CEMCAP
WP10 Chilled ammonia process (CAP)
Although the CAP is on the verge of commercialization for coal and natural gas fuelled power plants, it has never been demonstrated for CO2 concentrations typical of a cement plant, i.e. exceeding 16vol%. Therefore, this work package aims at adapting the CAP to the conditions found in cement plants, and advancing its technology readiness level (TRL) to 6. GE Power as technology provider and ETHZ as research partner will collaborate in the study.
Experimental testing in a high-fidelity laboratory environment (GE Power-Sweden 1 t/day pilot plant) will be conducted and evaluated under realistic cement plant operational conditions. These test campaigns along with full process simulations, optimization and integration with the cement plant will enable the achievement of TRL6. In particular, the CO2 absorber, the NH3 recovery section, and the direct contact cooler (DCC) will be operated with cement plant flue gas, including typical cement impurities (i.e. dust, SOx and NOx). Optimal operating variables (e.g. temperature, liquid-to-gas ratio, ammonia loading in the lean solvent) and modifications to the existing absorber design (e.g. number of stages, temperature control) will be evaluated.
The knowledge acquired from power plant applications and the new simulation models adapted and validated with the pilot experimental campaigns will serve as basis for the design of full-scale plants. Additionally, the cooperation with WP4 will allow to assess the full cement plant running with the CAP, either greenfield or retrofitted; results will show the most suitable integration of the CAP within the cement plant, including the position in the flue gas line and alternatives for heat integration.
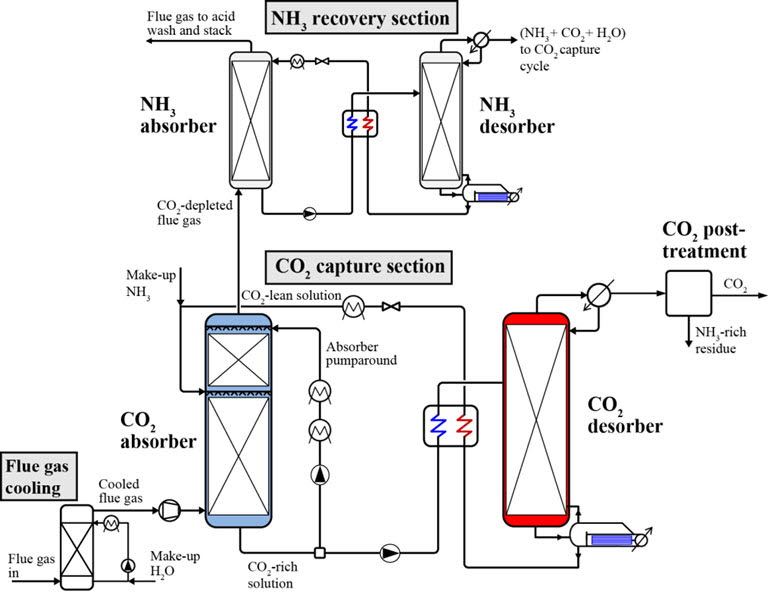