Objectives
The main objective of the PRINTCR3DIT project is to implement a methodology to integrate 3D printing in the advanced design, modelling and manufacture of structured catalysts and catalytic reactors with significant cost reductions, access to new design strategies and faster lead times.
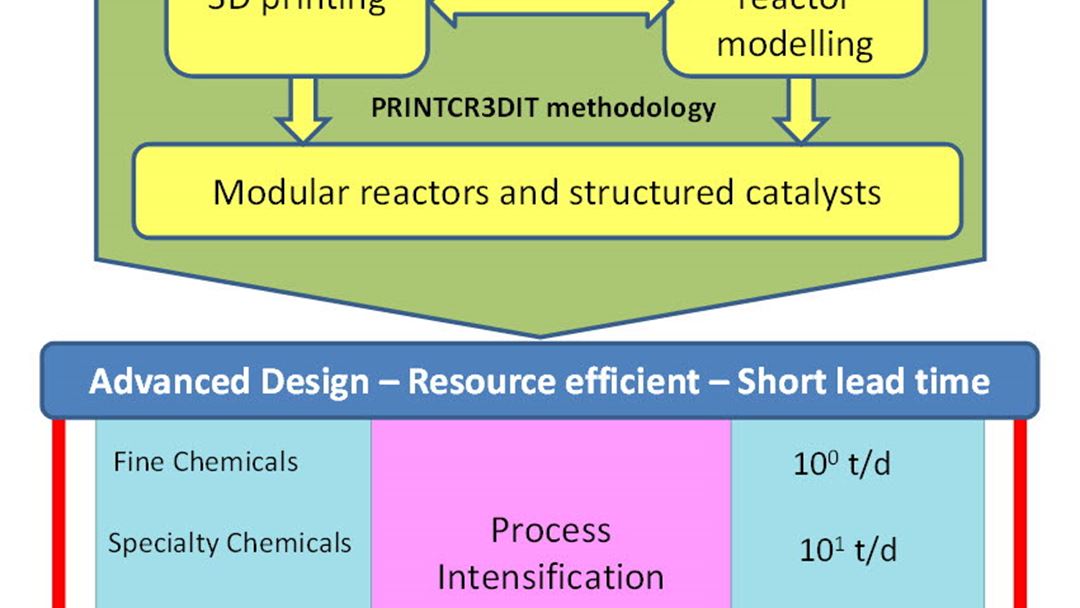
The principal target of the project is to increase the efficiency through process intensification in reactions that present heat, mass and momentum transfer limitations, with targeted goals to significantly reduce the energy consumption, increased selectivities and longer lifetimes. The utility and flexibility of the methodology will be demonstrated through three industrial processes that span different chemical sectors, scales of production and catalytic reactors. The selected examples will target the production of fine chemicals, commodity chemicals and fertilizers.
As shown in the figure abow, the concept of PRINTCR3DIT aims to achieve process intensification by combination of 3D printing of novel structured catalysts and reactors, integrated with advanced reactor modelling to maximize expected performance with reduced energy and emissions. In particular, this concept can bring major benefits in cases where strong limitations of mass, energy and/or momentum transfer constrain the optimal performance of current reactors and catalysts. The concept of the hybrid utilization of additive manufacturing has especially high impact in cases where optimal or innovative designs cannot be realized with traditional manufacturing approaches or when such designs are very expensive.