2014. Extensive emission measurements such as those have hardly been carried out earlier at Norwegian BtE plants.
Figure 1: FTIR gas sampling and conditioning unit. (Photo: Sascha Njaa, SINTEF)
In 2015 two mapping campaigns have been carried out, one at the Statkraft Varme Marienborg bioenergy plant in Trondheim and another one at the Statkraft Varme bioenergy plant in Kungsbacka in Sweden. The main aim of the former was providing experimental data as input to and as validation for CFD modelling of the plant. This activity has been carried out in WP2.1 and is reported there. The main aim of the latter was operation optimization for emission minimization, providing guidelines and proposals for a real plant. This work resulted in strategies for reduced CO and NOx emissions, strategies that could be implemented at other comparable bioenergy plants.
The intention of the mapping is to serve as a basis for concept improvements, both numerical and experimental, as well as verification of CFD calculations and basis for model improvement. A new mapping may be carried out to verify the emission level if a new concept or improved conditions are included at the plant.
Emission modeling
Tools and methods to study emissions from biomass and waste conversion units will be developed. CFD modeling will be an essential part of this work, and combined with detailed chemical kinetics for the gas phase reactions, which is a necessity when modeling fuel NOx formation and reduction at low to moderate temperatures, this gives quite comprehensive calculations and detailed results.
In 2012, a characteristic geometry (the SINTEF multi-fuel reactor) was set up in the CFD tool Fluent to study NOx formation. A chemical kinetics mechanism developed in WP2.1 was implemented in the CFD tool. A representative syngas composition was selected and initial calculations performed. The outcome is a numerical tool that can be used to study NOx emissions and NOx reduction potential from biomass conversion.
In 2013, comprehensive modeling work was started to assess the NOx reduction potential in the multi-fuel reactor using CFD, which is compared with earlier experimental results. This work was finalised with a journal publication manuscript in 2014 with the title "Numerical simulations of staged biomass grate fired combustion with an emphasis on NOx emissions", to be presented at ICAE 2015 and published in the international journal Energy Procedia.
In the paper we studied NOx emissions from biomass combustion, with the objective to demonstrate the applicability of stationary computational fluid dynamics simulations, including a detailed representation of the gas phase chemistry, to a multi-fuel lab-scale grate fired reactor (the multi-fuel reactor), shown in Figure 2, using biomass as fuel. In biomass combustion applications, the most significant route for NOx formation is the fuel NOx mechanism. The formation of fuel NOx is very complex and sensitive to fuel composition and combustion conditions. And hence, accurate predictions of fuel NOx formation from biomass combustion rely heavily on the use of chemical kinetics with sufficient level of details. In the work we used computational fluid dynamics together with three gas phase reaction mechanisms; one detailed mechanism consisting of 81 species and 1401 reactions, and two skeletal mechanisms with 49 and 36 species respectively. Using the detailed mechanism (81 species), the results show a high NOx reduction at a primary excess air ratio of 0.8, comparable to the NOx emission reduction level achieved in the corresponding experiment, demonstrating both the validity of the model and the potential of NOx reduction by staged air combustion.
![]() |
![]() |
Figure 2: The multi-fuel reactor and the two-level grate system.
The next step could be a further development in order to study mixing behavior, combustion and emissions in furnaces and to develop new concepts or optimising existing processes, combined with measurements for existing plants or combustion units (e.g., wood stoves).
In 2015, the focus has been on CFD modelling of the Statkraft Varme Marienborg bioenergy plant in Trondheim, see WP2.1.